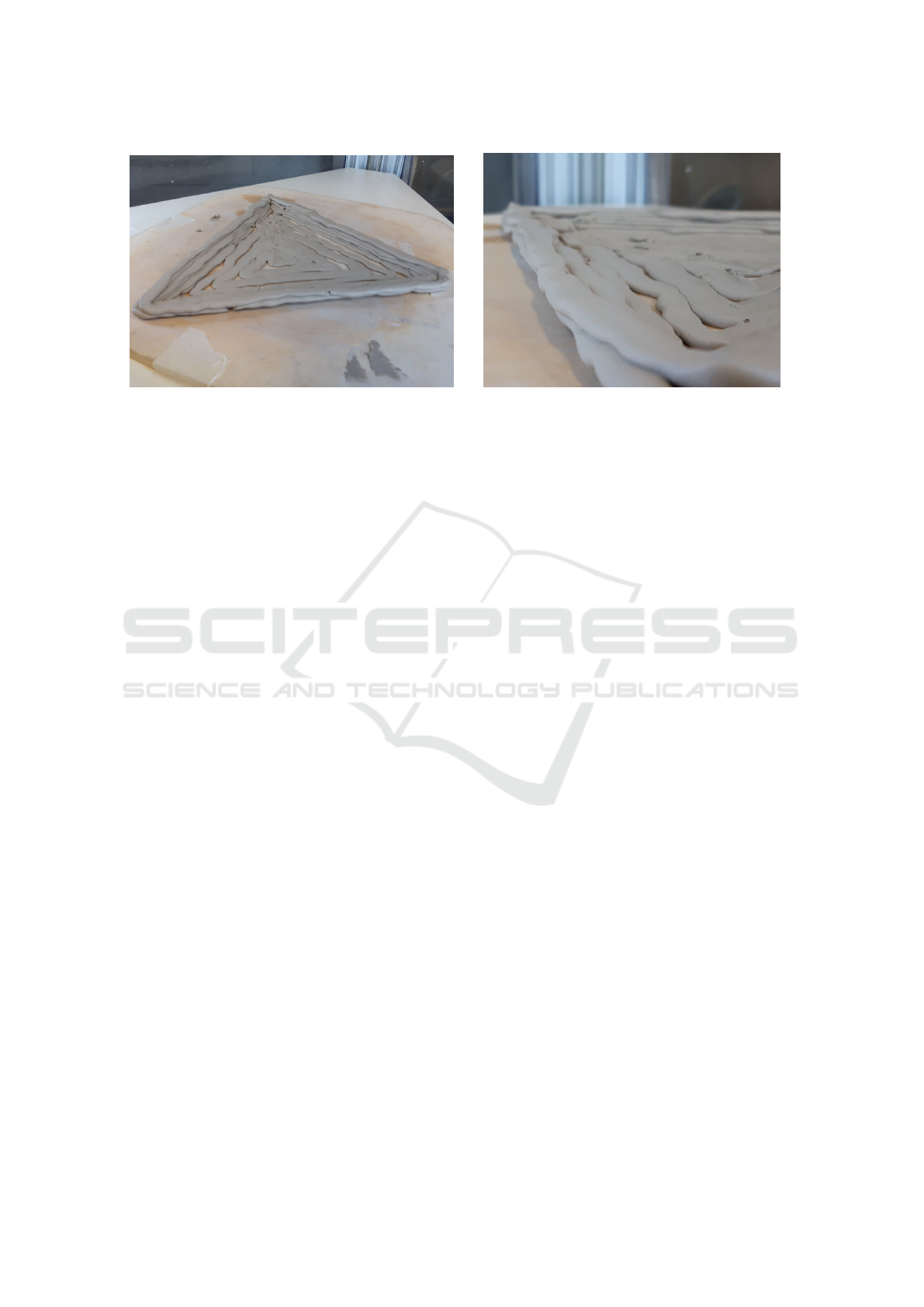
(a) (b)
Figure 6: Preliminary example of a clay pot produced using a 3D printer.
exchange, and the potential for artisans to collaborate
on collaborative projects.
REFERENCES
Balan, L., Yuen, T., and Mehrtash, M. (2019). Problem-
based learning strategy for cad software using free-
choice and open-ended group projects. Procedia Man-
ufacturing, 32:339–347.
Bernardo, A. (2017). Virtual reality and simulation in neu-
rosurgical training. World neurosurgery, 106:1015–
1029.
Camacho, D. D., Clayton, P., O’Brien, W. J., Seepersad, C.,
Juenger, M., Ferron, R., and Salamone, S. (2018). Ap-
plications of additive manufacturing in the construc-
tion industry–a forward-looking review. Automation
in construction, 89:110–119.
Capece, N., Erra, U., and Romaniello, G. (2018). A low-
cost full body tracking system in virtual reality based
on microsoft kinect. In De Paolis, L. T. and Bourdot,
P., editors, Augmented Reality, Virtual Reality, and
Computer Graphics, pages 623–635, Cham. Springer
International Publishing.
Castro e Costa, E., Duarte, J. P., and B
´
artolo, P. (2017). A
review of additive manufacturing for ceramic produc-
tion. Rapid Prototyping Journal, 23(5):954–963.
Dashti, S., Prakash, E., Navarro-Newball, A. A., Hussain,
F., and Carroll, F. (2022). Potteryvr: Virtual reality
pottery. Vis. Comput., 38(12):4035–4055.
Erra, U., Malandrino, D., and Pepe, L. (2018). A method-
ological evaluation of natural user interfaces for im-
mersive 3d graph explorations. Journal of Visual Lan-
guages & Computing, 44:13–27.
Featherstone, R. (2014). Rigid Body Dynamics Algorithms.
Springer US.
Florian, H. and Andrea, I. Clayxels. Online available at:
https://www.clayxels.com/.
H
¨
oll, M., Oberweger, M., Arth, C., and Lepetit, V. (2018).
Efficient physics-based implementation for realistic
hand-object interaction in virtual reality. In 2018
IEEE conference on virtual reality and 3D user inter-
faces (VR), pages 175–182. IEEE.
Ming, C., Mirjan, A., Medina Ib
´
a
˜
nez, J., Gramazio, F., and
Kohler, M. (2022). Impact printing. 3D Printing and
Additive Manufacturing, 9(3):203–211.
Mujber, T. S., Szecsi, T., and Hashmi, M. S. (2004). Vir-
tual reality applications in manufacturing process sim-
ulation. Journal of materials processing technology,
155:1834–1838.
Ostrander, J. K., Ryan, L., Dhengre, S., McComb, C., Simp-
son, T. W., and Meisel, N. A. (2019). A comparative
study of virtual reality and computer-aided design to
evaluate parts for additive manufacturing. In Interna-
tional Design Engineering Technical Conferences and
Computers and Information in Engineering Confer-
ence, volume 59186, page V02AT03A029. American
Society of Mechanical Engineers.
Ostrander, J. K., Tucker, C. S., Simpson, T. W., and Meisel,
N. A. (2020). Evaluating the use of virtual reality
to teach introductory concepts of additive manufactur-
ing. Journal of Mechanical Design, 142(5):051702.
Perrot, A., Rangeard, D., and Courteille, E. (2018). 3d
printing of earth-based materials: Processing aspects.
Construction and Building Materials, 172:670–676.
Peterson, S. and Peterson, J. (2003). The Craft and Art of
Clay: A Complete Potter’s Handbook. Laurence King.
Rayna, T. and Striukova, L. (2016). From rapid prototyp-
ing to home fabrication: How 3d printing is changing
business model innovation. Technological Forecasting
and Social Change, 102:214–224.
Renner, A., Holub, J., Sridhar, S., Evans, G., and Winer,
E. (2015). A virtual reality application for additive
manufacturing process training. In International De-
sign Engineering Technical Conferences and Comput-
ers and Information in Engineering Conference, vol-
ume 57045, page V01AT02A033. American Society
of Mechanical Engineers.
Song, P., Yu, H., and Winkler, S. (2008). Vision-
based 3d finger interactions for mixed reality games
with physics simulation. In Proceedings of the 7th
ACM SIGGRAPH international conference on virtual-
reality continuum and its applications in industry,
pages 1–6.
ARTISTA: Redefining Pottery Design with Virtual Reality and Physically Simulated Clay
499