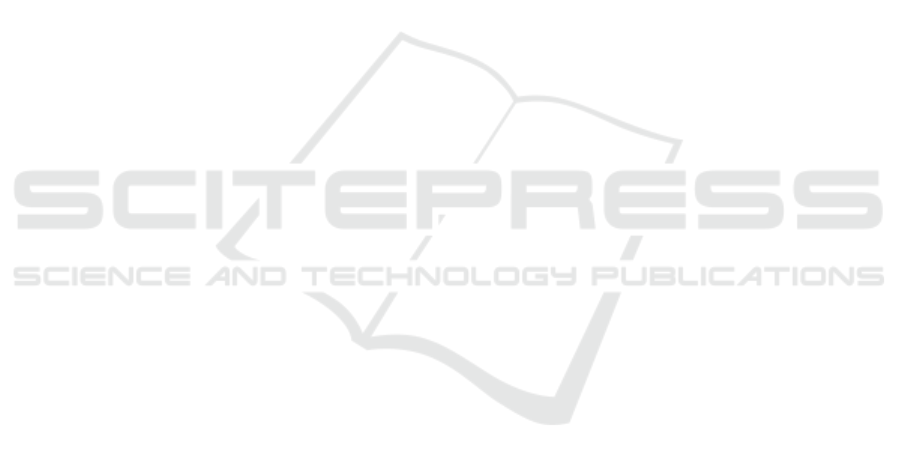
current control method and the linear mean current
charging were designed for the proposed converter,
improving the power factor. The power factor is
measured as 0.94 and %thd of the supply current is
around 7.23%. A hardware prototype model is
developed to verify the operation of the proposed
converter.
REFERENCES
Ramezani, A., Farhangi, S., Iman-Eini, H., Farhangi, B.,
Rahimi, R., & Moradi, G. R. (2019). Optimized LCC-
Series Compensated Resonant Network for Stationary
Wireless EV Chargers. IEEE Transactions on
Industrial Electronics, 66(4), 2756–2765.
Liu, J., Chan, K., Chung, C. Y., Hon, N., Liu, M., & Xu, W.
(2018). Single-Stage Wireless-Power-Transfer
Resonant Converter With Boost Bridgeless Power-
Factor-Correction Rectifier. IEEE Transactions on
Industrial Electronics, 65(3), 2145–2155.
Samanta, S., & Rathore, A. K. (2019). Small-Signal
Modeling and Closed-Loop Control of a Parallel–
Series/Series Resonant Converter for Wireless
Inductive Power Transfer. IEEE Transactions on
Industrial Electronics, 66(1), 172–182.
https://doi.org/10.1109/tie.2018.2823682
Samanta, S., & Rathore, A. K. (2018). A New Inductive
Power Transfer Topology Using Direct AC–AC
Converter With Active Source Current
Waveshaping. IEEE Transactions on Power
Electronics, 33(7), 5565–5577.
Phuoc Sang Huynh, & Williamson, S. S. (2019). Analysis
and Design of Soft-Switching Active-Clamping Half-
Bridge Boost Inverter for Inductive Wireless Charging
Applications. IEEE Transactions on Transportation
Electrification, 5(4), 1027–1039.
https://doi.org/10.1109/tte.2019.2930199
Moghaddami, M., & Sarwat, A. I. (2018). Single-Phase
Soft-Switched AC–AC Matrix Converter With Power
Controller for Bidirectional Inductive Power Transfer
Systems. IEEE Transactions on Industry
Applications, 54(4), 3760–3770.
Huynh, Phuoc Sang & Ronanki, Deepak & Vincent, Deepa
& Williamson, Sheldon. (2020). Overview and
Comparative Assessment of Single-Phase Power
Converter Topologies of Inductive Wireless Charging
Systems. Energies. 13. 2150. 10.3390/en13092150.
Yao, Yousu & Wang, Yijie & Liu, Xiaosheng & Lin,
Fanfan & Xu, Dian. (2017). A Novel Parameter Tuning
Method for Double-sided LCL Compensated WPT
System with Better Comprehensive Performance. IEEE
Transactions on Power Electronics. PP. 1-1.
10.1109/TPEL.2017.2778255.
Vu, V.-B., Phan, V.-T., Dahidah, M., & Pickert, V. (2019).
Multiple Output Inductive Charger for Electric
Vehicles. IEEE Transactions on Power
Electronics, 34(8), 7350–7368.
Charthad, Jayant & Chang, Ting & Liu, Zhaokai & Sawaby,
Ahmed & Weber, Marcus & Baker, Sam & Gore,
Felicity & Felt, Steve & Arbabian, Amin. (2018). A
mm-Sized Wireless Implantable Device for Electrical
Stimulation of Peripheral Nerves. IEEE Transactions
on Biomedical Circuits and Systems. PP. 1-14.
10.1109/TBCAS.2018.2799623.
ISPES 2023 - International Conference on Intelligent and Sustainable Power and Energy Systems
66