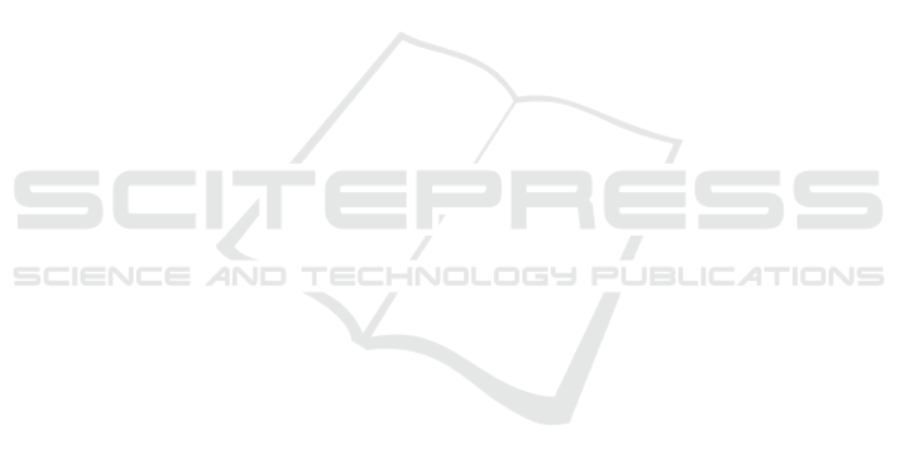
an initial abnomalities in the machine, so that we
could solve the machine's problem faster before it
affected another part (make the breakdown worst).
Regular lubrication keeps the part in machine run
smoothly as the setting of the parameter that has been
set in HMI. Tightening keeps all the mechanical part
stick to the initial places, so as the machine run there
will be no shifting on it.
Autonomous maintenance (CILT) that was
developed through FMEA-RCM processes could be
one of the solutions to boost machine peformance in
the food and beverage industry. FMEA-RCM
processes clearly gave us a deep analysis and helped
us to provide specific and relatively precise action to
be done in autonomous maintenance by operator. It
combined historical data of machine breakdown and
also analysis of failure probability in the parts of the
machine. It is also standardizes how operator
maintains their machine and share the responsibility
to maintain a machine between technician and
operator.
5 COPYRIGHT FORM
This paper has already got an agreement to be
published by the 2
nd
International Conference on
Inclusive Business in the changing world.
6 CONCLUSIONS
Autonomous maintenance provides benefits to our
production line. Which help us to :
a. Reduce breakdown level in filling machine
Type A in average from 11% to 4.2%
b. Reducing non added value activity (cleaning
funnel)
c. Sharing responsibilities in maintaining
machine with Engineering
d. Provide new habits and development to
operator skills : cleaning to inspect, inspect
to detect, detect to correct, correct to perfect
e. FMEA-RCM processes can be a usefull tool
to develop autonomous task in the food and
beverage industry. It combained data of
machine breakdown and also analysis of
failure probability in the parts of the
machine.
This project will be copied to another type of
machines in production. The flow process will be
conducted as it had been proven from this project.
ACKNOWLEDGEMENTS
We realize that AM implementations take a lot of
effort. In addition to developing a good analysis, we
are facing a challenge that is related to changing
operator habit. Making sure that monitoring and
consistency in doing every single task of AM are
conducted also take a lot of time (a lot of task and lot
of machine). Awareness on the top management,
supervisory level, and operators become the key
success to implement AM to reduce machine
breakdown. And continously upgrade AM task
related to the history of the machine after
implementation and eliminating unnecessary tasks.
REFERENCES
Carl S. Carlson, 2016. Understanding and Applying the
Fundamentals of FMEAs. Reliability and
Maintainability Symposium.
Catola, S., G., 1983. Reliability-Centered Maintenance
Handbook. Direction of Commander, Naval Sea
Systems Command.
Chen, C. 2013. A developed autonomous preventive
maintenance programme using RCA and FMEA,
International Journal of Production Research. Taylor
& Francis
Day, J., Troy, D., Heller, D., 2004. The Implementation of
Autonomous Maintenance (Part 1 in a series of the
Total Productive Manufacturing Experience).
CSMANTECH.
Nowlan, F. Stanley, and Howard F. Heap. Reliability-
Centered Maintenance. Report Number AD-A066579.
United States Department of Defense. 1978. Archived
from the original (PDF) on 2013-08-01.
Miranda, S. F., Lopes, I. S. 2015. Development of
Autonomous Maintenance in a Furniture Company.
World Congress on Engineering. Vol. II
Mugwindiri, K., Mbohwa, C., 2013. Availability
Performance Improvement by Using Autonomous
Maintenance - The Case of a Developing Country,
Zimbabwe. Vol I. World Congress on Engineering.
Owen, C., 2011. Total Productive Maintenance. Retrieved
from https://www.industryforum.co.uk
Developing Autonomous Maintenance through FMEA-RCM Models to Reduce
639