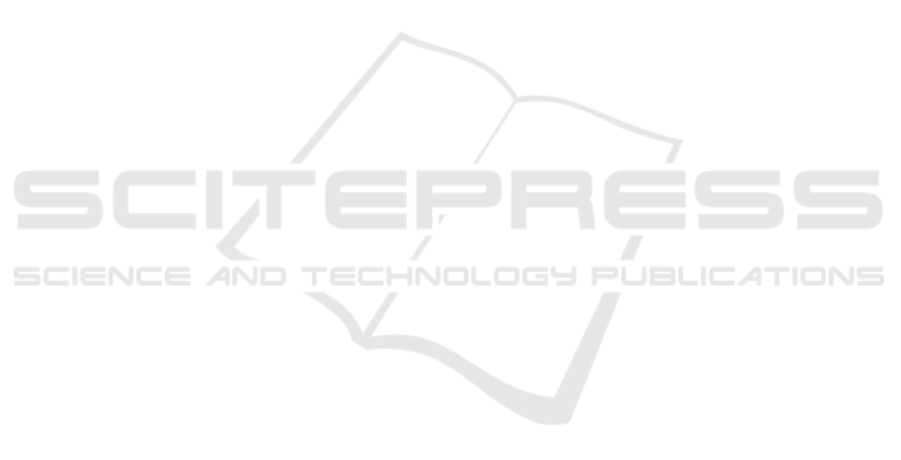
required for the assessment of safety,
reliability and security risks of autonomous
logistic systems. Special focus should be put
on considering the interactions between
subsystem and their potential outcomes and
implications. Knowledge on Cyber Physical
Systems (CPS) and Systems of Systems
(SoS) theories is important in handling the
system complexity.
▪ Application of systems-theoretic approaches
to support safety assessments of new
autonomous technologies. This will support
especially the identification of software-
based safety issues and issues in challenging
mixed traffic situations.
▪ Application of relevant standards from other
domains to account for the lack of domain-
specific standardization for port machinery.
The challenges presented in this paper cover only a
part of the larger number of socio-technical and
economic challenges that need to be solved to enable
increasing automation in small and mid-size
terminals. In addition to the mostly technical safety
and dependability aspects presented in this paper, the
entire business case and various operational and asset
management strategies need to be considered to form
a comprehensive understanding of the effects of
autonomy. Solving these challenges could lead to
major advances in container logistics, increasing
efficiency and safety within the terminal, but also
helping in optimization of the entire logistics chain.
ACKNOWLEDGEMENTS
The work presented in this paper is part of the
AUTOPORT project funded by Business Finland
under the Smart Mobility programme.
REFERENCES
AUTOPORT, 2020. Project website. Available:
https://autoport.fi/
Baudin, É, Blanquart, J., Guiochet, J. & Powell, D. 2007.
Independent Safety Systems for Autonomy: State of the
Art and Future Directions, LAAS-CNRS.
Brinkmann B., 2011. Operations Systems of Container
Terminals: A Compendious Overview. In: Böse J. (ed)
Handbook of Terminal Planning. Operations
Research/Computer Science Interfaces Series, vol 49.
Springer.
Čaušević, A. 2017. A risk and threat assessment approaches
overview in autonomous systems of systems. 2017
XXVI International Conference on Information,
Communication and Automation Technologies (ICAT),
Sarajevo, 2017, pp. 1-6.
Fiedler, R., et al., 2019. Autonomous vehicles' impact on
port infrastructure requirements. Fraunhofer Center for
Maritime Logistics and Services CML.
Hämäläinen, J., Yli-Paunu, P. & Peussa, P., 2018.
Automated container terminals and self-driving cars:
Industry outlook. Cargotec Kalmar white paper.
Available:
https://www.kalmarglobal.com/48eaed/globalassets/m
edia/215590/215590_White-paper-Autonomous-cars-
web.pdf
Heath, T., 2018. Autonomous Industrial Machines and the
Effect of Autonomy on Machine Safety. M.Sc Thesis.
Tampere University of Technology.
Heikkilä, E., & Välisalo, T. (2018). A methodological
framework to support the design of safe and secure
autonomous systems. In 9th International Conference
on Safety of Industrial Automated Systems, SIAS 2018:
Proceedings, pp. 110-115. inrs.
Hollnagel, E., 2012. FRAM: The functional resonance
analysis method: Modelling complex socio-technical
systems. Ashgate Publishing Ltd.
ISO 17757:2017. Earth-moving machinery and mining —
Autonomous and semiautonomous machine system
safety. 44 p.
Leveson, N. (2012). Engineering a safer world: Systems
thinking applied to safety. MIT Press.
Malm, T., Vuori, M., Rauhamäki, J., et al., 2011. Safety-
critical software in machinery applications. VTT
Technical Research Centre of Finland. VTT Research
Notes, No. 2601.
PEMA, 2016. Container Terminal Automation.
PEMA information paper. Available:
https://www.pema.org/wp-
content/uploads/downloads/2016/06/PEMA-IP12-
Container-Terminal-Automation.pdf
Pendleton, S., et al. 2017. Perception, Planning, Control,
and Coordination for Autonomous Vehicles. Machines.
5(1), 6.
Pentikäinen, H., Malm, T., & Heikkilä, E., 2019.
Cybersecurity in Autonomous Machine Systems
Development. VTT Technical Research Centre of
Finland. VTT Research Report, No. VTT-R-01087-19
Ramos, M.A., Thieme, C., Utne, I.B. & ; Mosleh, A.
Autonomous Systems Safety – State of the Art and
Challenges. In the Proceedings of the First International
Workshop on Autonomous Systems Safety (IWASS).
11-13 March, 2019, Trondheim Norway. Norwegian
University of Science and Technology (NTNU)
Trondheim, Norway ISBN: 978-82-691120-2-3
SAE-J3016, 2018. Taxonomy and Definitions for Terms
Related to Driving Automation systems for On-Road
Motor Vehicles. SAE International.
Tiusanen, R., Heikkilä, E., Malm, T., & Ronkainen, A.,
2019a. System safety engineering approach and
concepts for autonomous work-machine applications.
In 2019 World Congress: Resilience, Reliability and
Safety and Dependability of Autonomous Systems in Container Terminals: Challenges and Research Directions
533