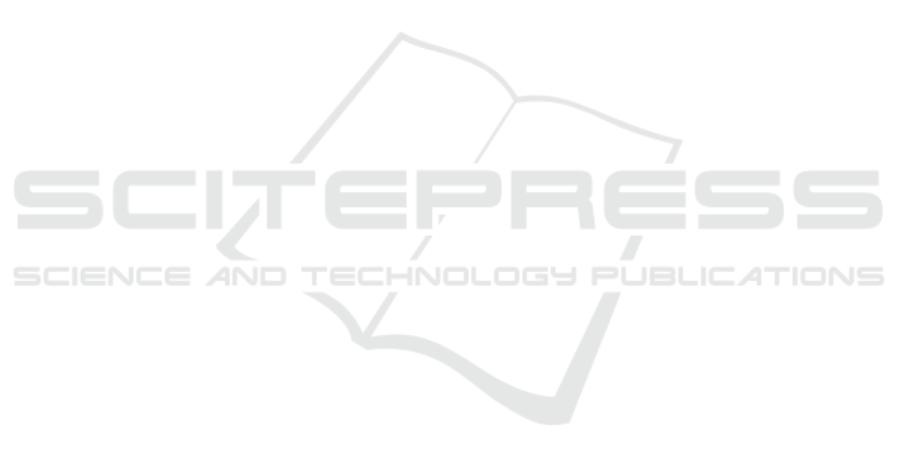
sponsibilities. They should also focus on building a
team and teamwork skills and manager should engage
in daily routine mentoring to increase efficiency in
production. Moreover, managers should ensure that
employees receive training to boost their problem-
solving skills (Shamim et al., 2016).
8.3 Compensation: in the industry 4.0 environ-
ment, the system of compensating employees should
be a reflection of the contributions of the employ-
ees towards the company. The organizations should
pay the employees based on their individual, group,
and organizational performance (Prieto and P
´
erez-
Santana, 2014). The managers should implement
strategies that will create a link between job perfor-
mance and the reward which includes payment of ad-
ditional incentives and profit sharing. Such a sys-
tem of compensation enhances a favorable environ-
ment for innovation and learning (Prieto and P
´
erez-
Santana, 2014).
8.4 Performance Appraisal: the best suitable per-
formance appraisal for industry 4.0 should focus on
improving results, behaviors, and the development
of employees. The employees should be updated
on their performance daily. Additionally, the per-
formance appraisal should be more of an objective
than subjective, and this implies that the performance
should be evaluated quantitatively by the use of ma-
trixes (Shamim et al., 2016). An ideal process of
performance appraisal should comprise of develop-
ment of performance standards, communicating the
expected results, evaluating the actual performance,
comparing the actual performance with the set stan-
dards, a discussion of the appraisal with the employ-
ees, and implementing corrective measures where
necessary. There are many methods of performance
appraisal, but management objectives (MBO) are the
most commonly used. MBO is a practical perfor-
mance approach that is compatible with the fourth in-
dustrial revolution (Shamim et al., 2016).
8.5 Job design: it is how an industry organizes
the tasks in a specific position including how and
when the tasks are accomplished and any other fac-
tors affecting work like the conditions and the order
in which the functions are to be completed. The job
design is an essential factor that enhances the climate
of learning and innovation and should be character-
ized by job rotation, extensive transfer of roles to the
employees, and flexible assignments in multiple ar-
eas. Moreover, the job design should cultivate a cul-
ture of teamwork and collaboration (Prieto and P
´
erez-
Santana, 2014). An industry 4.0 setting is character-
ized by learning and innovation, and as a result, a job
design can significantly help the company to adjust to
the business environment.
9 CONCLUSIONS
Industry 4.0 refers to the development processes that
took place in manufacturing industries and chain pro-
duction. The fourth industrial revolution is poised to
impact various areas of management including tech-
nology, data and analytics management, security of
data, regulatory compliance, risk management, val-
idation, and HR practices. The industry 4.0 envi-
ronment is characterized by learning and innovation
and influences various HR practices such as train-
ing, performance appraisal, compensation, staffing,
and job design. In staffing, innovativeness, learning,
and knowledge management capacity among the ap-
plicant is highly sought. Proper characteristics of a
candidate is the one who is open to new experience
including active imagination, attentiveness, intellec-
tual curiosity, flexible thinking, inner feeling, vari-
ety preferences, and interest. Employee training top
learning goal orientation are highly interested in par-
ticipating in challenging tasks, are always ready to
improve, have a tendency of achieving mastery, and
are more than willing to develop a new set of skills
and should be geared towards increasing the variety
of skills. And focus on building a team and teamwork
skills to increase efficiency in production. Moreover,
managers should implement strategies that will cre-
ate a link between job performance and the reward
which includes payment of additional incentives and
profit sharing. Performance appraisal should be more
of an objective than subjective, and this implies that
the performance should be evaluated quantitatively by
the use of matrixes. The last but not least, the job de-
sign is an essential factor that enhances the climate
of learning and innovation and should be character-
ized by job rotation, extensive transfer of roles to the
employees, and flexible assignments in multiple ar-
eas. Moreover, the job design should cultivate a cul-
ture of teamwork and collaboration. Therefore, the
managers should implement strategies that have pos-
itive impacts on these factors to facilitate the culture
of industry 4.0. The fourth industrial revolution will
increase the efficiency and quality of the produced
goods and services.
ACKNOWLEDGEMENTS
We would like to thanks Universiti Teknologi MARA,
Cawangan Pulau Pinang for the assistance and finan-
cial support rendered towards the production of this
paper.
ICCETIM 2019 - International Conference on Creative Economics, Tourism Information Management
108