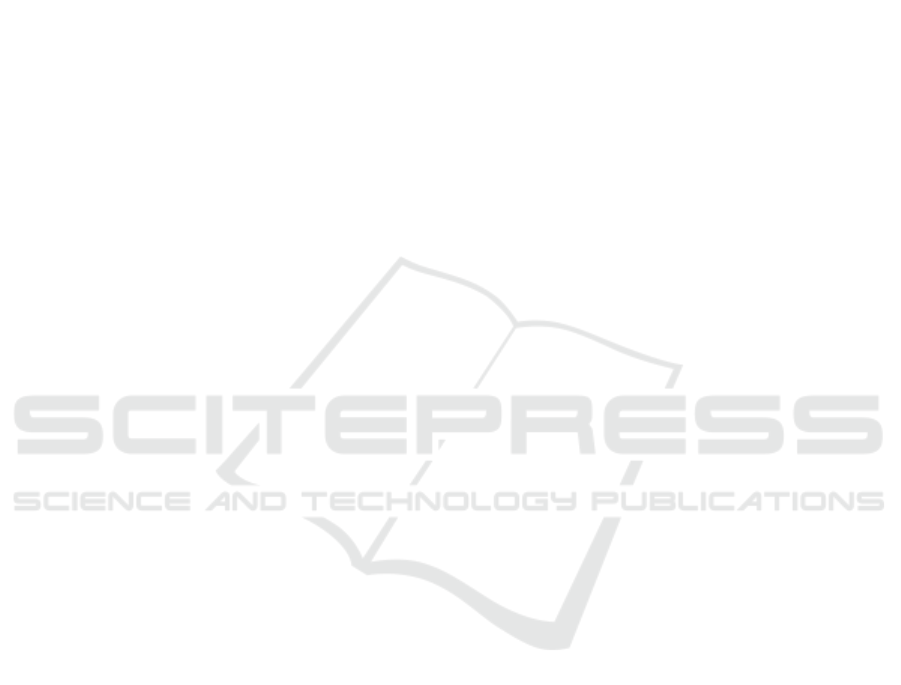
Optimization of CNC Milling Machining Time through Variation of
Machine Parameters and Toolpath Strategy in Various
Cross-sectional Shape on Tool Steels and Die Steels Materials
Wirawan Sumbodo, Kriswanto, Murdani, Idhhar Suwanda and Tri Syamsul Allam
Department of Mechanical Engineering, Universitas Negeri Semarang, Semarang, Indonesia
idharsuwanda3@gmail.com, syamsul165@yahoo.com
Keywords: Machine Time, Simulation, Toolpath Strategy, Optimization.
Abstract: CNC machines are manufacturing machines for mass products that required to operate quickly. Machining
Time efficiency will reduce production costs. This paper presents an optimization of CNC milling Machining
Time from a variations of machine parameters, toolpath strategy and variations in cross sectional shapes. The
method is simulation use simulation software and optimization with constraint machining time. The program
is based on parameters (speed, feed rate, and width of cut) for pocket roughing operations. The cross section
shape of the workpiece is rectangular with 5 variation size. The width of cut for roughing work is 30%, 50%,
and 80%. Endmill uses a diameter of 12 mm and 4 flutes. The optimal machining time value in each cross
section workpiece is generated from the zigzag toolpath strategy and 80% width of cut. The optimum
Machining Time of W1 is 3 minutes 11 seconds, W2 is 5 minutes 55 seconds, W3 is 12 minutes 25 seconds,
W4 is 5 minutes 18 seconds and w5 is 12 minutes 19 seconds. The toolpath strategy that produces the largest
Machining Time high speed and true spirals toolpath strategy.
1 INTRODUCTION
Computer Numeric Control machine (CNC) is a
manufacturing machine technology widely used in
industries. CNC machine is used to produce high-
precision mass products quickly. CNC machines with
high capability produce products quickly called high
speed machine (HSM) CNC machines. The HSM
milling machine has a spindle speed of up to
60,000rpm. High speed machining is one of the
modern technologies that increases the efficiency,
accuracy and quality of workpiece compared to
conventional cutting (Awale, 2015). CNC milling
machines generally have spindle speeds of 3000 rpm
to 6000 rpm. CNC machines with high spindle rates
can produce high feed rate and small machine time.
Small Machining Time is the efficiency of production
time which reduces production costs. Machining time
estimation is a critical step towards an optimal and
practical production plan (Borkar, 2014). Gavril
(2016) study about increase productivity and cost
optimization in CNC manufacturing with the results
that by increasing the working time by 32.49% may
achieve an economy up to 10.33% for the
manufacturing cost.
The milling CNC machine with a small spindle
rate so that the feed rate produced is small while the
Machining Time is large. Parameters that affect the
value of Machining Time other than spindle rate and
feed rate are stepover and toolpath strategies.
Determination of stepover parameters and
toolpath strategies affects machine time. (Romero,
2013), and (Gologlu, 2008). Dimitrov (2012), Saroj
(2013), Daneshmand (2013), Prajapati (2013), and
Minquiza (2013) study of the reduction in Machining
Time CNC milling, the results show that setting
toolpath parameters using the help of CAM software
can reduce machining time. These parameters include
speed, stepover percentage, feed rate, and toolpath
strategy. Daneshmand (2011) investigating potential
ways to reduce Machining Time with the help of
CATIA
®
and CAM, the results of machining time are
reached when using a zigzag toolpath strategy. Study
on Machining Time by Akmal (2013) shows that the
parallel spiral toolpath strategy has the smallest
Machining Time compared to other toolpath
strategies by reason of a parallel spiral strategy using
84
Sumbodo, W., Kriswanto, ., Murdani, ., Suwanda, I. and Allam, T.
Optimization of CNC Milling Machining Time through Variation of Machine Parameters and Toolpath Strategy in Various Cross-sectional Shape on Tool Steels and Die Steels Materials.
DOI: 10.5220/0009006800840092
In Proceedings of the 7th Engineering International Conference on Education, Concept and Application on Green Technology (EIC 2018), pages 84-92
ISBN: 978-989-758-411-4
Copyright
c
2020 by SCITEPRESS – Science and Technology Publications, Lda. All rights reserved