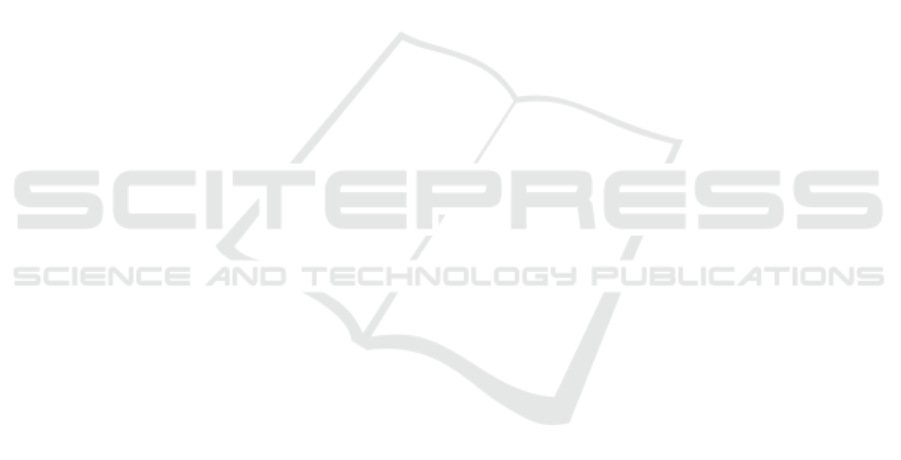
resources in storage, resulting in a steady increase in
energy consumption and production over time. How-
ever, it exhibited limitations in maximizing efficiency
compared to more advanced methods. The Pareto-
based Selection method balanced input prices with re-
source availability, leading to more efficient produc-
tion outcomes and higher economic activity. Lastly,
the Pareto Optimization approach, as the most ad-
vanced method, consistently minimized operational
costs while maximizing production efficiency, yield-
ing the highest total price sales and demonstrating op-
timal energy use.
The findings highlight the significance of multi-
objective optimization in improving resource man-
agement and production processes in chemical indus-
tries. By leveraging Pareto Optimization, companies
can achieve a more balanced approach to energy use
and resource allocation, ultimately enhancing both
economic and environmental sustainability. However,
the study also acknowledges that real-world complex-
ities, such as market fluctuations and logistical con-
straints indicating areas for further improvement.
Based on the results, it is recommended that
chemical production facilities adopt multi-objective
optimization techniques like Pareto Optimization to
enhance operational efficiency and sustainability. Fu-
ture research should focus on incorporating dynamic
market conditions, transportation logistics, and re-
newable energy sources into optimization models.
Additionally, considering regulatory and economic
factors, such as carbon pricing and subsidies, will of-
fer a more comprehensive view of sustainability in
chemical production. By adopting these improve-
ments, industries can better align with global sustain-
ability goals while maintaining economic viability.
ACKNOWLEDGEMENTS
We would like to thank all our partners of the project
Carbon2Chem
®
for the pleasant and successful in-
terdisciplinary collaboration. Also, we would like to
thank the Federal Ministry of Education and Research
(BMBF) for funding the project Carbon2Chem
®
(project number 03EK3037D).
REFERENCES
Aghaie, A. and Hajian Heidary, M. (2019). Simulation-
based optimization of a stochastic supply chain con-
sidering supplier disruption: Agent-based model-
ing and reinforcement learning. Scientia Iranica,
26(6):3780–3795.
El-Shafie, M. (2023). Hydrogen production by water elec-
trolysis technologies: A review. Results in Engineer-
ing, page 101426.
Fadillah, G., Alarifi, N. T., Suryawan, I. W. K., and Saleh,
T. A. (2024). Advances in designed reactors for water
treatment process: A review highlighting the designs
and performance. Journal of Water Process Engineer-
ing, 63:105417.
Haleem, A., Javaid, M., Singh, R. P., Suman, R., and Qadri,
M. A. (2023). A pervasive study on green manufactur-
ing towards attaining sustainability. Green Technolo-
gies and Sustainability, 1(2):100018.
Helo, P. and Rouzafzoon, J. (2023). An agent-based sim-
ulation and logistics optimization model for manag-
ing uncertain demand in forest supply chains. Supply
Chain Analytics, 4:100042.
Ionescu, S¸., Delcea, C., Chirit¸
˘
a, N., and Nica, I. (2024). Ex-
ploring the use of artificial intelligence in agent-based
modeling applications: A bibliometric study. Algo-
rithms, 17(1):21.
Long, Q. (2014). Distributed supply chain network mod-
elling and simulation: integration of agent-based dis-
tributed simulation and improved scor model. Inter-
national journal of production research, 52(23):6899–
6917.
Mishra, K., Siwal, S. S., Nayaka, S. C., Guan, Z., and
Thakur, V. K. (2023). Waste-to-chemicals: Green so-
lutions for bioeconomy markets. Science of The Total
Environment, 887:164006.
Okunlola, A., Davis, M., and Kumar, A. (2023). Assess-
ing the cost competitiveness of electrolytic hydrogen
production from small modular nuclear reactor-based
power plants: A price-following perspective. Applied
Energy, 346:121290.
Singh, V., Buelens, L. C., Poelman, H., Saeys, M., Marin,
G. B., and Galvita, V. V. (2022). Carbon monoxide
production using a steel mill gas in a combined chem-
ical looping process. Journal of Energy Chemistry,
68:811–825.
Sollai, S., Porcu, A., Tola, V., Ferrara, F., and Pettinau, A.
(2023). Renewable methanol production from green
hydrogen and captured co2: A techno-economic as-
sessment. Journal of CO2 Utilization, 68:102345.
Venkataramanan, V. S. and Srinivasan, R. (2024). Agent-
based dynamic simulation for supply chain manage-
ment of lng import terminals. Industrial & Engineer-
ing Chemistry Research, 63(6):2750–2768.
Zhou, L., Chen, G., Zheng, M., Gao, X., Luo, C., and
Rao, X. (2024). Agent-based modeling methodology
and temporal simulation for natech events in chemi-
cal clusters. Reliability Engineering & System Safety,
243:109888.
Zhu, M., Yang, G., Jiang, Y., and Wang, X. (2023). Agent-
based modeling for water–energy–food nexus and its
application in ningdong energy and chemical base.
Sustainability, 15(14):11428.
SIMULTECH 2025 - 15th International Conference on Simulation and Modeling Methodologies, Technologies and Applications
158