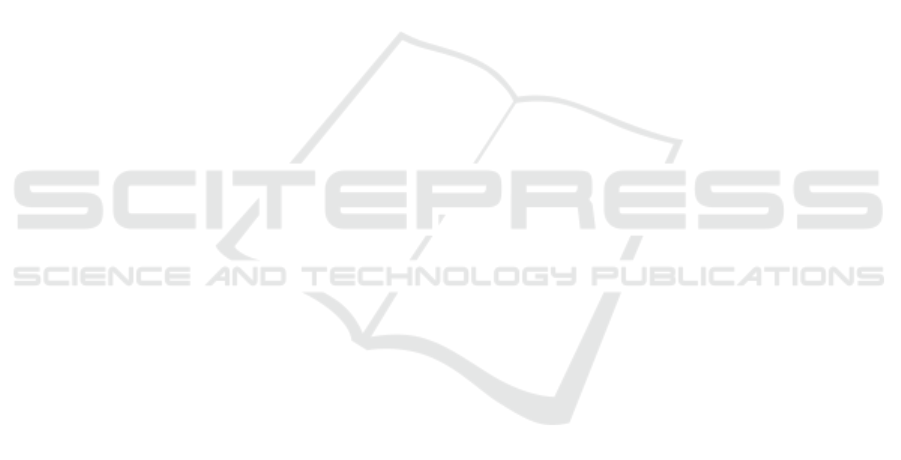
lowest because there is no dead zone (at 0 and 100
rpm) and vortex (at 300 rpm), so that radical OH
contact with rice husk is good. Good contact results
in more broken lignin bonds.
ANOVA statistical test results it can be ascertained
that the temperature and H
2
O
2
concentration have
an effect on the glucose level produced, the
higher the concentration of H
2
O
2
, the higher the
glucose produced, but decreases at a 10% H
2
O
2
concentration. Meanwhile, changes in operating
temperature from 25
◦
C to 45
◦
C do not have a large
effect on cellulose levels.
Understanding wax aging mechanisms is also very
important to fully understanding the process of the
formation of wax deposits in pipelines. Furthermore,
understanding these mechanisms and predicting the
CCN of particular crude oils would be helpful in
determining what chemical inhibitors would be most
effective for preventing wax build-up in pipelines
carrying those oils.
The continuing research into methods of
inhibiting wax deposition and removing deposits has
the potential of making the maintenance of crude oil
pipelines significantly easier, as it becomes easier
to optimize pigging frequency, to determine the
minimum pressure required to restart gelled lines,
or even to avoid the need for constant wax removal
procedures by finding a way to costeffectively
implement a promising method of control such as the
use of polar crude oil fractions or biological removal
measures.
Initial testing of oil containing paraffin wax is very
important to determine the wax content contained in
oil and the temperature at which wax begins to form.
then testing was carried out to test the oil containing
paraffin wax after adding a solvent to it, so these two
tests were conducted to see the effectiveness of the
solvent to overcome the problem of paraffin wax.
As for the tests carried out to identify the content
of paraffin wax in oil, which is cloud point testing
(ASTM D5771), cold point testing (ASTM D6371)
(Products & Products, n.d.) and pour point testing
(ASTM D97) (Methods & Oil, n.d.), this parameter
can be used as a reference whether the solvent mixed
with oil containing paraffin wax can be handled
properly or not. and also other supporting tests
such as density (ASTM D1298) (Standard, n.d.),
specific gravity (ASTM D1250) (Guide, 2004) and
0
API (ASTM D287) and viscosity (ASTM D445)
(Viscometers et al., 2009). where all these parameters
are the reference to the success of the solvent in
dealing with paraffin wax.
5 CONCLUSIONS
This work shows how the process of making
bioethanol from agricultural waste with optimal
conditions such as particle size, enzyme / acid
concentration, reducing sugar content, stirring speed,
temperature and fermentation time and also in this
work provides another alternative in overcoming
the problem of oil containing paraffin wax using
bioethanol which produced from agricultural waste
so that it can prevent environmental damage and
provide a more efficient cost alternative in dealing
with paraffin wax deposits.
ACKNOWLEDGEMENTS
A Great Thanks To Universitas Islam Riau and
Petronas Technology University for funding with
number 469/KONTRAK/LPPM-UIR-9-2018 For
Support In Writing This Paper.
REFERENCES
Abdurrahman, M., Ferizal, F., Husna, U., and Pangaribuan,
L. (2018). Possibility of wax control techniques in
indonesian oil fields. In AIP conference proceedings,
volume 1941, page 020001. AIP Publishing.
Afdhol, M. K., Haris, F., Amiliana, R. A., Hanafi, A.,
Ramadhan, I. T., et al. (2017). Production of
activated carbon from coffee grounds using chemical
and physical activation method. Advanced Science
Letters, 23(6):5751–5755.
Afdhol, M. K., Lubis, H. Z., Siregar, C. P., et al. (2019).
Bioethanol production from tea waste as a basic
ingredient in renewable energy sources. Journal of
Earth Energy Engineering, 8(1):21–26.
Aiyejina, A., Chakrabarti, D. P., Pilgrim, A., and Sastry,
M. (2011). Wax formation in oil pipelines: A critical
review. International journal of multiphase flow,
37(7):671–694.
Al-Yaari, M. et al. (2011). Paraffin wax deposition:
Mitigation and removal techniques. In SPE
Saudi Arabia section Young Professionals Technical
Symposium. Society of Petroleum Engineers.
Cai, W., Liu, R., He, Y., Chai, M., and Cai, J. (2018).
Bio-oil production from fast pyrolysis of rice husk in
a commercial-scale plant with a downdraft circulating
fluidized bed reactor. Fuel processing technology,
171:308–317.
Ebrahimi, M., Caparanga, A. R., Ordono, E. E., Villaflores,
O. B., and Pouriman, M. (2017). Effect of ammonium
carbonate pretreatment on the enzymatic digestibility,
structural characteristics of rice husk and bioethanol
production via simultaneous saccharification and
fermentation process with saccharomyces cerevisiae
ICoSET 2019 - The Second International Conference on Science, Engineering and Technology
320