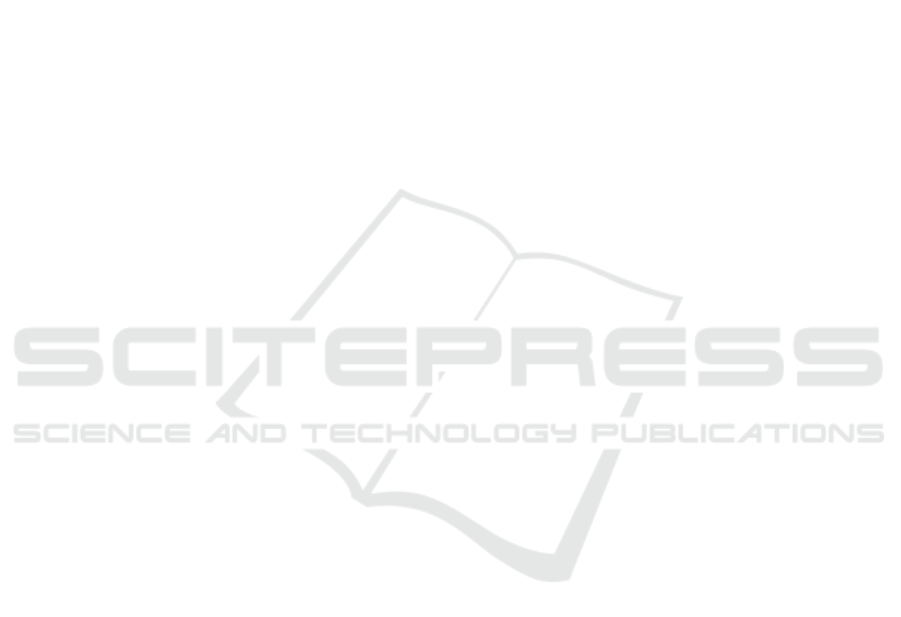
Experimental Study of Aluminum Composite Material by the Percentage
Variation of Volcanic Ash Reinforcement
Juriah Mulyanti
1
, Sukamto
1
, Novi Arviyanto
2
, Sazkia Noor Anggraini
3
and Muhammad Kunta
Biddinika
4
1
Department of Mechanical Engineering, Janabadra University, Yogyakarta 55231, Indonesia
2
PT. Kereta Api Indonesia, Yogyakarta, Indonesia
3
Indonesian Art Institute of Yogyakarta, Indonesia
4
Department of Civil Engineering, Janabadra University, Yogyakarta 55231, Indonesia
Keywords:
Aluminum composite, volcanic ash, percentage of reinforcement, stir casting, material testing.
Abstract:
This research is using the volcanic ash from the eruption of Mount Kelud as material composite reinforcement.
Information about large amounts of Silica (SiO2) on Mount Kelud volcanic ash and its abundant amounts in
Yogyakarta after the eruption, were the reason for choosing this material as reinforcement in the making of
aluminum metal composite. This composite is using the recycled aluminum material as their matrix. Stir
casting method used during the experiment. 1%, 3%, 5% of volcanic ash used with 300 rpm stirring rotation
and 4 minutes stirring rotation. Microstructure testing, hardness testing, impact testing and tensile testing
were carried out to determined changes in material characteristic. The result showed that the addition of 1%
volcanic ash reinforcement gives the highest hardness and toughness number to aluminum composite material,
but the lowest ductility value. The highest aluminum composite material ductility value reached in the addition
of 3% volcanic ash reinforcement.
1 INTRODUCTION
Aluminum material is widely used because it has
several advantages, including formability and tensile
strength which can be improved through cold work-
ing processes or a heat treatment process (Callister,
2007)) . In the aluminum industry, it is usually com-
bined with other elements to get better product char-
acteristic. Composite is a material that composed
from a combination of two or more types of material
which are differentially macro in shape and compo-
sition(Waddoups and Halpin, 1974). It is produces
new material which is very different from the ba-
sic material. Al-Si-Cu-Mg is the aluminum compos-
ites that quite widely used in the industrial world be-
cause of their pour ability and good mechanical char-
acteristic in heat treatment conditions (Runxia et al.,
2010). The Stir casting method is the process of cast-
ing by melting the metal until it boils and then stirring
continuously until a vortex is formed (Hashim et al.,
1999). The reinforcement (in the form of powder) is
mixed gradually through the edges of the formed vor-
tex (Ajiriyanto, 2010).
Bhushan and Kumar (Bhushan and Kumar, 2011)
have conducted research on the the distribution ef-
fect of SiC particles on Al-7075 with the stir cast-
ing method and maintained temperature in the range
of 750 to 800o C. This experiment result shows that
the 5 to 15% SiC reinforcement added will increase
the 10.48% hardness value. In stirring with a rotation
of 500 rpm, metallographic result shows a uniform
distribution of granule structure with clearly visible
granule boundaries. This study took the stir casting
method from Bhushan and Kumar experiment by us-
ing the volcanic ash as a reinforcement material. The
stir casting method are suggested to reduce the poros-
ity in material composite (Wilastari et al., 2011).
Volcanic ash often referred to volcanic sand or
pyroclastic fall. It is a falling volcanic material that
sprayed into the air during an eruption, consisting of
large to fine-sized rocks. The volcanic ash that usedon
this experiment coming from the eruption of Mount
Kelud. Mount Kelud erupted on February 13th 2014
and sent wind-erupted volcanic ash in the form of fine
material falling in Yogyakarta. The result from Eu-
ropean Satelite Agency shows the chemical analysis
of Kelud volcanic ash which contains minimum of
55.05% silica (SiO2) (Guidebook et al., 2000). This
134
Mulyanti, J., Sukamto, ., Arviyanto, N., Anggraini, S. and Biddinika, M.
Experimental Study of Aluminum Composite Material by the Percentage Variation of Volcanic Ash Reinforcement.
DOI: 10.5220/0009879501340138
In Proceedings of the 2nd International Conference on Applied Science, Engineering and Social Sciences (ICASESS 2019), pages 134-138
ISBN: 978-989-758-452-7
Copyright
c
2020 by SCITEPRESS – Science and Technology Publications, Lda. All rights reserved