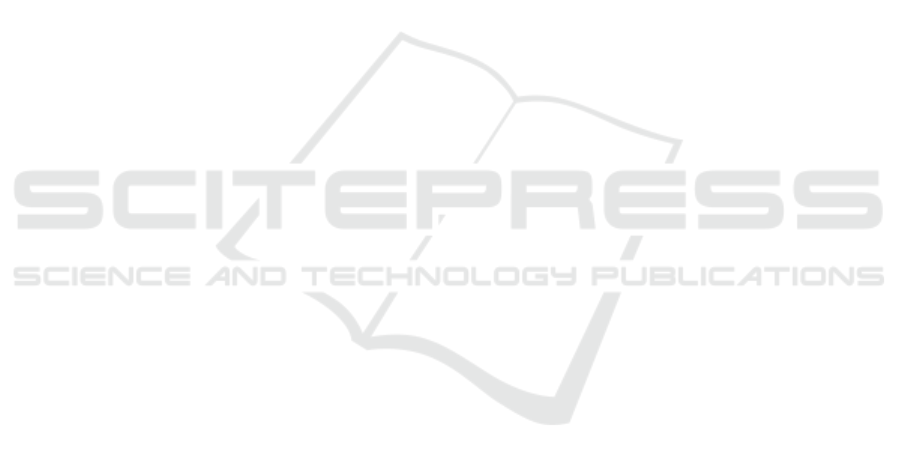
and resins (Abdel-Raouf, 2012). Emulsion in the
production field can be classified into three types,
Water-Emulsion in Oil (W/O);Oil Emulsion in Water
(O/W); and Complex Emulsion (Multiple/Complex).
Emulsion is an unstable system, according to (Wylde
et al., 2009), classifying the length of time an
emulsion system is separated based on its stability:
• Loose emulsion: is separated in minutes;
• Medium emulsion: separate in 10 minutes or
more;
• The emulsion sight will be stable for hours or even
days and in some cases, will not be able to be
overcome.
Some of the causes of the stability of the
emulsion are explained in the study (Kokal, 2005).
Such as agitation, the grain size, surfactant, effect
of pH, the composition of brine water, viscosity,
and temperature. For demulsification of emulsion,
injecting the demulsifire is one of the option for
separate the emulsion to dissolve dispersed phase
from the dispersing phase. The molecule of a
demulsifier will mobilize to the interface of oil-water
and separated both natural surfactant (asphaltenes
and resins) (Zhou et al., 2014). Over the years
there has been an over dependence on the use of
foreign/commercial demulsifiers this has been found
not to be quite effective in most cases due to
incompatibility with the nature of some kinds of
crude (Emuchay et al., 2013). For some cases it
will led to the challenge for the advanced studies to
locallyformulated demulsifier in result for improved
cost efficiency and effectiveness.
2 MATERIAL & METHOD
2.1 Material
The material we used for laboratory study of emulsion
and demulsification are a water bath (Memmert
WNB 14), heater and stirrer (Wisd.), digital scale
(Amastech), bottle for test (duran), several breakers
(Pyrex Iwaki TE-32), several graduated cylinder
(Pyrex), density bottle, and stopwatch. For producing
local demulsifier we used a commercial palm
oil, potassium hydroxide (KOH), aquades, glycerin
(C
3
H
8
O
3
), and citrus limon.
2.2 Method
Generally we used saponification, bottle test method,
and statistical test. In order to produce the liquid soap
as a base of local demulsifier, we used saponification
with following step based on (Naomi et al., 2013;
Sukeksi et al., 2017; Zulkifli and Estiasih, 2014).
Bottle test used to observing the result and converting
the data into graphic. As for statistical method will
be using statistic application that allows providing
which parameter (time of separation, temperature, or
injecting volume) most contribute for the test.
2.2.1 Production of Local Demulsifier
Local demulsifier (DKS) will be formulated with
saponification method, with the following step;a) 50
ml of palm oil commercial was added to a breaker
and heated with 80
◦
C for 30 minutes. b) 12.5 g of
KOH add into breaker along with 25 ml aquades and
then heated until homogenous; c) Add KOH + Aq into
palm oil and stir it with heater and stirrer in 80
◦
C, 800
rpm, for 3 hours and 20 minutes; d) For the last add
50 ml of aquades and stir for 5 minutes, then wait
the formula for 24 hours until the formula become
liquid. Both formulas are the local demulsifier for this
research.
2.2.2 Demulsification with Bottle Test Method
The following formulas that will be tasted are: a)
Local demulsifier (DKS); b) Local demulsifier +
lemon (DKL); c) Commercial demulsifier (DK);and
d) Base case (without adding demulsifier). Those
formulas will be injected to a bottle of sample
emulsion (1 ml, 3 ml, and 5 ml). Each volume are
tested in several temperature (40
◦
C, 60
◦
C, and 80
◦
C)
for 3 hours.
Emulsion separation was recorded at various time
intervals (Hirasaki et al., 2010).The process was
monitored for every 30 minutes in 3 hours. The step
based on (Erfando et al., 2019; Hirasaki et al., 2010)
3 RESULT
Table 1 is the properties data for sample oil. The
data was calculate to determine the type of oil. The
type of oil sample is heavy oil with SG = 0.929 and
20.8
◦
API. Figure 1-3 are the result of the test with
bottle test method in water bath.From those figures
we found out the best, highest, and also the bad
separation within the formulas.
Based on data, base case formula has the highest
separation in figures 1 (40
◦
C). Meanwhile not the
case in temperature of 60
◦
C and 80
◦
C. Formula
DKShas the highest separation value on figure 2 when
adding 5 ml concentration. Figures 2 shown that
ICoSET 2019 - The Second International Conference on Science, Engineering and Technology
300