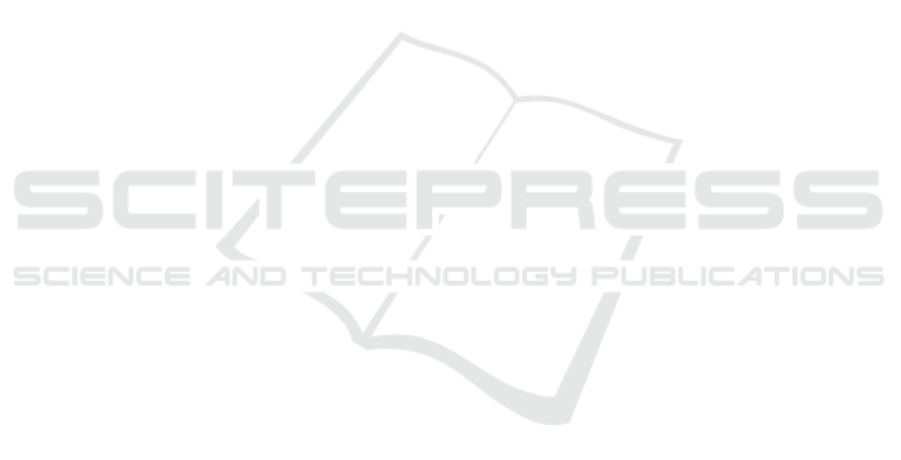
A continuum method for modeling surface tension.
Journal of Computational Physics, 100(2):335–354.
Gingold, R. A. and Monaghan, J. J. (1997). Smoothed par-
ticle hydrodynamics: Theory and application to non-
spherical stars. Monthly Notices of the Royal Astro-
nomical Society, 181(3):375–389.
Hattori, T. and Kohizuka, S. (2019). Numerical simulation
of droplet behavior on an inclined plate using the mov-
ing particle semi-implicit method. Mechanical Engi-
neering Journal, 6(5):19:00204–00220.
Kondo, M. and Matsumoto, J. (2021). Surface tension and
wettability calculation using density gradient poten-
tial in a physically consistent particle method. Com-
puter Methods in Applied Mechanics and Engineer-
ing, 385(114072):1–24.
Koshizuka, S. and Oka, Y. (1996). Moving-particle semi-
implicit method for fragmentation of incompressible
fluid. Nuclear Science and Engineering, 123(3):421–
434.
Morris, J. P. (2000). Simulating surface tension with
smoothed particle hydrodynamics. International
Journal for Numerical Methods in Fluids, 33:333–
353.
Mukai, N., Natsume, T., Oishi, M., and Ohsima, M. (2022).
Liquid injection simulation with wettability represen-
tation method considering adhesional and spreading
works. In 7th International Conference on Compu-
tational and Mathematical Biomedical Engineering
(CMBE), pages 617–620.
Natsume, T., Oishi, M., Ohsima, M., and Mukai, N.
(2019a). Particle based droplet simulation in liquid-
liquid two-phase flow. In MODSIM (23rd Interna-
tional Congress on Modelling and Simulation), pages
822–827.
Natsume, T., Oishi, M., Ohsima, M., and Mukai, N.
(2019b). Visualization of liquid drop behavior based
on particle method and its quantitative evaluation (in
Japanese). The Journal of the Society for Art and Sci-
ence, 18(3):106–113.
Natsume, T., Oishi, M., Ohsima, M., and Mukai, N.
(2021a). Droplet formulation method for viscous fluid
injection considering the effect of liquid-liquid two-
phase flow. ITE (The Institute of Image Informa-
tion and Television Engineers) Transactions on Media
Technology and Applications, 9(1):33–41.
Natsume, T., Oishi, M., Ohsima, M., and Mukai, N.
(2021b). Wettability method based on surface free
energy between solid and liquid. In IWAIT (Inter-
national Workshop on Advanced Image Technology)
2021, SPIE (The International Society for Optics and
Photonics), volume 11766, pages 1176613:1–6.
Natsume, T., Oishi, M., Ohsima, M., and Mukai, N.
(2022). A study on particle-based wettability method
considering adhesional and spreading wettings (in
Japanese). The Journal of the Society for Art and Sci-
ence, 21(2):97–110.
Nomura, K., Koshizuka, S., Oka, Y., and Obata, H. (2001).
Numerical analysis of droplet breakup behavior using
particle method. Journal of Nuclear Science and Tech-
nology, 38(12):1057–1064.
Ruan, L., Liu, J., Zhu, B., Sueda, S., Wang, B., and Chen, B.
(2021). Solid-fluid interaction with surface-tension-
dominant contact. ACM Transactions on Graphics,
40(4):Article 120.
Shirakawa, N., Rorie, H., Yamamoto, Y., and Tsunayama,
S. (2001). Analysis of the void distribution in a
circular tube with the two-fluid particle interaction
method. Journal of Nuclear Science and Technology,
38(6):392–402.
Tartakovsky, A. and Meakin, P. (2005). Modeling of surface
tension and contact angles with smoothed particle hy-
drodynamics. Physical Review, E 72:26301:1–9.
Wang, H., Mucha, P. J., and Turk, G. (2005). Water drops on
surfaces. ACM SIGGRAPH Papers, pages 921–929.
Xing, J., Ruan, L., Wang, B., Zhu, B., and Chen, B. (2022).
Position-based surface tension flow. ACM Transac-
tions on Graphics, 41(6):Article 244.
Yang, T., Lin, M. C., Martin, R. R., Chang, J., and Hu,
S. (2016). Versatile interactions at interfaces for SPH-
based simulations. In Eurographics/ACM SIGGRAPH
Symposium on Computer Animation, pages 57–66.
Zhang, Y., Wang, H., Wang, S., Tong, Y., and Zhou, K.
(2012). A deformable surface model for real-time wa-
ter drop animation. IEEE Transactions on Visualiza-
tion and Computer Graphics, 18(8):1281–1289.
GRAPP 2023 - 18th International Conference on Computer Graphics Theory and Applications
236