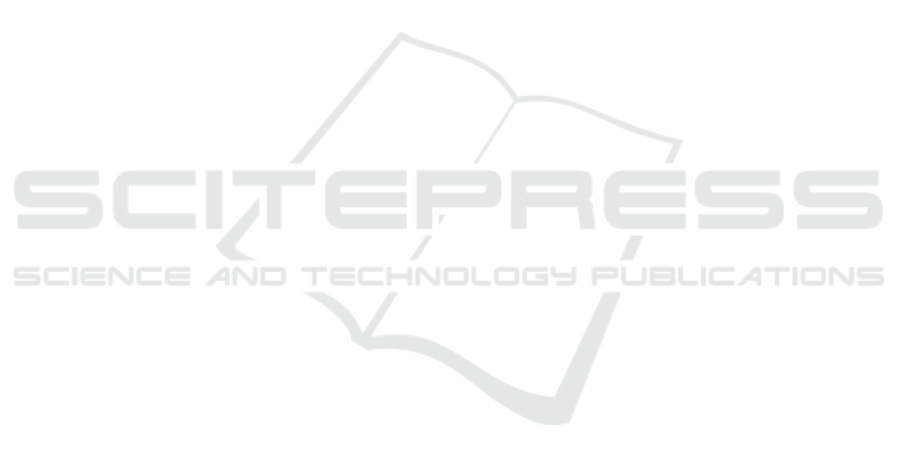
management of this vital resource is essential.
Furthermore, research suggests that improved
logistics will attain monetary and schedule savings,
reduce material waste, increase productivity and
safety (Jang et al., 2003; Poon et al., 2004; Shakantu
et al., 2003; Spillane and Oyedele, 2013). Thus,
effective construction logistics should provide
appropriate trade-offs involving costs and service in
the supply chain by integrating materials supply,
storage, processing and handling; site infrastructure
and equipment location; physical site flow
management and information management (Shakantu
et al., 2008).
Many industries attempt to integrate logistics
processes into logistics chains of suppliers and
customers, from obtaining raw material, through
manufacturing, distribution and final sale and service
to the end-users. Logistic processes, which are crucial
for successful completion of the project, are often
entrusted to external professionals specialised in
logistics services, such as logistics centres (Sobotka
and Czarnigowska, 2005). However, in the field of
construction, this tendency is to be developed.
Moreover, recent research has shown that, in the
management of material deliveries, an ad hoc,
intuitive approach is often adopted (Spillane and
Oyedele, 2017; Ying et al., 2014). Consequently,
there appears to be a significant need for an enhanced
understanding of transportation in a construction
context in order to deliver the full benefits from the
adoption of efficient construction logistics. The
purpose of this research is to address how the
efficiency of construction logistics can be improved
by using logistics centres. In order to evaluate the
effect of using a logistics centre, we provide a
simulation case study that measures logistics waste
with and without a logistics centre.
Next section surveys the related literature. It
follows by defining the problem environment and the
research methodology. The mathematical models and
scenario considered are then described. The paper
ends with conclusions and further research directions.
2 LOGISTICS ISSUES IN
CONSTRUCTION
2.1 Lack of Supply Chain Innovations
While many industries have experienced
performance improvements through supply chain
management initiatives, the construction industry is
yet to realise these improvements to the same extent.
Several researchers have explained the particular
features of the industry that hinder these potential
benefits, such as the fragmented structure of the
industry (Fadiya et al., 2015), the negative
consequence of arm-length relationships (Briscoe and
Dainty, 2005), and the lack of trust and commitment
among the firms involved in the process (Gadde and
Dubois, 2010).
Determining project logistics process requires a
wide range of construction project management
knowledge, such as knowledge of the building
materials market, financing, and managing
contractors’ approaches to supply. It also demands a
deep understanding of the impact of logistics on
project efficiency in terms of cost, quality and time.
Furthermore, it is of great impact to be aware of
logistics costs and their relationship to variables such
as batch size, place and time of the delivery, and
required storage conditions.
2.2 On-site and off-Site Logistics
Efficiency and effectiveness of a construction project
heavily depend on the integration between on-site and
off-site logistics. However, a lack of planning of
materials deliveries and unloading among
subcontractors and their site workforce causes
significant issues in this interface (Ying et al., 2014).
Previous research shows that substantial benefits can
be attained through the rearrangement of on-site
logistics (Lindén and Josephson, 2013). Off-site
logistics refers to supply logistics involving suppliers
of building materials.
The aim of logistics customer service is to ensure
that construction materials are appropriate and
available for construction operations. Thus, service
related factors affecting vehicle movements are
planning, training, loading and the logistics
management strategy. It is widely recognised that the
troublesome logistics in the construction industry is
influenced by the characteristics of the industry,
including the fragmentation of the construction
industry supply chain, lack of coordination and
communication among actors, inefficient planning
both on-site and off-site. From the project managerial
perspective, the real-time scheduling of materials
planned and keyed to the master plan for material
delivery is highly desirable. However, frequently this
is unachievable because of many factors, such as
inadequate detailed information at the
commencement of a contract, and considerable
variations during the construction stage.
Simulation of Vehicle Movements for Planning Construction Logistics Centres
259