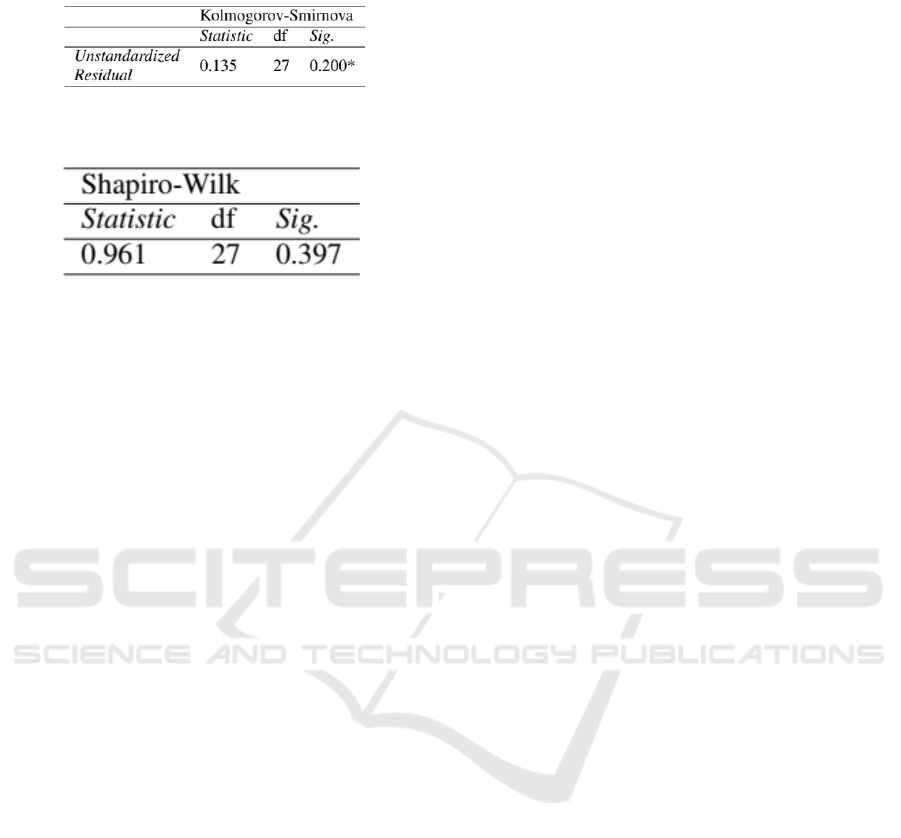
space
Figure 13: Residual normality test of calorific value.
Figure 14: Residual normality test of calorific value (exten-
sion).
Based on Figure 13 and Figure 14, it can be con-
cluded that the sawdust charcoal calorific value model
has met the eligibility requirements, and model vali-
dation, so that the resulting model is declared feasible
and valid and can be used to predict the sawdust char-
coal calorific value. The drying and pyrolysis treat-
ment has a positive effect on increasing the calorific
value. It is proved because the initial sawdust calorific
value of 3887 cal/g increased to 6231 cal/g after dry-
ing and pyrolysis. Therefore, there was an increase in
the calorific value of 2344 cal/g.
4 CONCLUSIONS
The optimum condition of the pyrolysis process
which can increase the calorific value of sawdust is
the drying temperature of 60 C°, the pyrolysis temper-
ature of 600 C°, holding time of 120 minutes, and par-
ticle size of 100 mesh. The linearity test results show
that the value of R; R Square; and Adjusted R Square
at the calorific value to have a strong correlation with
drying temperature, pyrolysis temperature, holding
time, and particle size. The result calorific value
model is
ˆ
Y(cal/g) = 4708.58–33.23X1 + 42.71X2 +
5.70X3 + 12.32X4. The validation test results of the
heat value model show that the residual normality dis-
tribution (P-value)> 0.05 does not form a certain pat-
tern on the assumption of homoscedasticity, no mul-
ticollinearity (TOL> 1; VIF <10) and the DW value
is within the specified range so the model is declared
valid. The model feasibility test results in a P-value
(0.000) < α (0.05) so that the calorific value model
is declared feasible and can be used to predict the
calorific value of sawdust charcoal to produce a qual-
ity briquette.
ACKNOWLEDGEMENTS
This research was funded by the Directorate Gen-
eral of Research and Development, Ministry of Re-
search, Technology and Higher Education for the pe-
riod 2017-2019.
REFERENCES
Al-Refaie, A., Al-Durgham, L., and Bata, N. (2010). Op-
timal parameter design by regression technique and
grey relational analysis. volume 3. Proceedings of the
World Congress on Engineering.
Azadi, M. M., Kolahan, F., and Golmezerji, R. (2011).
Multi objective optimization of turning process using
grey relational analysis and simulated annealing algo-
rithm. pages 2926–2932.
Basu, P. (2013). Biomass Gasification, Pyrolysis and Tor-
refaction: Practical Design and Theory. Elsevier Inc,
2nd edition.
Blasi, C. D. (2008). Modeling chemical and physical pro-
cesses of wood and biomass pyrolysis. 34:47–99.
Giacomo, G. D. and Taglieri, L. (2013). Modeling chemical
and physical processes of wood and biomass pyroly-
sis. 2(3):255–260.
Kalyani, P. and Anitha, A. (2013). Biomass carbon
& its prospects in electrochemical energy systems.
38:4034–4045.
Lela, B., Bari
ˇ
sic, M., and Nizˇetic, S. (2016). Card-
board/sawdust briquettes as biomass fuel: Physical–
mechanical and thermal characteristics. 47:236–245.
Mandala, W. W., Cahyono, M. S., Sukarjo, S., and War-
doyo, H. B. (2016). Influence of temperature to yield
and caloric value of plastic waste pyrolysis oil. 1.
Roy, R. K. (2010). A primer on the taguchi method: Society
of manufacturing engineers. 21.
Stolarski, J. M., Szczukowski, S., Tworkowski, J., Zaniak,
K., Gulczynski, P., and Mleczek, M. (2013). Compar-
ison of quality and production cost of briquettes made
from agricultural and forest origin biomass. 57:20–26.
Sundaram, P., Sudhakar, P., and Yogeshwaran, R. (2016).
Experimental studies and mathematical modeling of
drying wheat in fluidized bed dryer. 9(36):1–8.
Vargas-Moreno, J. M., Callej
´
on-Ferre, A. J., P
´
erez-
Alonsoa, J., and Vel
´
azquez-Mart
´
ı, B. (2012). A review
of the mathematical models for predicting the heating
value of biomass materials. 16:3065–3083.
Vishwakarma, M., Parashar, V., and Khare, V. (2012).
Regression analysis and optimization of material re-
moval rate on electric discharge machine foren-19 al-
loy steel using tungsten copper electrode. 2(6):785–
792.
Wilk, M., Magdziarz, A., Kalemba, I., and Gara, P. (2016).
Carbonisation of wood residue into charcoal during
low temperature process. pages 507–513.
Wisakha, P. (2015). Sustainability approach for energy pro-
duction using biomass at household and community
levels. a case study in thailand. 5(3):859–872.
Optimizing the Pyrolysis Process and Modelling the Calorific Value of Sawdust Charcoal as Composing Materials of Quality Briquettes
267