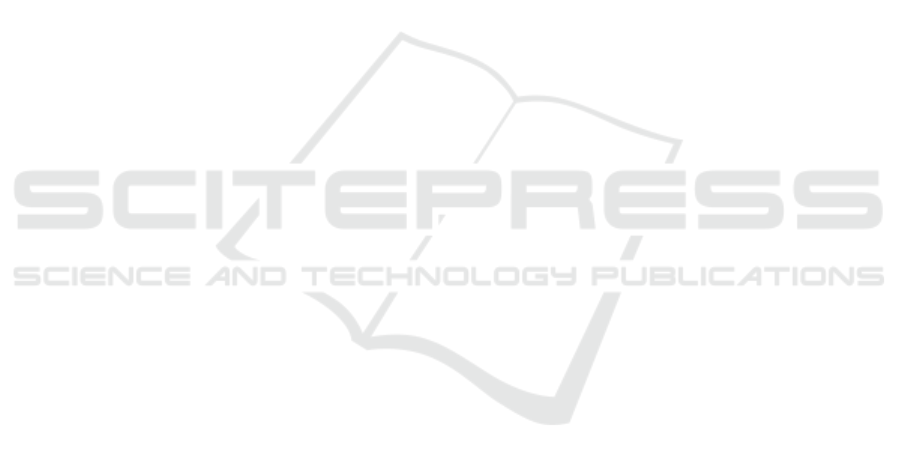
can be done, for example, with the help of a FEM
simulation. In our example, the distance was circa
10 cm. The test motion can be entered into our pro-
gram with the help of a small UI. We have carried
out our feasibility check and the resulting component
placement with this data. Our algorithm has selected
the position x = 50 cm, y = 156 cm, and z = 130 cm
for the robot starting point, corresponding to the po-
sition shown in Figure 4. This also denotes that the
robot can apply the required forces for our chosen use
case. Finally, we performed the actual component test
to ensure that the robot could apply the forces for the
given testing motion and the calculated starting pose,
which includes the pose E and joint positions Q. For
further validation of our force model, we performed
an experimental test at different positions with differ-
ent heights. The calculated values corresponded to
the experimentally determined values with a margin
of ± 300 N. However, these are negligible unless us-
ing the test bench at its ultimate limits of the forces or
torques. In order to be able to state how exactly the
values are deviating, more research is planned, which
will be described in more detail in the next section.
6 CONCLUSION
One challenge of robot-based component testing is
specimen placement since industrial robots cannot
achieve all forces or torques in every position. Our
CASP (Computer Aided Specimen Placement) ap-
proach for robot-based component testing solves this
challenge by calculating a position for the specimen
placement where the robots can test it. We first
extended our developed model for testing motions,
which includes load paths consisting of forces and
torques, the corresponding directions, and the start-
ing point to be determined by the testing motion. A
further advantage of this model is the representation
of superimposed loads that only a few standard test
rigs can muster. Moreover, we have developed a
description and storage format for robot forces and
torques depending on the robot’s orientation and po-
sition. With the help of the combination of these two
developments, we have presented an algorithm that
performs an automatic feasibility check for the re-
quired test motions and calculates the automatic spec-
imen placement. In our case study, we briefly ex-
plained our testing facility and evaluated the compo-
nent placement by choosing a classical use case for
material testing (standardized tensile tests). Our ap-
proach automatically calculated a placement for the
test specimen of this use case, and we successfully
performed the actual test afterward. In addition, we
conducted an experimental comparison of our force
model and identified slight deviations between our
model and the actual applicable forces. An initial as-
sumption leading to this deviation is the impact of the
mounted periphery, e.g., the weight of the end effec-
tor or the cable tow, as this is currently not included
in our calculation model. In further research, we will
conduct more experimental comparisons to determine
the deviations and thus better define the boundaries
more precisely. Finally, we are investigating how
the computer aided specimen placement can be sim-
ulated, e.g., for collision detection and extended for
multi-robot component tests. For this purpose, we are
already simulating the motion to the calculated start-
ing point of the test motion with the help of ROS2,
MoveIt, and NVIDIA Isaac Sim (see Figure 1 for our
Isaac Sim Model). We also want to combine the robot
motion simulation with a physical simulation of the
specimen with the framework ORBIT to simulate the
entire test sequence later on.
ACKNOWLEDGEMENTS
This work partly presents the results of the project
WiR Augsburg which was funded by the German Fed-
eral Ministry of Education and Research (BMBF) and
the Bavarian Government.
REFERENCES
(2019). Metallic materials, Tensile testing, Part 1: Method
of test at room temperature. Standard DIN EN 6892-
1:2019, DIN Deutsches Institut f
¨
ur Normung e. V.,
Berlin, DE.
Alemzadeh, K. and Raabe, D. (2007). Prototyping artifi-
cial jaws for the bristol dento-munch robo-simulator;
’a parallel robot to test dental components and mate-
rials’. In 2007 29th Annual International Conference
of the IEEE Engineering in Medicine and Biology So-
ciety, pages 1453–1456.
Coleman, D., Sucan, I., Chitta, S., and Correll, N. (2014).
Reducing the Barrier to Entry of Complex Robotic
Software: a MoveIt! Case Study.
Filipenko, M., Poeppel, A., Hoffmann, A., Reif, W., Mon-
den, A., and Sause, M. (2020). Virtual commission-
ing with mixed reality for next-generation robot-based
mechanical component testing. In ISR 2020; 52th In-
ternational Symposium on Robotics, pages 1–6.
Hanke, J., Eym
¨
uller, C., Reichmann, J., Trauth, A., Sause,
M., and Reif, W. Software-defined testing facility
for component testing with industrial robots. ETFA,
September 06-09, 2022, Stuttgart, to be published.
Harada, K., Tsuji, T., Nagata, K., Yamanobe, N., and Onda,
H. (2014). Validating an object placement planner
CASP: Computer Aided Specimen Placement for Robot-Based Component Testing
381