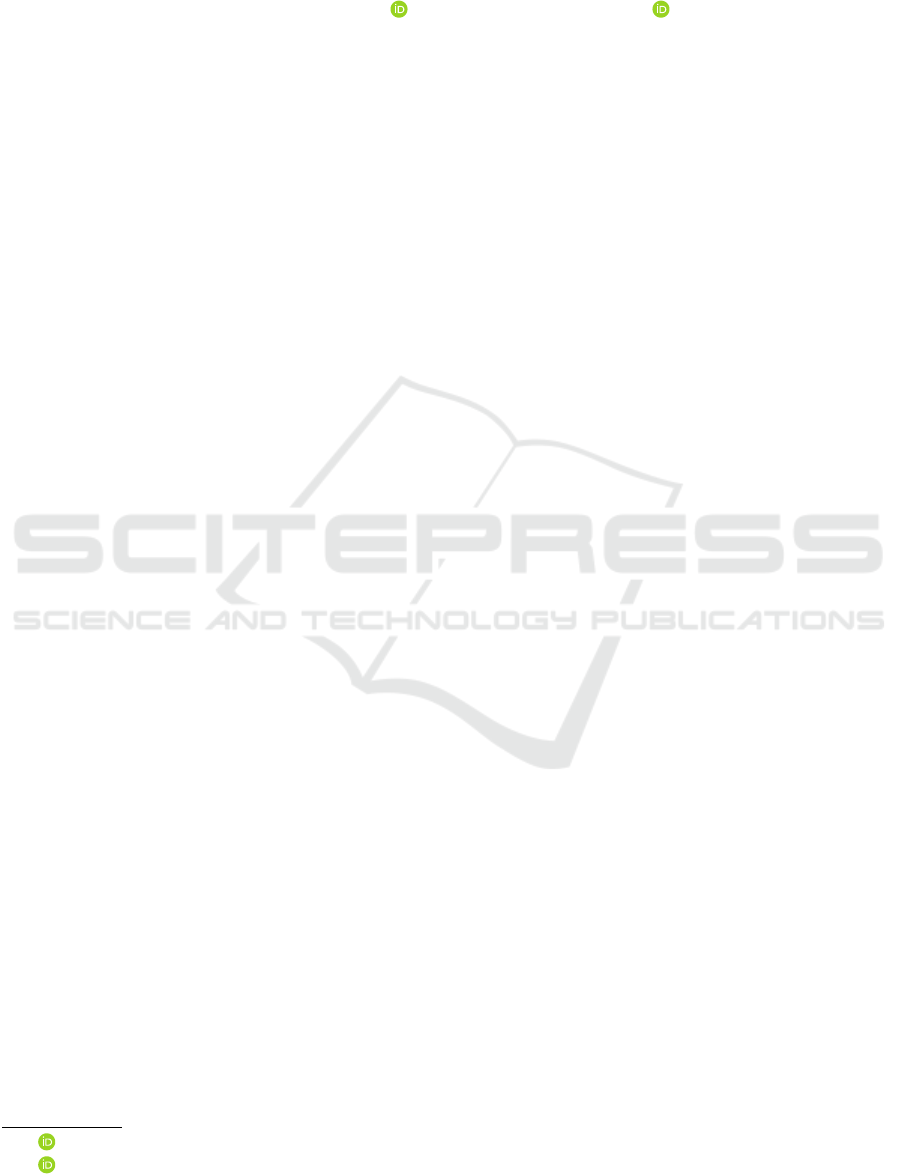
Implicit Multilinear Modeling of Air Conditioning Systems
Torben Warnecke
1 a
and Gerwald Lichtenberg
2 b
1
Deutsches Elektronen-Synchrotron DESY, Notkestr. 85, 22607 Hamburg, Germany
2
Faculty of Life Sciences, Hamburg University of Applied Sciences, Ulmenliet 20, 21033 Hamburg, Germany
Keywords:
Multilinear Algebra, Differential-Algebraic Models, State-Space Models, Tensor Decomposition, HVAC,
Air-Conditioning, Building Automation, Building Simulation.
Abstract:
The publication explores the applicability of implicit multilinear model approaches in air conditioning systems.
Implicit multilinear time-invariant models offer a structure that allows for the representation of most of the
fundamental physical equations of HVAC systems. Since the implicit multilinear time-invariant model class
is closed, it enables a component-based modeling approach to represent various types of HVAC systems with
different combinations of components. Multilinear time-invariant models are usually represented by tensors.
With HVAC-Systems having a large number of inputs and states, the models can be efficiently represented
in a decomposed manner, resulting in a matrix representation. As an example, the model of a precision
climatization hutch with a PI controller is derived and simulated.
1 INTRODUCTION
In this paper, an example model is provided to demon-
strate the applicability of implicit multilinear time-
invariant (iMTI) models for HVAC-Systems (Heat-
ing, Ventilation and Air Conditioning) working with
humid air. The energy equations of HVAC-Systems
mostly consist of linear combination of mass flows
and thermodynamic states, such as temperatures or
enthalpies (specific energy content of mass), e.g. in
the first law of thermodynamics applied to fluids.
Such equations typically exhibit a multilinear time-
invariant structure, as shown in (Lichtenberg et al.,
2022), (Pangalos et al., 2013) and (Pangalos et al.,
2014). A multilinear time-invariant structure can be
derived from the fundamental physical equations of
thermodynamic states and the energy conservation
principles of humid air systems. For the example of a
precision climatization hutch, typical thermodynamic
approaches, e.g. shown in (Yao and Yu, 2018), were
used. Usually, these systems are approximated using
linearized state-space models. However, this paper
proposes a modeling method with fewer approxima-
tions, allowing for direct utilization of most of the
fundamental physical equations.
a
https://orcid.org/0009-0004-3037-8634
b
https://orcid.org/0000-0001-6032-0733
2 MULTILINEAR MODELS
Recently, the implicit multilinear model framework
has been introduced. Firstly in an explicit form in
(Pangalos et al., 2013) and an implicit form in (Licht-
enberg et al., 2022). The multilinear model method
serves as a compromise between slow but accurate
nonlinear and fast but linear models. Furthermore,
linear and binary models can be fully represented us-
ing the multilinear structure. The multilinear func-
tions enable the utilization of tensor algorithms and
multilinear algebra, since the model structure and
parameter-space can be represented by tensors. This
facilitates the usage of tensor decomposition methods
and enhances the efficient use of multilinear models
in simulations or other applications, like control and
automation.
2.1 Implicit Multilinear State-Space
Modeling
Expanding the explicit multilinear time-invariant
(eMTI) model format into the implicit multilinear
time-invariant (iMTI) format allows the multiplica-
tion of state derivatives
˙
x ∈ R
n
with states x ∈ R
n
,
inputs u ∈ R
m
and/or outputs y ∈ R
r
. This enables
the representation of broken rational functions within
implicit multilinear models. More importantly, the
iMTI model class is a closed model class, mean-
440
Warnecke, T. and Lichtenberg, G.
Implicit Multilinear Modeling of Air Conditioning Systems.
DOI: 10.5220/0012138200003546
In Proceedings of the 13th International Conference on Simulation and Modeling Methodologies, Technologies and Applications (SIMULTECH 2023), pages 440-447
ISBN: 978-989-758-668-2; ISSN: 2184-2841
Copyright
c
2023 by SCITEPRESS – Science and Technology Publications, Lda. Under CC license (CC BY-NC-ND 4.0)