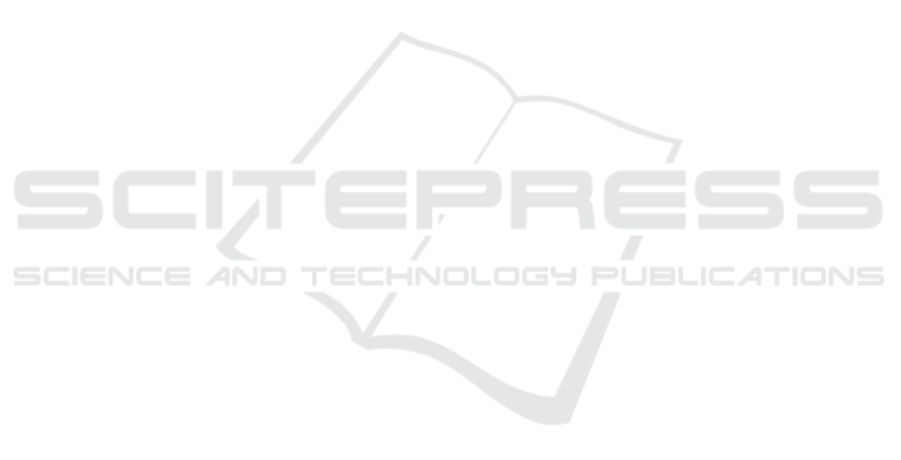
Recent developments in techniques and methodolo-
gies for improving thickener performance. Chemical
Engineering Journal, 80(1):149–155.
Gholaminejad, T., Khaki-Sedigh, A., and Bagheri, P.
(2016). Adaptive tuning of model predictive control
based on analytical results. In 2016 4th International
Conference on Control, Instrumentation, and Automa-
tion (ICCIA), pages 226–232.
Jin, Y. and Ding, F. (2023). 1. a coupled recursive least
squares algorithm for multivariable systems and its
computational amount analysis by using the coupling
identification concept. International Journal of Adap-
tive Control and Signal Processing.
Juan, I. and Aldo, C. (2019). Dynamic modeling and simu-
lation of tailing thickener units for the development of
control strategies. Minerals Engineering 131.
Kosonen, M., Kauvosaari, S., Gao, S., and Henriksson, B.
(2017). Performance optimization of paste thickening.
In Wu, A. and Jewell, R., editors, Paste 2017: Pro-
ceedings of the 20th International Seminar on Paste
and Thickened Tailings, pages 13–22, Beijing. Uni-
versity of Science and Technology Beijing.
Kouvaritakis, B. and Cannon, M. (2016). Model Predictive
Control. Springer International Publishing.
Landau, I. D., Lozano, R., Saad, M. M., and Karimi, A.
(2024). 2. adaptive control: Algorithms, analysis and
applications. arXiv.org.
Li, Z. and Gupta, R. (2023). 1. impacts of various hydraulic
and solid loading conditions on process capability of
sludge thickening with thickening centrifuges. Pro-
ceedings of the Water Environment Federation.
Mohseni, N., Nguyen, T. W., Ul Islam, S. A., Kolmanovsky,
I. V., and Bernstein, D. S. (2020). Active noise con-
trol for harmonic and broadband disturbances using
rls-based model predictive control. In 2020 American
Control Conference (ACC), pages 1393–1398.
Nagai, T., Tanaka, M., Oishi, T., and Kitazaki, T. (2018).
Thickener for obtaining high concentration slurry and
control method for same.
Nguyen, T. W., Islam, S. A. U., Bruce, A. L., Goel, A.,
Bernstein, D. S., and Kolmanovsky, I. (2020). Output-
feedback rls-based model predictive control *. pages
2395–2400. IEEE.
Ojeda, P., Bergh, L. G., and Torres, L. (2014). Intelligent
control of an industrial thickener. In 2014 13th Inter-
national Conference on Control Automation Robotics
& Vision (ICARCV), pages 505–510.
Oulhiq, R., Benjelloun, K., Kali, Y., and Saad, M. (2021).
Identification and control of an industrial thickener
using historical data. In 2021 International Multi-
Conference on Systems, Signals & Devices (SSD).
Oulhiq, R., Benjelloun, K., Kali, Y., Saad, M., and Griguer,
H. (2024). Constrained model predictive control of
an industrial high-rate thickener. Journal of Process
Control, 133:103147.
Pirouz, B., Javadi, S., and Seddon, K. (2017). 5. thickener
performance variability: underflow solids concentra-
tion and flowrate.
Ruuska, J., Nikula, R.-P., Ruhanen, E., Kauppi, J., Kau-
vosaari, S., and Kosonen, M. (2020). Data analysis of
a paste thickener. Open Engineering, 10(1):362–367.
Salamati, S. M., Salamati, S. A., Mahoor, M., and Salmasi,
F. R. (2017). Leveraging adaptive model predictive
controller for active cell balancing in li-ion battery.
In 2017 North American Power Symposium (NAPS),
pages 1–6.
Sanchez, J. M. (1981). 2. adaptive-predictive control sys-
tem.
Serova, N. V., Olyunina, T. V., Lysykh, M. P., Ermishkin,
V. A., and Smirnova, V. B. (2016). Thickening and
rheological properties of slurries as functions of the
oxidized nickel ore composition. Russian Metallurgy.
Tan, C. K., Bao, J., and Bickert, G. (2017). 5. a study on
model predictive control in paste thickeners with rake
torque constraint. Minerals Engineering.
Wang, L., Cheng, L., Yin, S., and Chen, J. (2024). Floccula-
tion, dewatering and sedimentation behaviour of mine
backfill slurry in deep cone thickener (dct). Journal of
Environmental Chemical Engineering, 12(2):112168.
Wang, Y. and Xiao, B. (2024). 3 - theory, experiment, and
equipment in tailings thickening process. In Wang, Y.
and Xiao, B., editors, Cemented Paste Backfill, pages
25–65. Elsevier.
Xie, D. D., Tong, X., Xie, X., Hou, K., and Li, J. Y.
(2015). Efficient application of automation technol-
ogy in thickener process. In Advanced Materials
Research, volume 1094, pages 441–444. Trans Tech
Publications, Ltd.
Xu, J. N., Zhao, Z. B., and Wang, F. Q. (2017). Data
driven control of underflow slurry concentration in
deep cone thickener. In 2017 6th Data Driven Con-
trol and Learning Systems (DDCLS), pages 690–693.
Zaki, N., Hadoudi, N., Charki, A., Bensitel, N., Ouarghi,
H. E., Amhamdi, H., and Ahari, M. (2023). Ad-
vancements in the chemical treatment of potable
water and industrial wastewater using the coagula-
tion–flocculation process. Separation Science and
Technology, 58(15–16):2619–2630.
Ziemann, V. (2023). 2. simulations of real-time system
identification for superconducting cavities with a re-
cursive least-squares algorithm. Physical review ac-
celerators and beams.
Advanced Predictive Process Control for Industrial Thickeners
269