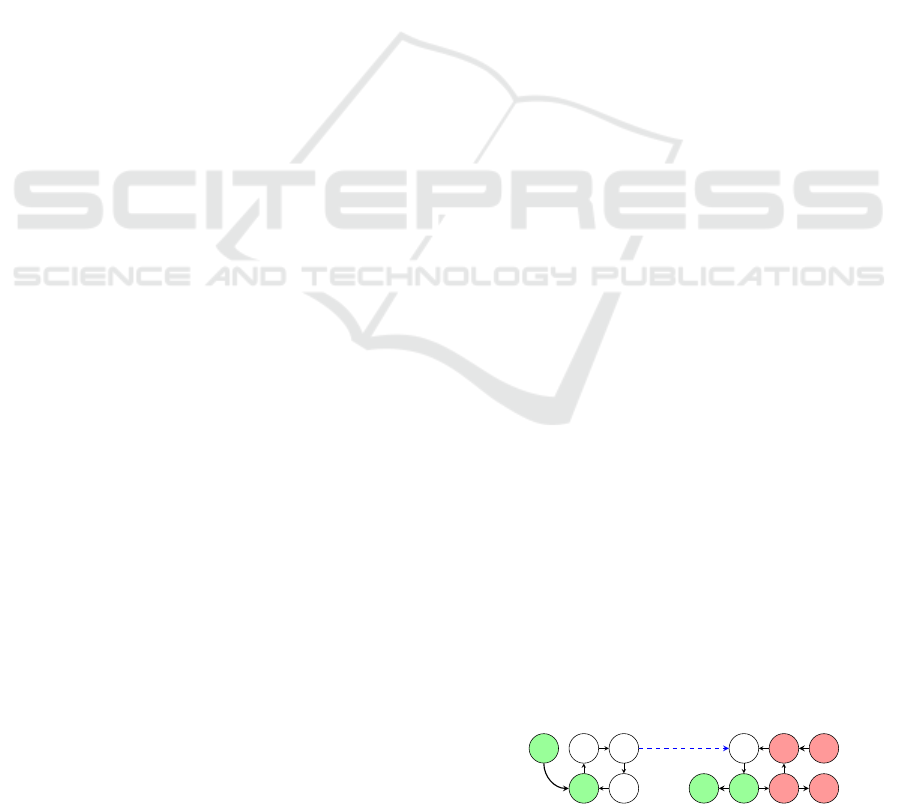
S ⊂ E, which represents controllable gates in the sys-
tem transporting workpieces between carousels.
The workload is represented by a set of k work-
pieces M = {1, . . . , k}. Each workpiece m ∈ M is
associated with the release time r
(m)
∈ N
0
, denoting
its earliest possible time when the workpiece can be
loaded on the belt. Before the workpiece is loaded
on the belt, it stays at its inbound location I
(m)
∈ V .
Furthermore, the workpiece m ∈ M specifies the se-
quence of vertices (stations) π
(m)
=
π
(m)
1
, . . . , π
(m)
n
m
,
π
(m)
i
∈ V which have to be visited by m. After posi-
tion π
(m)
n
m
is reached by m, it is moved to its outbound
location O
(m)
∈ V and is effectively removed from the
system since it no longer occupies any belt position.
The solution to the problem is represented by
a schedule y
(m)
t
∈ V , which for each workpiece m
specifies the position it occupies at time t. Further-
more, it defines for each gate (u, v) ∈ S a binary value
z
t
(u, v) ∈ {0, 1} which is set to 1 if and only if the gate
(u, v) is activated at time t.
We say that the schedule is feasible if workpieces
satisfy their release times and for any m
a
, m
b
∈ M,
m
a
6= m
b
: ∀t : y
(m
a
)
t
6= y
(m
b
)
t
, i.e., at any moment, no
two workpieces occupy the same position. Further-
more, a workpiece m which at time t occupies y
(m)
t
subsequently occupies its neighboring position of y
(m)
t
at time t +1. The neighboring position of vertex v ∈ V
at time t is either u ∈ V such that (v, u) ∈ E (i.e., u is
the successor position of the v on the same carousel)
or w ∈ V if (v, w) ∈ S and z
t
(v, w) = 1, i.e., the work-
piece is transported to a different carousel with (v, w)
gate. The objective is to minimize the total flow time,
i.e., the sum of differences between the time reaching
the outbound location and the release time over every
workpiece.
3.3 Example
To demonstrate the defined quantities and constraints
of the problem, please see an example in Figure 3.
There, we depict three different solutions for the prob-
lem with two workpieces A and B. We assume that the
release times of both workpieces are equal to zero,
i.e., r
(A)
= r
(B)
= 0 and the sequences of stations to
visit are π
(A)
= (0, 15) and π
(B)
= (9, 15).
In Figure 3a, both workpieces are loaded to the
carousel at time t = 0, thus y
(A)
0
= 0 and y
(B)
0
= 9. At
the time t = 1, workpieces are moved to their neigh-
boring location. In this solution, the gate (9, 18) was
activated at time t = 0, i.e., z
0
(9, 18) = 1. In subse-
quent time instant, both workpieces are again moved
to their neighboring positions; therefore, y
(A)
1
= 1 and
y
(B)
1
= 18. After one additional move, the gate (2,12)
is activated at time 2 (i.e., z
2
(2, 12) = 1), thus, we
have y
(A)
3
= 12. However, this violates the feasibility
condition since y
(B)
3
= 12 as well, and the solution (a)
is infeasible.
A different solution is shown in Figure 3b. In this
case, the gate (9, 18) is not activated at time t = 0.
Therefore, the workpiece B is forced to perform one
additional rotation with its initial carousel before it is
(eventually) transferred. Thus, the conflict at position
12 is avoided at the expense of increased flow time of
B by 6 time units.
Finally, the third solution is displayed in Fig-
ure 3c. Here, the workpiece B is unloaded onto the
carousel immediately at time t = 0, whereas work-
piece A waits at its inbound location until time t = 1.
Since A is released 1 time unit later than in solution
(a), it also avoids the conflict at position 12, but the
total flow time is smaller than in solution (b).
The above examples show some important con-
siderations to be made when solving the problem—
both the timings of the gates as well the times when
the workpieces are loaded to the carousels affect the
quality of the solution. Thus, they need to be consid-
ered simultaneously, which represents an interesting
optimization problem.
4 TIME-EXPANDED INTEGER
MULTI-COMMODITY FLOW
First, we explain the concept of a time-expanded net-
work for the conveyor belt scheduling problem. Then,
we give a mixed-integer linear programming (MILP)
formulation of the problem, which resembles an ordi-
nary integer multi-commodity network flow problem
with one additional constraint.
4.1 Time-Expanded Network
The main difficulty of using network flow formalism
for problems with time-related constraints (e.g., re-
lease times and vertex ordering) is that a flow in the
network does not capture the notion of time. One of
the possible options how to accommodate these con-
straints is the so-called time expansion of the network,
which is used, e.g., for dynamic network flow prob-
lems (Ahuja et al., 1988).
0
1
2
3
5
4
6
7
A B
A B
Figure 4: An example of a system G.
ICORES 2023 - 12th International Conference on Operations Research and Enterprise Systems
206