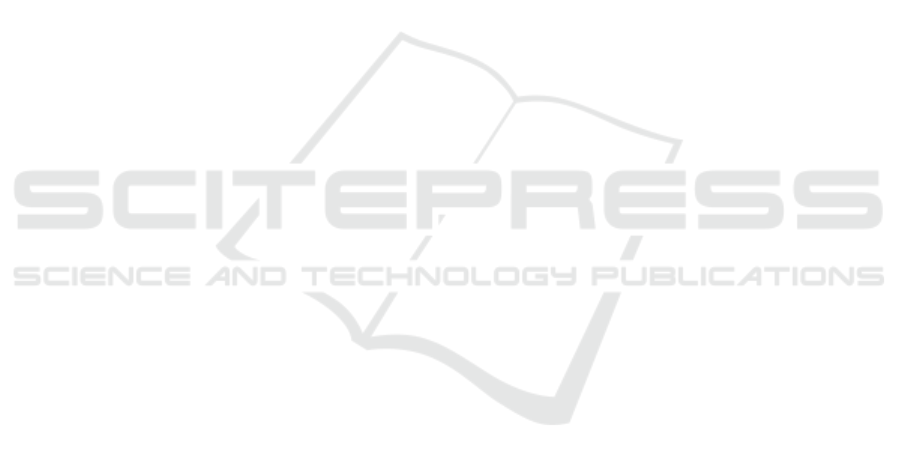
on Machine Learning Production Scheduling.
Processes, 10(3). https://doi.org/10.3390/pr10030520
Fu, Y., Tian, G., Fathollahi-Fard, A. M., Ahmadi, A., &
Zhang, C. (2019). Stochastic multi-objective modelling
and optimization of an energy-conscious distributed
permutation flow shop scheduling problem with the
total tardiness constraint. Journal of Cleaner
Production, 226, 515–525. https://doi.org/10.
1016/j.jclepro.2019.04.046
Gao, S., Daaboul, J., & Le Duigou, J. (2021). Process
planning, scheduling, and layout optimization for
multi-unit mass-customized products in sustainable
reconfigurable manufacturing system. Sustainability
(Switzerland), 13(23). https://doi.org/10.3390/su1323
13323
Giret, A., Trentesaux, D., & Prabhu, V. (2015).
Sustainability in manufacturing operations scheduling:
A state of the art review. Journal of Manufacturing
Systems, 37, 126–140. https://doi.org/10.1016/j.
jmsy.2015.08.002
Janga Reddy, M., & Nagesh Kumar, D. (2020).
Evolutionary algorithms, swarm intelligence methods,
and their applications in water resources engineering: A
state-of-the-art review. In H2Open Journal (Vol. 3,
Issue 1, pp. 135–188). IWA Publishing.
https://doi.org/10.2166/h2oj.2020.128
Jiang, T., Zhang, C., & Sun, Q. M. (2019). Green Job Shop
Scheduling Problem with Discrete Whale Optimization
Algorithm. IEEE Access, 7, 43153–43166.
https://doi.org/10.1109/ACCESS.2019.2908200
Khaled, M. S., Shaban, I. A., Karam, A., Hussain, M.,
Zahran, I., & Hussein, M. (2022). An Analysis of
Research Trends in the Sustainability of Production
Planning. Energies, 15(2). https://doi.org/10.3390/
en15020483
Li, Y. Z., Pan, Q. K., Gao, K. Z., Tasgetiren, M. F., Zhang,
B., & Li, J. Q. (2021). A green scheduling algorithm for
the distributed flowshop problem. Applied Soft
Computing, 109. https://doi.org/10.1016/j.asoc.
2021.107526
Lu, C., Gao, L., Gong, W., Hu, C., Yan, X., & Li, X. (2021).
Sustainable scheduling of distributed permutation flow-
shop with non-identical factory using a knowledge-
based multi-objective memetic optimization algorithm.
Swarm and Evolutionary Computation, 60.
https://doi.org/10.1016/j.swevo.2020.100803
Lu, C., Gao, L., Li, X., Pan, Q., & Wang, Q. (2017).
Energy-efficient permutation flow shop scheduling
problem using a hybrid multi-objective backtracking
search algorithm. Journal of Cleaner Production, 144,
228–238. https://doi.org/10.1016/j.jclepro.2017.01.011
Marimin, & Farhan, M. N. (2020). Sustainable flexible flow
shop scheduling optimization in flexible packaging
industry using genetic algorithm. IOP Conference
Series: Earth and Environmental Science, 472(1).
https://doi.org/10.1088/1755-1315/472/1/012050
Piroozfard, H., Yew Wong, K., & Tiwari, K. (2018).
Reduction of carbon emission and total late work
criterion in job shop scheduling by applying a multi-
objective imperialist competitive algorithm.
Piwowar-Sulej, K. (2022). Environmental strategies and
human resource development consistency: Research in
the manufacturing industry. Journal of Cleaner
Production, 330. https://doi.org/10.1016/j.jclepro.
2021.129538
Renna, P., & Materi, S. (2021). A literature review of
energy efficiency and sustainability in manufacturing
systems. In Applied Sciences (Switzerland) (Vol. 11,
Issue 16). MDPI AG. https://doi.org/10.3390/app
11167366
Tranfield, D., Denyer, D., & Smart, P. (2003). Towards a
Methodology for Developing Evidence-Informed
Management Knowledge by Means of Systematic
Review. In British Journal of Management (Vol. 14,
Issue 3, pp. 207–222). https://doi.org/10.1111/1467-
8551.00375
Viles, E., Kalemkerian, F., Garza-Reyes, J. A., Antony, J.,
& Santos, J. (2022). Theorizing the Principles of
Sustainable Production in the context of Circular
Economy and Industry 4.0. Sustainable Production and
Consumption, 33, 1043–1058. https://doi.org/10.1016/
j.spc.2022.08.024
Xiao, Y., & Watson, M. (2019). Guidance on Conducting a
Systematic Literature Review. In Journal of Planning
Education and Research (Vol. 39, Issue 1, pp. 93–112).
SAGE Publications Inc. https://doi.org/10.1177/0739
456X17723971
Zhang, R. (2017). Sustainable scheduling of cloth
production processes by multi-objective genetic
algorithm with tabu-enhanced local search.
Sustainability (Switzerland), 9(10). https://doi.org/
10.3390/su9101754.
APPENDIX
The categorization of the revised indicators can be
seen in the following link: Appendix 1. The full list
of revised articles can be seen in the following link:
Appendix 2.
Integration of Sustainable Production Criteria into Production Scheduling: A Systematic Search and a Critical Review
69