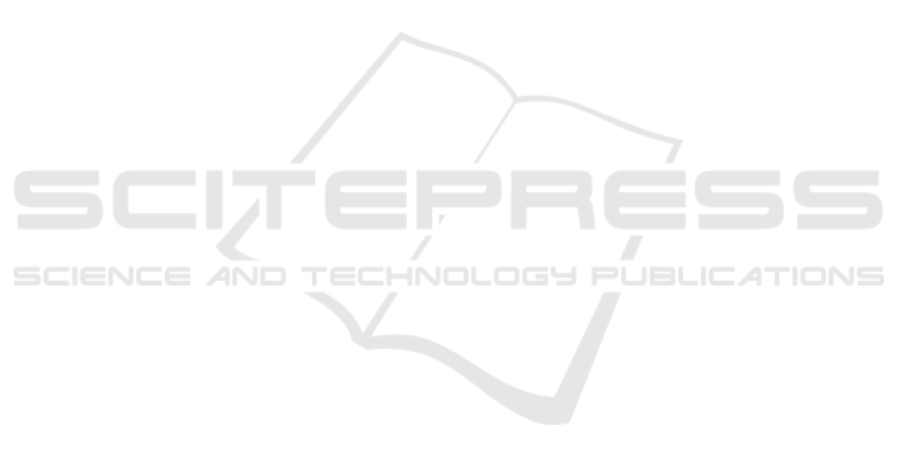
systems. European Journal of Operational Research,
222(3):484–494. Publisher: Elsevier.
Janse van Rensburg, L. J. v. (2019). Artificial intelli-
gence for warehouse picking optimization - an NP-
hard problem. Master’s thesis, Uppsala University.
Kallina, C. and Lynn, J. (1976). Application of the Cube-
per-Order Index Rule for Stock Location in a Distri-
bution Warehouse. Interfaces, 7(1):37–46.
Kofler, M., Beham, A., Wagner, S., and Affenzeller, M.
(2014). Affinity Based Slotting in Warehouses with
Dynamic Order Patterns. (Advanced Methods and
Applications in Computational Intelligence):123–143.
Koster, R. d., Le-Duc, T., and Roodbergen, K. J. (2007).
Design and control of warehouse order picking: A lit-
erature review. European Journal of Operational Re-
search, 182(2):481 – 501.
Kruk, S. (2018). Practical Python AI Projects: Mathemat-
ical Models of Optimization Problems with Google
OR-Tools. Apress.
K
¨
ubler, P., Glock, C., and Bauernhansl, T. (2020). A new
iterative method for solving the joint dynamic storage
location assignment, order batching and picker rout-
ing problem in manual picker-to-parts warehouses.
147:106645.
Larco, J. A., Koster, R. d., Roodbergen, K. J., and Dul, J.
(2017). Managing warehouse efficiency and worker
discomfort through enhanced storage assignment de-
cisions. International Journal of Production Re-
search, 55(21):6407–6422.
Lee, I. G., Chung, S. H., and Yoon, S. W. (2020). Two-stage
storage assignment to minimize travel time and con-
gestion for warehouse order picking operations. Com-
puters & Industrial Engineering, 139:106129.
Liu, C.-M. (1999). Clustering techniques for stock location
and order-picking in a distribution center. Computers
& Operations Research, 26(10):989–1002.
Mackay, D. J. C. (1998). Introduction to Monte Carlo Meth-
ods. In Learning in Graphical Models.
Mantel, R. et al. (2007). Order oriented slotting: A new as-
signment strategy for warehouses. European Journal
of Industrial Engineering, 1:301–316.
Ming-Huang Chiang, D., Lin, C.-P., and Chen, M.-C.
(2014). Data mining based storage assignment heuris-
tics for travel distance reduction. Expert Systems,
31(1):81–90. Publisher: Wiley Online Library.
Oxenstierna, J., Malec, J., and Krueger, V. (2022). Analysis
of Computational Efficiency in Iterative Order Batch-
ing Optimization. In Proceedings of the 11th Interna-
tional Conference on Operations Research and Enter-
prise Systems - ICORES,, pages 345–353. SciTePress.
Rajasekaran, S. and Reif, J. H. (1992). Nested annealing: a
provable improvement to simulated annealing. Theo-
retical Computer Science, 99(1):157–176.
Rathod, A. B., Gulhane, S. M., and Padalwar, S. R. (2016).
A comparative study on distance measuring approches
for permutation representations. In 2016 IEEE inter-
national conference on advances in electronics, com-
munication and computer technology (ICAECCT),
pages 251–255. IEEE.
Roodbergen, K. J. and Koster, R. (2001). Routing methods
for warehouses with multiple cross aisles. Interna-
tional Journal of Production Research, 39(9):1865–
1883.
Tak, H., Meng, X.-L., and Dyk, D. A. v. (2018). A Re-
pelling–Attracting Metropolis Algorithm for Multi-
modality. Journal of Computational and Graphical
Statistics, 27(3):479–490.
Trindade, M. A. M., Sousa, P., and Moreira, M. (2022).
Ramping up a heuristic procedure for storage loca-
tion assignment problem with precedence constraints.
Flexible Services and Manufacturing Journal, 34.
Valle, C., Beasley, J. E., and da Cunha, A. S. (2017). Opti-
mally solving the joint order batching and picker rout-
ing problem. European Journal of Operational Re-
search, 262(3):817–834.
Wales, D. J. and Doye, J. P. K. (1997). Global Optimiza-
tion by Basin-Hopping and the Lowest Energy Struc-
tures of Lennard-Jones Clusters Containing up to 110
Atoms. Journal of Physical Chemistry A, 101:5111–
5116.
Wu, J., Qin, T., Chen, J., Si, H., and Lin, K. (2014). Slot-
ting Optimization Algorithm of the Stereo Warehouse.
In Proceedings of the 2012 2nd International Confer-
ence on Computer and Information Application (IC-
CIA 2012), pages 128–132. Atlantis Press.
Wutthisirisart, P., Noble, J. S., and Chang, C. A. (2015). A
two-phased heuristic for relation-based item location.
Computers & Industrial Engineering, 82:94–102.
Xiang, X., Liu, C., and Miao, L. (2018). Storage as-
signment and order batching problem in Kiva mo-
bile fulfilment system. Engineering Optimization,
50(11):1941–1962.
Yu, M. and Koster, R. B. M. d. (2009). The impact of or-
der batching and picking area zoning on order pick-
ing system performance. European Journal of Opera-
tional Research, 198(2):480 – 490.
Yu, V. F., Winarno, Maulidin, A., Redi, A. A. N. P., Lin,
S.-W., and Yang, C.-L. (2021). Simulated Annealing
with Restart Strategy for the Path Cover Problem with
Time Windows. Mathematics, 9(14).
Zhang, R.-Q. et al. (2019). New model of the storage loca-
tion assignment problem considering demand corre-
lation pattern. Computers & Industrial Engineering,
129:210–219.
ˇ
Zulj, I., Glock, C. H., Grosse, E. H., and Schneider, M.
(2018). Picker routing and storage-assignment strate-
gies for precedence-constrained order picking. Com-
puters & Industrial Engineering, 123:338–347.
ICORES 2023 - 12th International Conference on Operations Research and Enterprise Systems
104