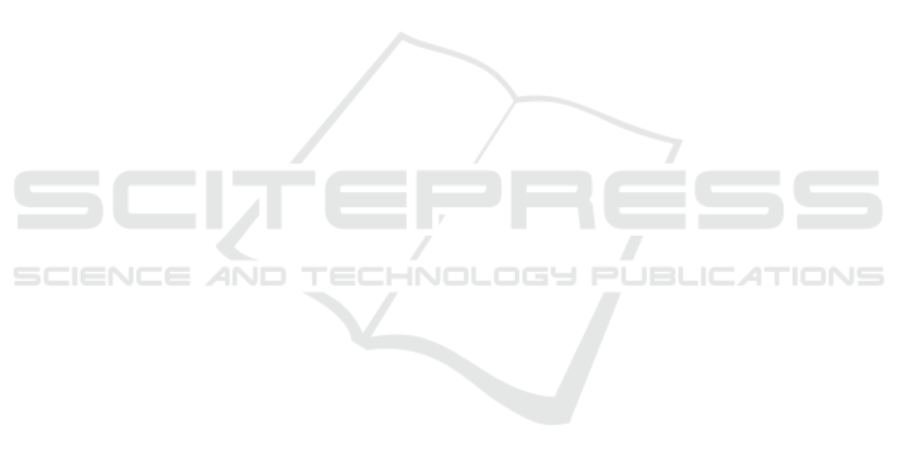
4 CONCLUSION
For coupled two tank level control, tuning PID param-
eter with Ziegler-Nichols method is fast without long
analitics formulation but respond system cannot be
adjust like we want. With RL method, system respond
is faster, smaller steadt state error, smaller water rip-
ples, smoother respond. PID parameters of Routh lo-
cus method could be adjusted like we want so it made
RL method powerful, more safety, more smooth, and
more stable.
REFERENCES
Bas¸c¸i, A. and Derdiyok, A. (2016). Implementation of an
adaptive fuzzy compensator for coupled tank liquid
level control system. Measurement, 91:12–18.
El-Samahy, A. and Shamseldin, M. (2018). rushless dc mo-
tor tracking control using self-tuning fuzzy pid control
and model reference adaptive control. Ain Shams En-
gineering Journal, 9(3):341–352.
Feng, H. (2018). Robotic excavator trajectory control us-
ing an improved ga based pid controller. Mechanical
Systems and Signal Processing, 105:153–168.
Gouta, H., Said, S., Barhoumi, N., and M’Sahli, F. (2015).
Observer-based backstepping controller for a state-
coupled two-tank system. IETE Journal of Research,
61(3):259–268.
Katal, N., Kumar, P., and Narayan, S. (2014). Optimal pid
controller for coupled-tank liquid-level control system
using bat algorithm. In 2014 International Conference
on Power, Control and Embedded Systems (ICPCES,
page 1–4.
Li, C., Yi, J., and Zhao, D. (2008). Interval type-2 fuzzy
neural network controller (IT2FNNC) and its appli-
cation to a coupled-tank liquid-level control system.
3rd International Conference on Innovative Comput-
ing Information and Control.
Lian, S., Marzuki, K., and Rubiyah, Y. (1998). Tuning of
a neuro-fuzzy controller by genetic algorithms with
an application to a coupled-tank liquid-level control
system. Engineering Applications of Artificial Intelli-
gence, 11(4):517–529.
Liang, G. (2018). Deaerator water level control based on
neuron intelligent control by fieldbus intelligent con-
trol network. In 2008 IEEE International Conference
on Networking, Sensing and Control, page 195–200.
Liang, L. (2011). The application of fuzzy pid controller in
coupled-tank liquid-level control system. In 2011 In-
ternational Conference on Electronics, Communica-
tions and Control (Icecc, page 2894–2897.
Pachauri, N., Rani, A., and Singh, V. (2017). Bioreactor
temperature control using modified fractional order
imc-pid for ethanol production. chemical engineering
research and design, 122:97–112.
Pan, H., Wong, H., Kapila, V., and Queiroz, M. (2005). Ex-
perimental validation of a nonlinear backstepping liq-
uid level controller for a state coupled two tank sys-
tem. Control Engineering Practice, 13(1):27–40.
Priyanka, E., Maheswari, C., and Thangavel, S. (2018). On-
line monitoring and control of flow rate in oil pipelines
transportation system by using plc based fuzzy-pid
controller. flow measurement and instrumentation.
Ramli, M. (2009). Improved coupled tank liquid lev-
els system based on swarm adaptive tuning of hy-
brid proportional-integral neural network controller.
American J. of Engineering and Applied Sciences,
2(4):669–675.
Roy, P., Kar, B., and Roy, B. (2017). Fractional order pi-pd
control of liquid level in coupled two tank system and
its experimental validation. Asian Journal of Control,
19(5):1699–1709.
Roy, P. and Roy, B. (2016). Fractional order pi control ap-
plied to level control in coupled two tank mimo sys-
tem with experimental validation. Control Engineer-
ing Practice, 48:119–135.
Tan, W. (2011). Water level control for a nuclear
steam generator. Nuclear Engineering and Design,
241(5):1873–1880.
Yadav, S., Verma, S., and Nagar, S. (2016). Optimized
pid controller for magnetic levitation system. IFAC-
PapersOnLine, 49(1):778–782.
Ziegler, J. and Nichols, N. (1942). Optimum settings for
automatic controllers. trans. ASME, 64(11).
Implementation PID in Coupled Two Tank Liquid Level Control using Ziegler-Nichols and Routh Locus Method
279