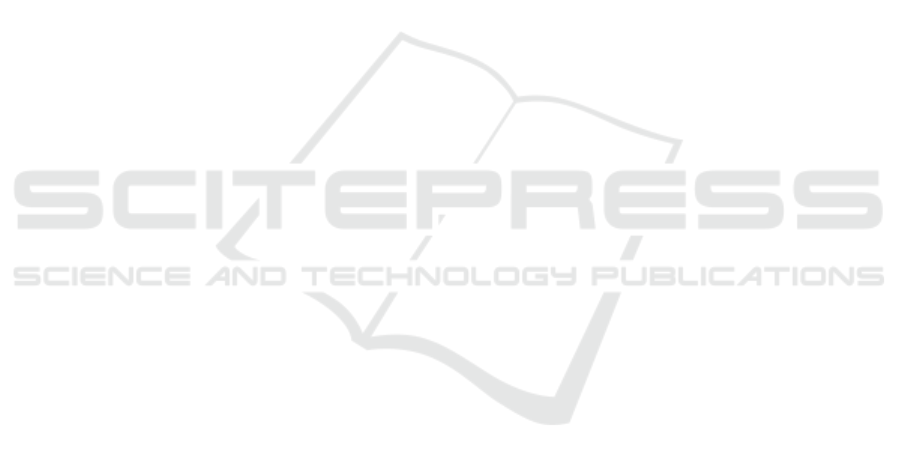
sponding movement to the physical robot by pressing
a designated VR button. This process can enhance the
existing human-robot collaboration schemes in terms
of of human safety and robot integrity (avoiding dam-
age).
ACKNOWLEDGMENTS
The work presented in this paper was supported by
the European Commission under contract H2020 -
101016953 CoRoSect.
REFERENCES
Angelov, V., Petkov, E., Shipkovenski, G., and Kalushkov,
T. (2020). Modern virtual reality headsets. In 2020 In-
ternational congress on human-computer interaction,
optimization and robotic applications (HORA), pages
1–5. IEEE.
Aoun, A., Ilinca, A., Ghandour, M., and Ibrahim, H. (2021).
A review of industry 4.0 characteristics and chal-
lenges, with potential improvements using blockchain
technology. Computers & Industrial Engineering,
162:107746.
Bauer, A., Wollherr, D., and Buss, M. (2008). Human–
robot collaboration: a survey. International Journal
of Humanoid Robotics, 5(01):47–66.
Bland, J. M. and Altman, D. G. (1997). Statistics notes:
Cronbach’s alpha. Bmj, 314(7080):572.
Bowman, D. A. and McMahan, R. P. (2007). Virtual re-
ality: How much immersion is enough? Computer,
40(7):36–43.
Braganc¸a, S., Costa, E., Castellucci, I., and Arezes, P. M.
(2019). A brief overview of the use of collaborative
robots in industry 4.0: human role and safety. Occu-
pational and environmental safety and health, pages
641–650.
Colgate, J. E., Wannasuphoprasit, W., and Peshkin, M. A.
(1996). Cobots: Robots for collaboration with hu-
man operators. In ASME international mechanical
engineering congress and exposition, volume 15281,
pages 433–439. American Society of Mechanical En-
gineers.
Dascal, J., Reid, M., IsHak, W. W., Spiegel, B., Recacho,
J., Rosen, B., and Danovitch, I. (2017). Virtual re-
ality and medical inpatients: A systematic review of
randomized, controlled trials. Innov. Clin. Neurosci.,
14(1-2):14–21.
Garcia, C. A., Naranjo, J. E., Ortiz, A., and Garcia, M. V.
(2019). An approach of virtual reality environment
for technicians training in upstream sector. Ifac-
Papersonline, 52(9):285–291.
Haas, J. K. (2014). A history of the unity game engine.
Hochhalter, J., Leser, W. P., Newman, J. A., Gupta, V. K.,
Yamakov, V., Cornell, S. R., Williard, S. A., and
Heber, G. (2014). Coupling damage-sensing particles
to the digitial twin concept - nasa technical reports
server (ntrs).
HTC (2011). Htc vive. Accessed on April 2023.
Kim, M., Jeon, C., and Kim, J. (2017). A study on immer-
sion and presence of a portable hand haptic system for
immersive virtual reality. Sensors, 17(5).
Kusiak, A. (2017). Smart manufacturing must embrace big
data. Nature, 544:23–25.
Laith K Hasan, Aryan Haratian, M. K. I. K. B. A. E. W. and
Petrigliano, F. A. (2021). Virtual reality in orthopedic
surgery training. Advances in Medical Education and
Practice, 12:1295–1301.
Lasi, H., Fettke, P., Kemper, H.-G., Feld, T., and Hoff-
mann, M. (2014). Industry 4.0. Bus. Inf. Syst. Eng.,
6(4):239–242.
Magnus Sundgot Schneider, K. O. S., Kurz, K. D., Dalen,
I., Ospel, J., Goyal, M., Kurz, M. W., and Fjetland,
L. (2023). Metric based virtual simulation training for
endovascular thrombectomy improves interventional
neuroradiologists’ simulator performance. Interven-
tional Neuroradiology, 29(5):577–582.
Mantovani, F., Castelnuovo, G., Gaggioli, A., and Riva, G.
(2003). Virtual reality training for health-care profes-
sionals. Cyberpsychology & behavior: the impact of
the Internet, multimedia and virtual reality on behav-
ior and society, 6:389–95.
Martinez-Hernandez, U. and Al, G. A. (2022). Wearable
fingertip with touch, sliding and vibration feedback
for immersive virtual reality. In 2022 IEEE Interna-
tional Conference on Systems, Man, and Cybernetics
(SMC), pages 293–298.
Matheson, E., Minto, R., Zampieri, E. G., Faccio, M.,
and Rosati, G. (2019). Human–robot collaboration
in manufacturing applications: A review. Robotics,
8(4):100.
Oyekan, J. O., Hutabarat, W., Tiwari, A., Grech, R., Aung,
M. H., Mariani, M. P., L
´
opez-D
´
avalos, L., Ricaud,
T., Singh, S., and Dupuis, C. (2019). The effec-
tiveness of virtual environments in developing collab-
orative strategies between industrial robots and hu-
mans. Robotics and Computer-Integrated Manufac-
turing, 55:41–54.
O’Connor, S. (2019). Virtual reality and avatars in health
care. Clinical Nursing Research, 28(5):523–528.
P
´
erez, L., Diez, E., Usamentiaga, R., and Garc
´
ıa, D. F.
(2019). Industrial robot control and operator training
using virtual reality interfaces. Computers in Industry,
109:114–120.
Qi, Q. and Tao, F. (2018). Digital twin and big data to-
wards smart manufacturing and industry 4.0: 360 de-
gree comparison. IEEE Access, 6:3585–3593.
Robla-G
´
omez, S., Becerra, V. M., Llata, J. R., Gonz
´
alez-
Sarabia, E., Torre-Ferrero, C., and P
´
erez-Oria, J.
(2017). Working together: A review on safe human-
robot collaboration in industrial environments. IEEE
Access, 5:26754–26773.
Salas, E., Wilson, K. A., Burke, C. S., and Priest, H. A.
(2005). Using simulation-based training to improve
Leveraging VR and Force-Haptic Feedback for an Effective Training with Robots
659