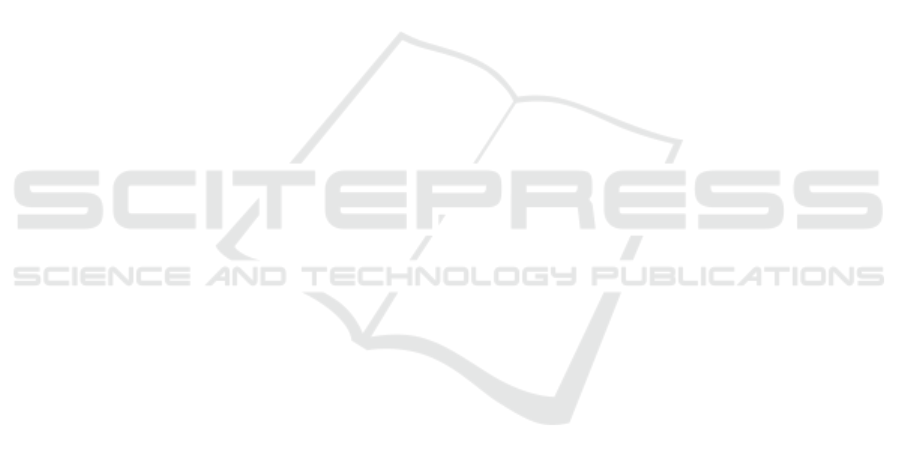
method of force decomposition achieves better re-
sults in experiment, up to an order of magnitude, than
common methods in literature. Future improvements
to the technique could include modeling interaction
torques as a force-couple with known moment arm
rather than a concentrated torque; this would match
the physical scenario more closely in certain config-
urations. Internal compliance might also be adjusted
so as to use each manipulator’s gripper point as the
respective center of rotation, while still sharing the
object center for external compliance and object-level
trajectory planning. Object mass and inertia proper-
ties, neglected here, could be incorporated into the
equations of motion. A Kalman filter could be ex-
plored for smoothing reactions to impulsive contact
forces and reducing oscillations. Taken together, this
work forms the basis for future dual-arm collabora-
tive object manipulation, including the exploration of
intelligent insertion strategies to improve speed and
repeatability.
REFERENCES
Ahlin, K. J., Sadegh, N., and Hu, A.-P. (2018). The se-
cant method: Global trajectory planning with variable
radius, solid obstacles. In Dynamic Systems and Con-
trol Conference, volume 51913, page V003T32A015.
American Society of Mechanical Engineers.
Calanca, A., Muradore, R., and Fiorini, P. (2016). A re-
view of algorithms for compliant control of stiff and
fixed-compliance robots. IEEE/ASME Transactions
on Mechatronics, 21(2):613–624.
Erhart, S. and Hirche, S. (2015). Internal force analysis and
load distribution for cooperative multi-robot manipu-
lation. IEEE Transactions on Robotics, 31(5):1238–
1243.
Gao, M., Zhou, H., Yang, Y., Dong, Z., and He, Z. (2022).
An intelligent master–slave collaborative robot system
for cafeteria service. Robotics and Autonomous Sys-
tems, 154:104121.
Hibbeler, R. C. (2011). Mechanics of materials. Prentice
Hall, Boston, 8th ed edition.
Hu, B., Yan, L., Han, L., and Yu, H. (2021). Coordinated
compliance control of dual-arm robot astronaut for
payload operation. International Journal of Advanced
Robotic Systems, 18(3):17298814211012850.
Khatib, O. (1985). Real-time obstacle avoidance for manip-
ulators and mobile robots. In Proceedings. 1985 IEEE
international conference on robotics and automation,
volume 2, pages 500–505. IEEE.
Khatib, O. (1986). The potential field approach and opera-
tional space formulation in robot control. pages 367–
377. Springer.
Kim, R., Balakirsky, S., Ahlin, K., Marcum, M., and
Mazumdar, A. (2021). Enhancing payload capacity
with dual-arm manipulation and adaptable mechani-
cal intelligence. Journal of Mechanisms and Robotics,
13(2).
Kousi, N., Michalos, G., Aivaliotis, S., and Makris, S.
(2018). An outlook on future assembly systems in-
troducing robotic mobile dual arm workers. Procedia
CIRP, 72:33–38. 51st CIRP Conference on Manufac-
turing Systems.
LaValle, S. M. (2006). Planning algorithms. Cambridge
university press.
Omar, R., Sabudin, E., CK, C. K. M., et al. (2016). Po-
tential field methods and their inherent approaches for
path planning. volume 11, pages 10801–10805. Asian
Research Publishing Network (ARPN).
Ren, X., Huang, L., and Zhao, M. (2021). Prioritized hier-
archical compliance control for dual-arm robot stable
clamping.
Roark, R. J., Young, W. C., Budynas, R. G., and Sadegh,
A. M. (2012). Roark’s formulas for stress and strain.
McGraw-Hill, New York, 8th ed edition. OCLC:
ocn769455976.
Seraji, H. (1994). Adaptive admittance control: an approach
to explicit force control in compliant motion. In Pro-
ceedings of the 1994 IEEE International Conference
on Robotics and Automation, pages 2705–2712 vol.4.
Song, X., Huang, H., Xu, W., and Li, B. (2022). A ro-
bust force controller of multi-robot cooperative ma-
nipulators for carrying task. In 2022 IEEE Interna-
tional Conference on Robotics and Biomimetics (RO-
BIO), pages 987–992, Jinghong, China. IEEE.
Song, X., Mao, H., Huang, H., Xu, W., and Li, B. (2021).
A Dynamic Adaptive Impedance Controller for Force
Tracking of Dual-arm Manipulators in Uncertain Con-
tact Environment. In 2021 IEEE International Con-
ference on Robotics and Biomimetics (ROBIO), pages
1674–1681, Sanya, China. IEEE.
Walker, I. D., Freeman, R. A., and Marcus, S. I. (1991).
Analysis of Motion and Internal Loading of Ob-
jects Grasped by Multiple Cooperating Manipula-
tors. The International Journal of Robotics Research,
10(4):396–409.
Wolf, S., Grioli, G., Eiberger, O., Friedl, W., Grebenstein,
M., Hoppner, H., Burdet, E., Caldwell, D. G., Car-
loni, R., Catalano, M. G., Lefeber, D., Stramigioli,
S., Tsagarakis, N., Van Damme, M., Van Ham, R.,
Vanderborght, B., Visser, L. C., Bicchi, A., and Albu-
Schaffer, A. (2016). Variable stiffness actuators: Re-
view on design and components. IEEE/ASME Trans-
actions on Mechatronics, 21(5):2418–2430. Cited By
:266.
Xian, Z., Lertkultanon, P., and Pham, Q.-C. (2017). Closed-
chain manipulation of large objects by multi-arm
robotic systems. IEEE Robotics and Automation Let-
ters, 2(4):1832–1839.
Dual-Arm Compliance Control with Robust Force Decomposition
623