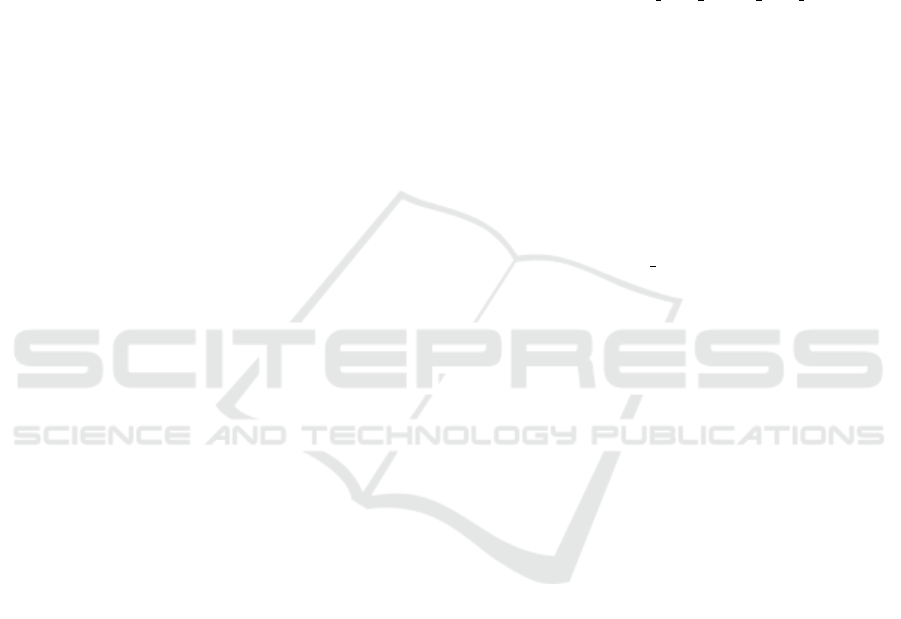
process by disintegrating flocculated ore formations,
it is advisable to exert a spatial effect on the iron ore
slurry including a combination of high-energy ultra-
sound and the pulsed magnetic field of descending in-
tensity.
The modelling results enable concluding that to
improve quality of ore particles cleaning before flota-
tion, it is advisable to apply a spatial effect to the
iron ore slurry. This includes a combination of high-
energy ultrasound of 20 kHz in the cavitation mode
modulated by high-frequency pulses within 1 MHz-
5 MHz and the pulsed magnetic field of descending
intensity. The next stage involves calculation of char-
acteristics of these effects and determination of the
device parameters to disintegrate flocculated ore for-
mations in the slurry flow on the basis of the ultra-
sonic phased array.
4 CONCLUSIONS
To increase efficiency of magnetite concentrates flota-
tion by disintegrating flocculated ore formations and
cleaning the particle surface, it is advisable to use
nonlinear effects of the high-energy ultrasonic field to
form and maintain cavitation processes and acoustic
flows in the iron ore slurry.
Investigation into cavitation patterns results in de-
pendences obtained to determine optimal frequency
of high-energy ultrasound aimed to maintain cavita-
tion processes in the iron ore slurry depending on pa-
rameters of its components.
Based on the modelling results, it is established
that in order to improve quality of ore particles clean-
ing before flotation, a spatial effect should be ex-
erted on the iron ore slurry, which includes a com-
bination of 20kHz high-energy ultrasound in the cav-
itation mode modulated by high-frequency pulses of
1 MHz-5 MHz and the pulsed magnetic field of de-
scending intensity.
REFERENCES
Ambedkar, B. (2012). Ultrasonic Coal-Wash for De-
Ashing and De-Sulfurization: Experimental Investi-
gation and Mechanistic Modeling. Springer Theses.
Springer Berlin, Heidelberg. https://doi.org/10.1007/
978-3-642-25017-0.
Ambedkar, B., Nagarajan, R., and Jayanti, S. (2011).
Investigation of High-Frequency, High-Intensity Ul-
trasonics for Size Reduction and Washing of
Coal in Aqueous Medium. Ind. Eng. Chem.
Res, 50(23):13210–13219. https://doi.org/10.1021/
ie200222w.
Carvell, K. J. and Bigelow, T. A. (2011). Dependence of op-
timal seed bubble size on pressure amplitude at ther-
apeutic pressure levels. Ultrasonics, 51(2):115–122.
https://doi.org/10.1016/j.ultras.2010.06.005.
Chikazumi, S. (2009). Physics of Ferromagnetism, vol-
ume 94 of International Series of Monographs on
Physics. Oxford University Press, Oxford, 2 edition.
Golik, V., Komashchenko, V., Morkun, V., and
Zaalishvili, V. (2015). Enhancement of
lost ore production efficiency by usage of
canopies. Metallurgical and Mining Indus-
try, 7(4):325–329. https://www.metaljournal.
com.ua/assets/MMI 2014 6/MMI 2015 4/
047-GolikKomashchenkoMorkunZaalishvili.pdf.
Gubin, G. V., Tkach, V. V., and Ravinskaya, V. O. (2017).
Application of ultrasound for cleaning the surface of
altered mineral particles before flotation [Primene-
nie ul’trazvuka dlja ochistki poverhnosti izmenennyh
mineral’nyh chastic pered flotaciej]. The quality of
mineral raw materials, 1:341–349.
Harrison, C. D., Raleigh, Jr., C. E., and Vujnovic, B. J.
(2002). The use of ultrasound for cleaning coal.
In Proceedings of the 19th Annual International
Coal Preparation Exhibition and Conference, vol-
ume 1, page 61–67. http://web.archive.org/web/
20190713150249if /http://www.bixbydental.com:
80/about/news/coalultrasound.pdf.
Hoff, L. (2001). Acoustic Characterization of Con-
trast Agents for Medical Ultrasound Imaging.
Springer Dordrecht. https://doi.org/10.1007/
978-94-017-0613-1.
Hoff, L., Sontum, P. C., and Hovem, J. M. (2000). Oscilla-
tions of polymeric microbubbles: Effect of the encap-
sulating shell. The Journal of the Acoustical Society
of America, 107:2272–2280. https://doi.org/10.1121/
1.428557.
Hu, Z. (2013). Comparison of Gilmore-Akulichev equa-
tion and Rayleigh-Plesset equation on the rapeu-
tic ultrasound bubble cavitation. Master’s the-
sis, Iowa State University. https://doi.org/10.31274/
etd-180810-3261.
Karmazin, V. V. and Karmazin, V. I. (2005). Magnetic,
electrical and special methods of mineral processing.
Publishing house MGTU.
Kozubkov
´
a, M., Rautov
´
a, J., and Bojko, M. (2012). Math-
ematical Model of Cavitation and Modelling of Fluid
Flow in Cone. Procedia Engineering, 39:9–18. XI-
IIth International Scientific and Engineering Confer-
ence ”Hermetic Sealing, Vibration Reliability and
Ecological Safety of Pump and Compressor Machin-
ery” - ”HERVICON-2011”. https://doi.org/10.1016/j.
proeng.2012.07.002.
Mast, T. D., Souriau, L. P., Liu, D.-L. D., Tabei, M., Nach-
man, A. I., and Waag, R. C. (2001). A k-space
method for large-scale models of wave propagation
in tissue. IEEE Transactions on Ultrasonics, Fer-
roelectrics, and Frequency Control, 48(2):341–354.
https://doi.org/10.1109/58.911717.
Morkun, V. and Morkun, N. (2018). Estimation of the
Crushed Ore Particles Density in the Pulp Flow Based
on the Dynamic Effects of High-Energy Ultrasound.
CSSE@SW 2022 - 5th Workshop for Young Scientists in Computer Science Software Engineering
84