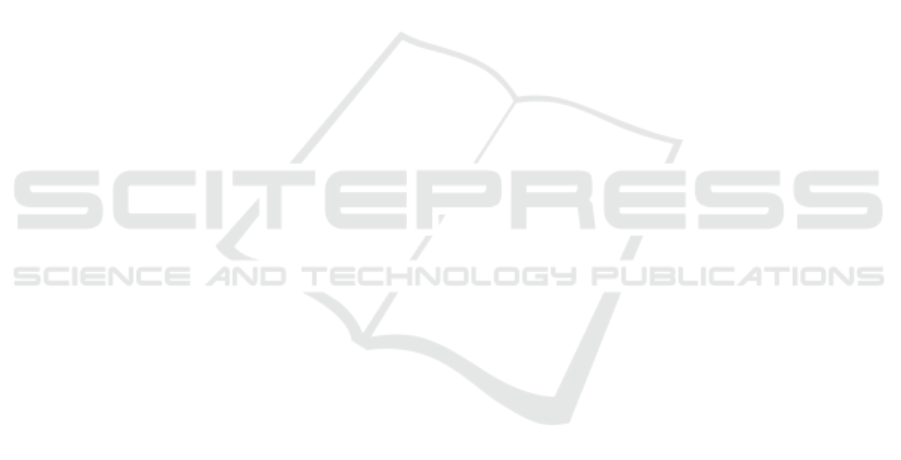
dence. Journal of Systems Engineering and Electron-
ics, 26(3):493–501.
Gobbi, C. (2011). Designing the reverse supply chain: the
impact of the product residual value. International
Journal of Physical Distribution & Logistics Manage-
ment, 41:768–796.
Guide, V. D. R. and Wassenhove, L. N. (2003). Busi-
ness aspects of closed-loop supply chains, volume 12.
Carnegie Mellon University Press Pittsburgh, PA.
Gunn, E. A. and Diallo, C. (2015). Optimal opportunistic
indirect grouping of preventive replacements in mul-
ticomponent systems. Computers & Industrial Engi-
neering, 90:281–291.
Guo, Y., Shi, Q., and Guo, C. (2022). A fuzzy robust pro-
gramming model for sustainable closed-loop supply
chain network design with efficiency-oriented multi-
objective optimization. Processes, 10(10):1963.
Haque, S. A., Kabir, A. Z., and Sarker, R. A. (2003). Opti-
mization model for opportunistic replacement policy
using genetic algorithm with fuzzy logic controller.
In The 2003 Congress on Evolutionary Computation,
2003. CEC’03., volume 4, pages 2837–2843. IEEE.
Issa, L. A. A. A. and Hassan, Z. A. H. (2023). Application
of markov models to maintenance-required systems.
In AIP Conference Proceedings, volume 2591, page
050012. AIP Publishing LLC.
Jiang, R. and Ji, P. (2002). Age replacement policy: a multi-
attribute value model. Reliability Engineering & Sys-
tem Safety, 76(3):311–318.
Kabir, S. (2017). An overview of fault tree analysis and
its application in model based dependability analysis.
Expert Systems with Applications, 77:114–135.
Lebrun, R. and Dutfoy, A. (2009). An innovating analysis
of the nataf transformation from the copula viewpoint.
Probabilistic Engineering Mechanics, 24(3):312–320.
Li, D.-Q., Wu, S.-B., Zhou, C.-B., and Phoon, K. (2012).
Performance of translation approach for modeling
correlated non-normal variables. Structural safety,
39:52–61.
Li, H., L
¨
u, Z., and Yuan, X. (2008). Nataf transformation
based point estimate method. Chinese Science Bul-
letin, 53(17):2586–2592.
Li, M., Jiang, X., and Negenborn, R. R. (2021). Op-
portunistic maintenance for offshore wind farms with
multiple-component age-based preventive dispatch.
Ocean Engineering, 231:109062.
Lin, S.-W., Matanhire, T. B., and Liu, Y.-T. (2021). Copula-
based bayesian reliability analysis of a product of a
probability and a frequency model for parallel systems
when components are dependent. Applied Sciences,
11(4):1697.
Lin, X., Jiang, Y., Peng, S., Chen, H., Tang, J., and Li,
W. (2020). An efficient nataf transformation based
probabilistic power flow for high-dimensional cor-
related uncertainty sources in operation. Interna-
tional Journal of Electrical Power & Energy Systems,
116:105543.
Liu, P.-L. and Der Kiureghian, A. (1986). Multivari-
ate distribution models with prescribed marginals and
covariances. Probabilistic engineering mechanics,
1(2):105–112.
Navarro, J. and Durante, F. (2017). Copula-based represen-
tations for the reliability of the residual lifetimes of
coherent systems with dependent components. Jour-
nal of Multivariate Analysis, 158:87–102.
Rebaiaia, M.-L. and Ait-Kadi, D. (2022). A remaining
useful life model for optimizing maintenance cost
and spare-parts replacement of production systems
in the context of sustainability. IFAC-PapersOnLine,
55(10):1562–1568.
Sasirekha, K. and Baby, P. (2013). Agglomerative hierar-
chical clustering algorithm-a. International Journal
of Scientific and Research Publications, 83(3):83.
Simpson, K. and Kelly, M. (2002). Reliability assessments
of repairable systems—is markov modelling correct?
In Safety and Reliability, volume 22, pages 19–39.
Taylor & Francis.
Son, K. S., Kim, D. H., Kim, C. H., and Kang, H. G. (2016).
Study on the systematic approach of markov modeling
for dependability analysis of complex fault-tolerant
features with voting logics. Reliability Engineering
& System Safety, 150:44–57.
Souza, G. C. (2013). Closed-loop supply chains: a crit-
ical review, and future research. Decision Sciences,
44(1):7–38.
Tahirov, N., Hasanov, P., and Jaber, M. Y. (2016). Opti-
mization of closed-loop supply chain of multi-items
with returned subassemblies. International Journal of
Production Economics, 174:1–10.
van Nunen, T. M. S. M. (1995). J van wassenhove l strategic
issues in product recovery management. California
Management Review, 372:114–135.
Wang, C., Xing, L., and Levitin, G. (2013). Reliability anal-
ysis of multi-trigger binary systems subject to compet-
ing failures. Reliability Engineering & System Safety,
111:9–17.
Wang, J., Miao, Y., Yi, Y., and Huang, D. (2021). An im-
perfect age-based and condition-based opportunistic
maintenance model for a two-unit series system. Com-
puters & Industrial Engineering, 160:107583.
Xiao, Q. (2014). Evaluating correlation coefficient for nataf
transformation. Probabilistic Engineering Mechanics,
37:1–6.
Zhang, J., Kang, J., Sun, L., and Bai, X. (2021a). Risk
assessment of floating offshore wind turbines based
on fuzzy fault tree analysis. Ocean Engineering,
239:109859.
Zhang, X.-m., Li, Q.-w., Liu, Z., and Chang, C.-T.
(2021b). Optimal pricing and remanufacturing mode
in a closed-loop supply chain of weee under govern-
ment fund policy. Computers & Industrial Engineer-
ing, 151:106951.
Integrating Reliability and Sustainability: A Multi-Objective Framework for Opportunistic Maintenance in Closed-Loop Supply Chain
189