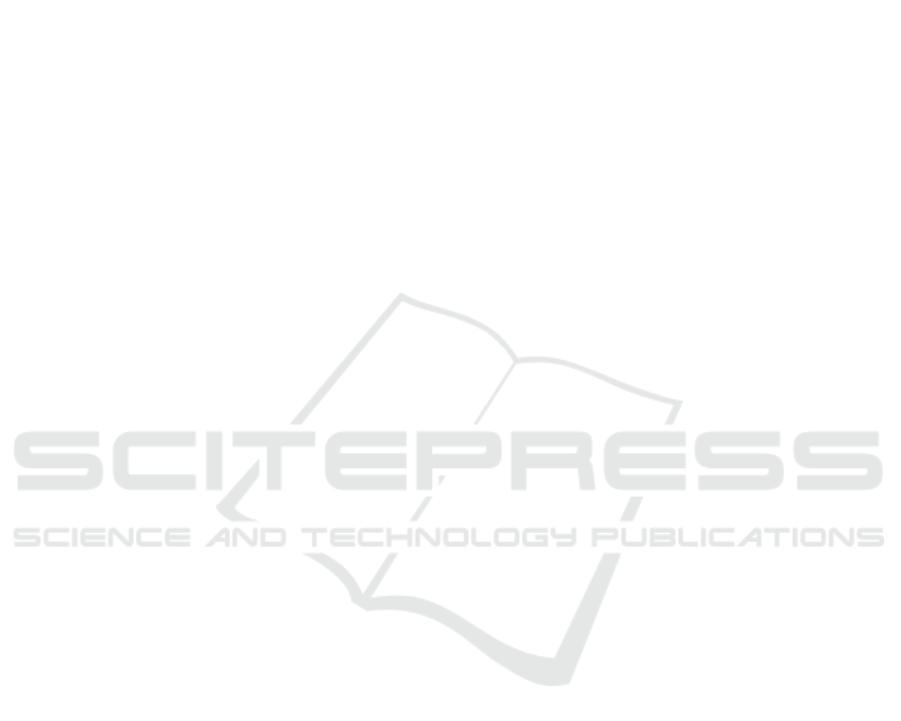
Chip Formation and Shear Plane Angle Analysis on Carbon Steel
Drilling using Solid Carbide Tools
Rieza Zulrian Aldio
Department of Mechanical Engineering, Universitas Islam Riau, Pekanbaru, Indonesia
Keywords:
Carbide Drill Bit, Chip Formation, Drilling, Shear Plane Angle
Abstract:
The analysis of the chip formation and shear plane angle from the drilling process are conducted as a mean to
determine the best drill bit used. Both aspects that influenced by the drill bit will define the machinability and
quality of the machining process. The aim of this experiment is to determine which is the best drill bit to use.
There are nine types of drill bit used in this experiment. All of the drills used are made of the solid carbide.
The chips are obtained from the drilling conducted by HPMT Industries Sdn Bhd. There are several types of
chips from the experiment, such as continuous, discontinuous and segmented chip. It is found that the chip’s
thickness and the helix angle of the drill bit affect the value of the shear plane angle created. Since all drill
bits are made of the same material, the helix angle of the drill bit become the main factor of choosing the best
drill bit because of the relationship between it influenced the shear plane angle value.
1 INTRODUCTION
One of the workpiece that is frequently and generally
used in the machining process is steel. There are sev-
eral types of steel used in the machining process such
as stainless steel, carbon steel and others. Each type
of steel has a different nature. Stainless steel is the
most common type of steel used in the manufactur-
ing industry. For example, corrosion resistant prop-
erties of stainless steel is due to a chromium content
of 10-12 percent of the total weight of stainless steel
(Kalpakjian and Schmid, 2006). Then there is also
carbon steel which is also often used in industry be-
cause of its low cost and ease of manufacture (Smith
and Hashemi, 2006).
One of the type of machining process which is of-
ten used for steel is drilling process. Drilling pro-
cess is the process by which drill bit will result in a
hole in the workpiece through direct contact between
the tool and the workpiece surface. Drilling process
is one of the most important machining processes in
the automotive and aircraft industries. (El-Sonbaty
et al., 2004) states that the industries required more
than 100,000 holes for small aircraft engines, mostly
used as a fastener. There are several forms of chips
that could resulted from the drilling process (Shar-
man et al., 2008). For example, the long continuous
chips are bad shape because chips will stick to the
surface of the tool and affect the performance of the
tool while performing the drilling process (Feng et al.,
2005). Long chips also make the chip evacuation be-
come more difficult and cause the drill to require more
power, which would increase the risk of broken drill
(Batzer et al., 1998). For this reason, the form and
evacuation process of the chips have important roles.
Chips will have direct contact with the flutes on
the twist drill during the drilling process. The geome-
try of the tool used will have an impact on the process
of moving chips (Abrao et al., 2008). Because of that,
the shape that commonly found has curls form, which
is according to the flute’s shape. (Bakkal et al., 2005)
in experiments on the chip’s morphology of drilling
metal glass found that there are six forms of chips
such as powder, short ribbon, long ribbon, long spi-
ral, long twisted ribbon and fan shape.
Movement of the chips on the flutes will cause
bending moments which can lead to chip fracture.
(Sakaurai et al., 1998) states that the chip will be
broken when the friction torque between the hole
wall and chip’s surface is beyond the chip’s torque.
The size of the chip will have impact on the sur-
face roughness, which will produce rougher surface
(Batzer et al., 1998). The performance of a tool can
be determined by the shape of the resulting chips.
Therefore, apart from the chip removal process,
the shape and length of chips resulted from the
drilling process should be reviewed in order to accom-
plish better performance of the drilling process. In
Zulrian Aldio, R.
Chip Formation and Shear Plane Angle Analysis on Carbon Steel Drilling using Solid Carbide Tools.
DOI: 10.5220/0009406203370341
In Proceedings of the Second International Conference on Science, Engineering and Technology (ICoSET 2019), pages 337-341
ISBN: 978-989-758-463-3
Copyright
c
2020 by SCITEPRESS – Science and Technology Publications, Lda. All rights reserved
337