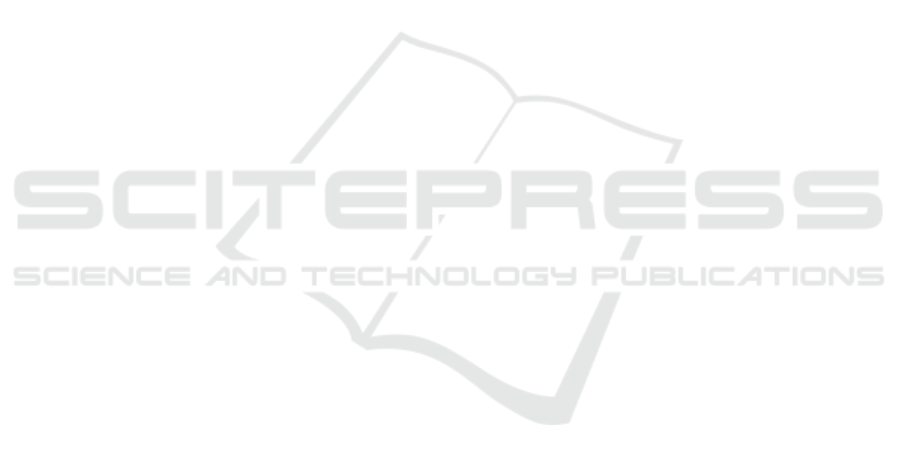
accordingly.
When message interval is kept within the capabil-
ity bracket of the FIWARE platform it will cause only
a marginal overhead. With 10ms messaging interval
26.5ms latency was measured. If loaded beyond the
processing capacity, overhead very quickly increases
to a significant amount. Scaling up cloud computing
capability is necessary if the capacity of the FIWARE
system becomes a bottleneck.
As network latency is dominating factor in normal
use case some strategies to mitigate it is needed. Cop-
ing with network latency in this use case can be done
in one of four ways:
• Increase safety zone to take into account the la-
tency
• Decrease working speed of robots
• Move computation into Edge to mitigate network
latency
• Use low latency networks such as 5G
In a practical use case scenario safety perimeter and
working speed may be the easiest ways of coping with
latency, but adding the edge capabilities or faster net-
work would have less impact on actual work perfor-
mance.
7 CONCLUSIONS
Understanding the distribution of latency in IoT data
collection systems helps to pinpoint bottlenecks in the
data collection system. Suitability to different use
cases and their real-time requirements requires an un-
derstanding of system behavior.
The performance of the FIWARE system is de-
pendent on underlying computing resources and the
messaging load of the system. When going over the
threshold, the latency increases from 17ms to over
4800ms. Determining the system load in terms of
context updates per second is important to keep the
latency within an acceptable limit. The underlying
computing platform processing capability needs to be
sized according.
Based on the findings here capability of the IoT
platform can be determined with a test involving data
subscriber and publisher. In the FIWARE system ma-
jority of the latency is coming from the IoT agent and
Orion. Optimizing cloud service performance param-
eters for those two components provide the best re-
sults for overall performance gains. Additional la-
tency is introduced with actual analysis as well as
communicating messages back to the robot.
Based on the findings here it can be argued that it
is feasible to use FIWARE in the simulated use cases
where the number of simultaneously operating robots
is limited. The latency caused by the IoT platform is
reasonable. If the platform is serving several farms or
fields simultaneously computing resources may need
to be allocated consecutively to keep QoS acceptable.
ACKNOWLEDGMENT
This research was conducted by VTT and LUKE as
part of the European Union’s Horizon 2020 research
and innovation programme under grant agreement No
101017111.
REFERENCES
Ahuja, A., Jain, V., Saini, D., and Al-Turjman, F. (2021).
Measuring clock reliability in cloud virtual machines,
real-time intelligence for heterogeneous networks:
Applications, challenges, and scenarios in iot. In Het-
Nets, 2021, 87-98.
Araujo, V., Mitra, K., Saguna, S., and
˚
Ahlund, C. (2019).
Performance evaluation of fiware: A cloud-based iot
platform for smart cities. In Journal of Parallel and
Distributed Computing 132 (2019) 250–261.
Farooq, M. S., Riaz, S., Abid, A., Abid, K., and Naeem,
M. A. (2019). A survey on the role of iot in agri-
culture for the implementation of smart farming. In
IEEE Access, vol. 7, pp. 156237-156271, 2019, doi:
10.1109/ACCESS.2019.2949703.
Friha, O., Ferrag, M. A., Shu, L., Maglaras, L.,
and Wang, X. (2021). Internet of things for
the future of smart agriculture: A comprehen-
sive survey of emerging technologies. ieee/caa
journal of automatica sinica, 8(4), 718–752.
https://doi.org/10.1109/jas.2021.1003925.
Garc
´
ıa, L., Parra, L., Jimenez, J., Lloret, J., and Lorenz,
P. (2020). Iot-based smart irrigation systems: An
overview on the recent trends on sensors and iot sys-
tems for irrigation in precision agriculture. In Sensors
2020, 20, 1042. https://doi.org/10.3390/s20041042.
Grieve, B. D., Duckett, T., Collison, M., Boyd, L., West, J.,
Yin, H., Arvin, F., and Pearson, S. (2019). The chal-
lenges posed by global broadacre crops in delivering
smart agri-robotic solutions: A fundamental rethink is
required, global food security. In Volume 23, Pages
116-124, ISSN 2211-9124.
Lee, J. and Hwang, K. (2021). Yolo with adap-
tive frame control for real-time object detection
applications. In Multimed Tools Appl (2021).
https://doi.org/10.1007/s11042-021-11480-0.
Levine, J. (2016). An algorithm for synchronizing
a clock when the data are received over a net-
work with an unstable delay. In IEEE Trans
Ultrason Ferroelectr Freq Control. 63(4):561-570.
doi:10.1109/TUFFC.2015.2495014.
Neagoe, T., Cristea, V., and L., B. (2006). Ntp versus ptp in
com puter networks clock synchronization. In IEEE
IoTBDS 2023 - 8th International Conference on Internet of Things, Big Data and Security
80