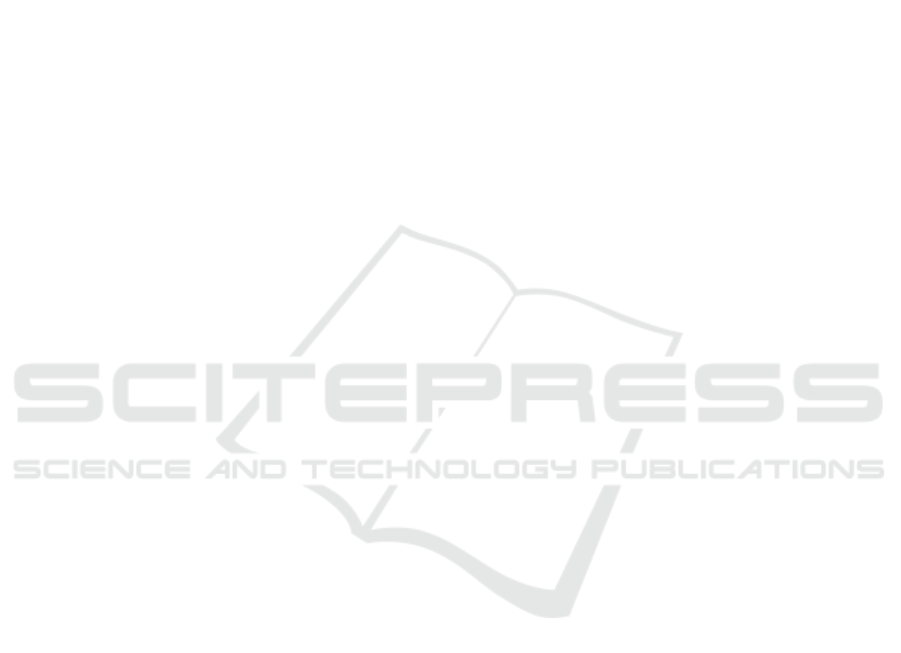
Analysis and Research on Defrosting Ventilation Pipe Deformation of
Automobile
Guangming Li
1, 2
, Congrui Zuo
3, a, *
, Yi Ma
1, 2
and Qike Huang
1, 2
1
Department of Mechanical and Energy Engineering, Shaoyang University, Shaoyang 422000,China
2
Key Laboratory of Hunan Province for Efficient Power System and Intelligent Manufacturing, Shaoyang
University,Shaoyang 422000,China
3
Institute Of Thermal And Energy Metrology, Hunan Institute Of Metrology And Test ,Changsha 410000,China
Keywords: Car, defrosting ventilation pipe, Deformation, The finite element.
Abstract: According to the market feedback, automobile defrosting ventilation pipe does not fit in the top 10 of
xiangtan geely automobile market quality problems. According to the detection of vehicles in this condition,
the reason for the deformation of automobile defrosting ventilation pipe position is that the gap between
instrument cover and ventilation pipe is less than 4mm. Ventilation tube ends around not level off, the
present state of collapse, and the intensity of this state collapse is due to the lack of overall deformation, for
deformation reasons of automobile ventilation pipe outlet increase 11 on the back of the improved design
scheme of reinforcement, using the method of three-dimensional modeling, design parameters, according to
auto defrost ventilation tube through the Pro/E 3 d software to complete the ventilation pipe before and after
the improvement model, using ANSYS Workbench software of finite element analysis was carried out on
the ventilation pipe before and after improvement, the maximum deformation analysis ventilation pipe
outlet, After the improvement, the deformation amount decreased from 10.643mm to 10.283mm, and the
maximum stress value of the ventilation pipe decreased from 85.783MPa to 55.781MPa, less than the
ultimate strength of 70MPa, verifying the rationality of the improved design, Solve the quality problem for
the enterprise, have very good reference value.
1 INTRODUCTION
According to the feedback from the market, the
defrosting ventilation pipe on the instrument table is
deformed, which affects the product quality and
brand image of the vehicle. Therefore, the
elimination of defrosting defrosting ventilation pipe
on the instrument has become an improvement
object. According to statistics: in January 2018, the
problem of unconformity of automobile defrosting
ventilation pipe was ranked among the top 10 in the
market, so the project was immediately started to
solve the problem of automobile. In the old parts
collection list, 200 vehicles of a certain model found
deformation of defrosting outlet position on the
instrument, as shown in figure 1:
Defrosting system (Tang Zhiliang, 2014) is an
important function to ensure the safe driving of
drivers in low temperature environment. Common
failure modes of automobile defrosting system
include no air supply, uneven air output,
deformation of ventilation pipes and pipelines, and
poor sealing of pipelines. Poor defrosting
performance reduces user experience and affects
driving vision, and serious defrosting will lead to
safety accidents. Therefore, as an important
functional part of an automobile, its quality needs to
be strictly controlled in the design stage and
manufacturing process.
In the stage of automobile design, the body
accessories will be rigorously verified. However, in
the manufacturing process, there are often
unqualified parts provided by suppliers, or improper
matching problems that cannot be found in the
actual assembly process. In this paper, we study the
defrosting export position ventilation tube
deformation is one of the common problems, in
order to solve the fault, eliminate defrost is not
completely safe hidden trouble, should be according
to the failure situation, analysis question reason,
make the corresponding improvement measures,
improve the quality of automobile products and
54
Li, G., Zuo, C., Ma, Y. and Huang, Q.
Analysis and Research on Defrosting Ventilation Pipe Deformation of Automobile.
DOI: 10.5220/0008867800540058
In Proceedings of 5th International Conference on Vehicle, Mechanical and Electrical Engineering (ICVMEE 2019), pages 54-58
ISBN: 978-989-758-412-1
Copyright
c
2020 by SCITEPRESS – Science and Technology Publications, Lda. All rights reserved