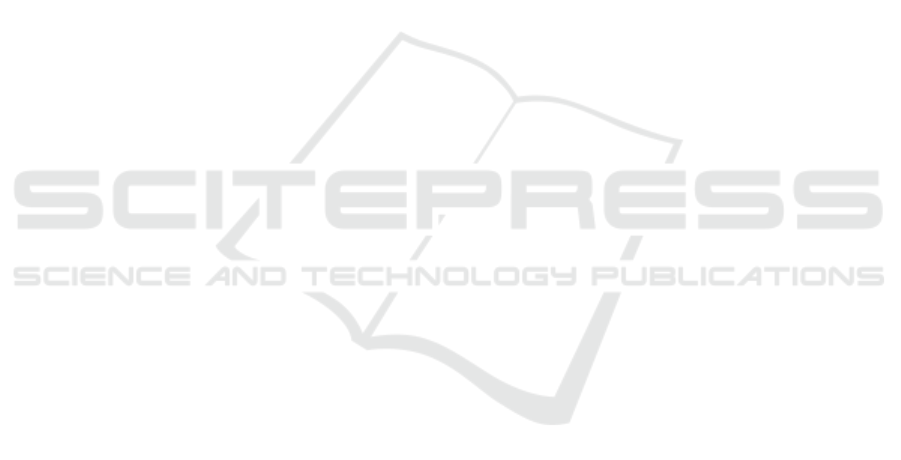
REFERENCES
Alharthi, N. W. and Brand
˜
ao, M. (2024). Physical and dig-
ital adversarial attacks on grasp quality networks. In
International Conference on Robotics and Automation
(ICRA), pages 1907–1902. IEEE.
Arias-P
´
erez, J. and V
´
elez-Jaramillo, J. (2022). Ignor-
ing the three-way interaction of digital orientation,
not-invented-here syndrome and employee’s artificial
intelligence awareness in digital innovation perfor-
mance: A recipe for failure. Technological Forecast-
ing and Social Change, 174:121305.
Bolstorff, P. and Rosenbaum, R. (2007). Supply chain ex-
cellence: A handbook for dramatic improvement us-
ing the scor model. Journal of Supply Chain Manage-
ment, 39(4):38.
Brandt, D. R. and Scharioth, J. (1998). Attribute life cycle
analysis. alternatives to the kano method. In Market-
ing Research Congress, pages 413–430. ESOMAR.
Chitturi, R., Raghunathan, R., and Mahajan, V. (2008). De-
light by design: The role of hedonic versus utilitarian
benefits. Journal of marketing, 72(3):48–63.
Chryssolouris, G., Alexopoulos, K., and Arkouli, Z. (2023).
Artificial intelligence in manufacturing systems. In A
Perspective on Artificial Intelligence in Manufactur-
ing, pages 79–135. Springer.
Culot, G., Orzes, G., Sartor, M., and Nassimbeni, G. (2020).
The future of manufacturing: A delphi-based scenario
analysis on industry 4.0. Technological forecasting
and social change, 157:120092.
Demlehner, Q., Schoemer, D., and Laumer, S. (2021). How
can artificial intelligence enhance car manufacturing?
a delphi study-based identification and assessment of
general use cases. International Journal of Informa-
tion Management, 58:102317.
El Naqa, I. and Murphy, M. (2015). What is machine learn-
ing? In Machine Learning in Radiation Oncology,
pages 3–11.
Espina-Romero, L., Guti
´
errez Hurtado, H., R
´
ıos Parra,
D., Vilchez Pirela, R. A., Talavera-Aguirre, R., and
Ochoa-D
´
ıaz, A. (2024). Challenges and opportunities
in the implementation of ai in manufacturing: A bib-
liometric analysis. Sci, 6(4):60.
Ge, Z., Song, Z., Ding, S. X., and Huang, B. (2017). Data
mining and analytics in the process industry: The role
of machine learning. IEEE Access, 5:20590–20616.
Hasan, S. M., Shahid, A. R., and Imteaj, A. (2024). Evaluat-
ing sustainability and social costs of adversarial train-
ing in machine learning. IEEE Consumer Electronics
Magazine.
Jaiswal, A., Arun, C. J., and Varma, A. (2023). Reboot-
ing employees: Upskilling for artificial intelligence in
multinational corporations. In Artificial Intelligence
and International HRM, pages 114–143. Routledge.
Jeziorek, O. (1994). Lean production. Lean Production,
pages 3–27.
Kilkenny, M. F. and Robinson, K. M. (2018). Data qual-
ity:“garbage in–garbage out”.
Kotsiantis, S. B., Zaharakis, I., Pintelas, P., et al. (2007). Su-
pervised machine learning: A review of classification
techniques. Emerging Artificial Intelligence Applica-
tions in Computer Engineering, 160(1):3–24.
Kovalenko, I., Barton, K., Moyne, J., and Tilbury, D. M.
(2023). Opportunities and challenges to integrate
artificial intelligence into manufacturing systems:
Thoughts from a panel discussion [opinion]. Robotics
& Automation Magazine, 30(2):109–112.
Kovi
ˇ
c, K., Tominc, P., Prester, J., and Pal
ˇ
ci
ˇ
c, I. (2024). Arti-
ficial intelligence software adoption in manufacturing
companies. Applied Sciences, 14(16):6959.
Kusiak, A. (2018). Smart manufacturing. International
Journal of Production Research, 56:508 – 517.
Kutz, J., Neuh
¨
uttler, J., Spilski, J., and Lachmann,
T. (2022). Implementation of ai technologies in
manufacturing-success factors and challenges. In In-
ternational Conference on Applied Human Factors
and Ergonomics (AHFE), pages 24–28.
Lee, W.-Y., Lee, Y., Jeong, J. S., Yu, G.-I., Kim, J. Y.,
Park, H. J., Jeon, B., Song, W., Kim, G., Weimer,
M., et al. (2019). Automating system configuration of
distributed machine learning. In International Con-
ference on Distributed Computing Systems (ICDCS),
pages 2057–2067. IEEE.
Lepore, D., Dubbini, S., Micozzi, A., and Spigarelli, F.
(2022). Knowledge sharing opportunities for indus-
try 4.0 firms. Journal of the Knowledge Economy,
13(1):501–520.
Li, Y., Cheng, M., Hsieh, C.-J., and Lee, T. C. M. (2022). A
review of adversarial attack and defense for classifica-
tion methods. The American Statistician, 76(4):329–
345.
L
´
opez Mart
´
ınez, P., Barros, L., and Drake, J. M. (2010).
Scheduling configuration of real-time component-
based applications. In International Conference on
Reliable Software Technologies (Ada-Europe), pages
181–195. Springer.
May, R. and Adler, S. (2024). Experiences in develop-
ing configurable digital twin-assisted xR applications
for industrial environments. In International Work-
ing Conference on Variability Modelling of Software-
Intensive Systems (VaMoS), pages 1–5. ACM.
May, R., Alex, A., Suresh, R., and Leich, T. (2024a).
Product-line engineering for smart manufacturing: A
systematic mapping study on security concepts. In In-
ternational Conference on Software Technologies (IC-
SOFT), pages 323–330. SciTePress.
May, R. et al. (2023a). A systematic mapping study on se-
curity in configurable safety-critical systems based on
product-line concepts. In International Conference
of Software Technologies (ICSOFT), pages 217–224.
SciTePress.
May, R., Kr
¨
uger, J., and Leich, T. (2024b). Sok: How
artificial-intelligence incidents can jeopardize safety
and security. In International Conference on Avail-
ability, Reliability and Security (ARES), pages 1–12.
ACM.
May, R., Niemand, T., Scholz, P., and Leich, T. (2023b).
Design patterns for monitoring and prediction ma-
chine learning systems: Systematic literature review
and cluster analysis. In International Conference
Adopting Artificial-Intelligence Systems in Manufacturing: A Practitioner Survey on Challenges and Added Value
97