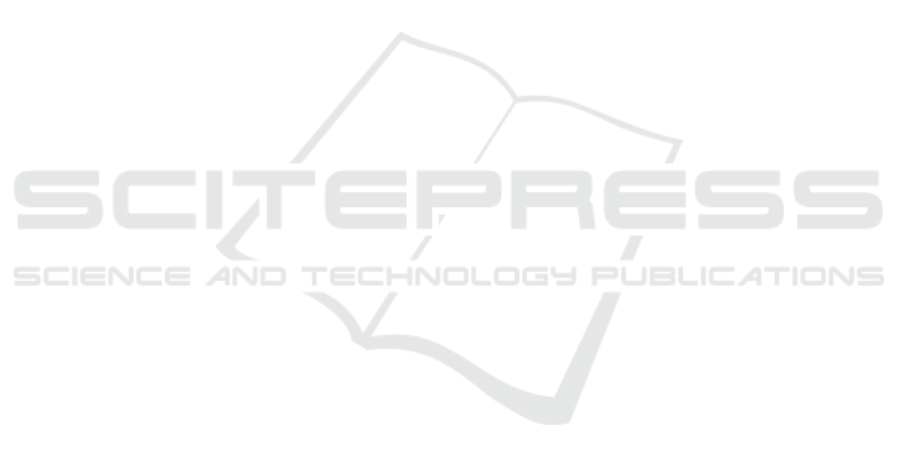
degradation rate of chitosan-roselle films determined
by DTG were lower when increased the roselle ratio
in the blend films at cure temperature of 50, 60 and
70
o
C. Thus, the chitosan-roselle films were degrade
faster when increased the roselle ratio in blend film
at ambient temperature. From the cure temperature
50, 60 and 70
o
C, the most optimum cure temperature
was 60
o
C which showed the lowest weight loss and
exhibited the highest heat resistance compared to
other cure temperature. SEM results showed the
surface structure of different ratio of chitosan-roselle
films which were cure at 60◦C. The higher ratio of
chitosan-roselle, the surface structure become
smoother. As conclusion, chitosan-roselle films have
higher heat resistance, degraded faster and have
smoother surface at most optimum cure temperature
(60
o
C). The smoother surface of chitosan-roselle
films made the higher thermal resistance of these
blend films.
ACKNOWLEDGEMENTS
This work was supported by Faculty of Mathematic
and Natural Sciences, Universitas Sumatera Utara
and School of Materials Engineering, Universiti
Malaysia Perlis.
REFERENCES
Alves, V., Costa, N., Hilliou, L., Larotonda, F., Gonçalves,
M., Sereno, A., & Coelhoso, I., 2006. Design of
biodegradable composite films for food packaging.
Desalination, 199(1-3), 331-333.
Betzabe Gonza Lez-Campos, Evgen Prokhorov, Gabriel
Luna-Bárcenas, Abril Fonseca-García, & Isaac
C.Sanchez., 2009. Dielectric relaxations of chitosan:
The effect of water on the α-relaxation and the glass
transition temperature. Journal of Polymer Science Part
B Polymer Physic, 47(22), 2259-2271.
Cissé M., Kouakou A.C., Montet D., Loiseau G., Ducamp-
Collin M.N., 2013. Food Hydrocolloids, 30 (2), 576-
580.
Dev Raj. and J. Yamini, 2013. Preparation and
Characterization of Pharmaceutical Grade Chitosan and
Hydrated Chitosan Gums for Topical Preparations.
Chem. Phys Journal. 1(9), 858-860.
Esam A. El-hefian and Abdul H. Yahaya., 2010.
Rheological study of chitosan and its blends: An
overview of chitosan, International Journal of
Carbohydrate Chemistry 4(02), 210-220
Portes, E., Gardrat, C., Alain, C., & Véronique, C., 2009.
Environmentally friendly films based on chitosan and
tetrahydrocurcuminoid derivatives exhibiting
antibacterial and antioxidative properties. Carbohydrate
polymers. 76(4), 578-584.
Jayakumar, N. Nwe, S. Tokura, H. Tamura, 2007. Sulfated
chitin and chitosan as novel biomaterials. International
Journal of Biological Macromolecules, 40(3), 175-181
Kammoun , M., Haddar , M., Kallel , T. K., Dammak, M.,
& Sayari, A., 2013. Biological properties and
biodegradation studies of chitosan biofilms plasticized
with PEG and glycerol. International Journal of
Biological Macromolecules.
Kumirska, Jolanta., Czerwicka, M., KaczyÅski, Z.,
Bychowska, A., Brzozowski, K., Thoming, J., &
Stepnowski, P., 2010. Application of Spectroscopic
Methods for Structural Analysis of Chitin and Chitosan.
Marine Drugs. 8(5), 1567-636.
Leceta, I., Guerrero, P., Ibarburu, I., Dueñas, M.T., de la
Caba, K., 2013. Characterization and antimicrobial
analysis of chitosan-based films. Journal of Food
Engineering, 116,(2013), 889–899.
Ngah, W.S.W., Fatinathan, S. and Yosop, N.A., 2011.
Isotherm and kinetic studies on the adsorption of humic
acid onto chitosan-H2SO4 beads. Desalination. 272,
293–300.
Norashikin, M. I., 2010. Fabrication and Characterization
of Sawdust. World Academy of Science, Engineering
and Technology, 716-719.
Ou, Y. Wang, S. Tang, C. Huang, and M. G. Jackson, 2005.
"Role of ferulic acid in preparing edible films from soy
protein isolate," Journal Food Eng, vol. 70, pp. 205-
210.
Tharanathan, R. N., 2003. Biodegradable films and
composite coatings: past, present and future. Trends in
Food Science and Technology, 14, 71-78.
Tuija Annala, 2007. Chitosan Film Preparation, Instruction
for laboratory experiments, Rev 0.
ZhenXing Tang, and JunQinQin, 2007. Use of chitosan gel
for the purification of protein, Engineering AND
Technology, College of Chemical Engineering and
Materials Science, Zheijiang University of Technology,
Hangzhou, Zhejiang, China.
Thermal Properties of Chitosan-roselle Films
273