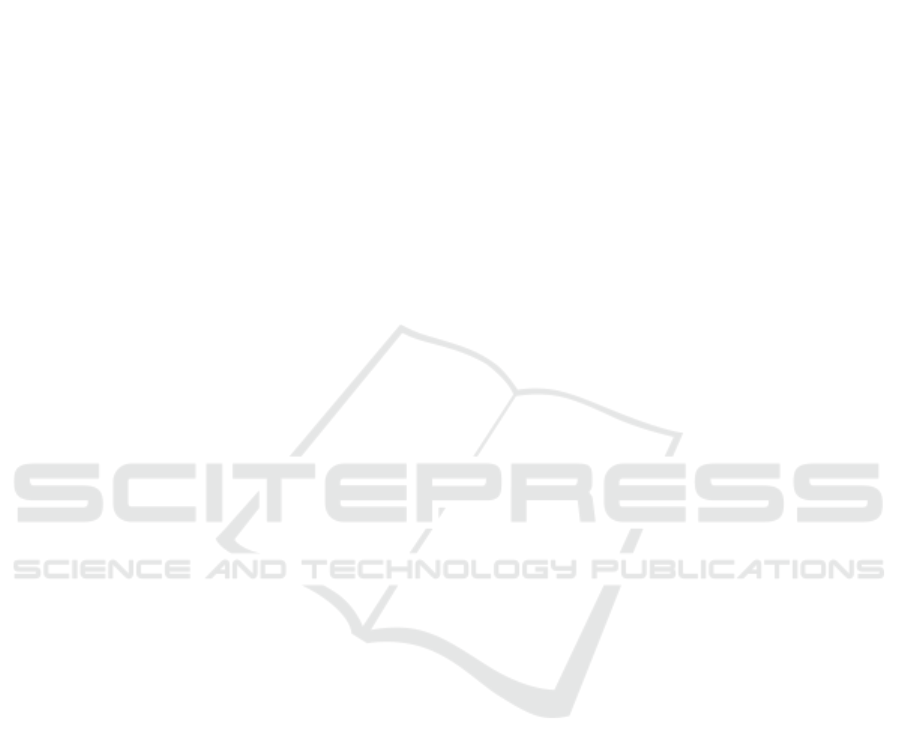
Research on Modeling and Lightweight of Automobile Hub
Fujian Yan
1, a
, Wei Xiong
1, b
1
Guilin University of Aerospace Technology, Jinji Road, Guilin, China
Keywords: Modeling, Lightweight, Hub.
Abstract: This paper studies the application of industrial design concept in automobile hub design, and uses the
localized design method to integrate Chinese cultural elements into the hub design and complete the creative
hub design. The radial load and bending moment load of the hub are analysed by finite element method to
verify the safety of the hub structure, and the lightweight design of the hub is carried out by analysing
different materials.
1 INTRODUCTION
The development of wheels has gone through a long
time. In ancient times, they were made of wood, but
now they are made of aluminium alloy. In some
western countries, the development history of
wheels can be traced back to a hundred years ago.
Aluminum alloy wheels appeared in 1920 (Yi, Deng
Li, 2012). They were originally manufactured by
sand casting and were only used in racing cars. In
1930, aluminium rolled rims and steel spoke wheels
were introduced and implemented in some simple
automobiles, which was a prerequisite for the
development of aluminium alloy wheels later. Due
to the impact of the global energy crisis, the
automotive industry has put forward an urgent need
for "lightweight", and aluminum alloy wheels have
begun to be widely used in ordinary automobiles
(Parry G, Roehrich, Jens, 2013).
China develops its own automobile brand by
drawing lessons from foreign advanced automobile
design and manufacturing technology. In order to
rapidly develop the automobile industry, China
constantly introduces foreign advanced technology
and cooperates with foreign enterprises. Therefore,
more and more automobile brands have entered
China and occupied the majority of the Chinese
automobile market. With the development of
domestic brands and the limitation of automobile
brand technology patents, Chinese manufacturers
have to pay high technology costs to foreign
enterprises. Therefore, it is of practical significance
to study the shape and lightweight of wheel hub for
the localization of automobiles.
2 MODELING DESIGN OF
AUTOMOBILE HUB
National culture is a culture created by a long-term
campaign and productive working country, which
brings together the wealth and resources of the
country. Chinese national culture is composed of 56
beautiful Chinese cultures. There are 56 different
cultures and related species, which are composed of
China's long-standing culture. Chinese elements are
built from Chinese national culture, which is a
symbol of Chinese national culture. In short, it is a
microcosm of national culture. It embodies the spirit
of national culture and is recognized by Chinese and
overseas Chinese.
2.1 Hub Modeling Scheme
Modeling design can choose words or graphics with
Chinese characteristics, contouring the selected
objects to reflect the characteristics of the selected
objects, and then simplifying their contours into
lines and graphics for early drawing design.
Scheme 1: The Chinese character "中" is used as
the design element, and "中" also represents a spirit
of the Chinese people. In ancient China, the doctrine
of the mean was regarded as a virtue by scholars and
the highest virtue by Confucianism. As shown in the
Figure 1.
Scheme 2: The design element is "flame" totem.
The ancients got inspiration from the sun and
created the decoration of "flame". The characteristic
of flame totem is circular, which conforms to the
Yan, F. and Xiong, W.
Research on Modeling and Lightweight of Automobile Hub.
DOI: 10.5220/0008849200150020
In Proceedings of 5th International Conference on Vehicle, Mechanical and Electrical Engineering (ICVMEE 2019), pages 15-20
ISBN: 978-989-758-412-1
Copyright
c
2020 by SCITEPRESS – Science and Technology Publications, Lda. All rights reserved
15