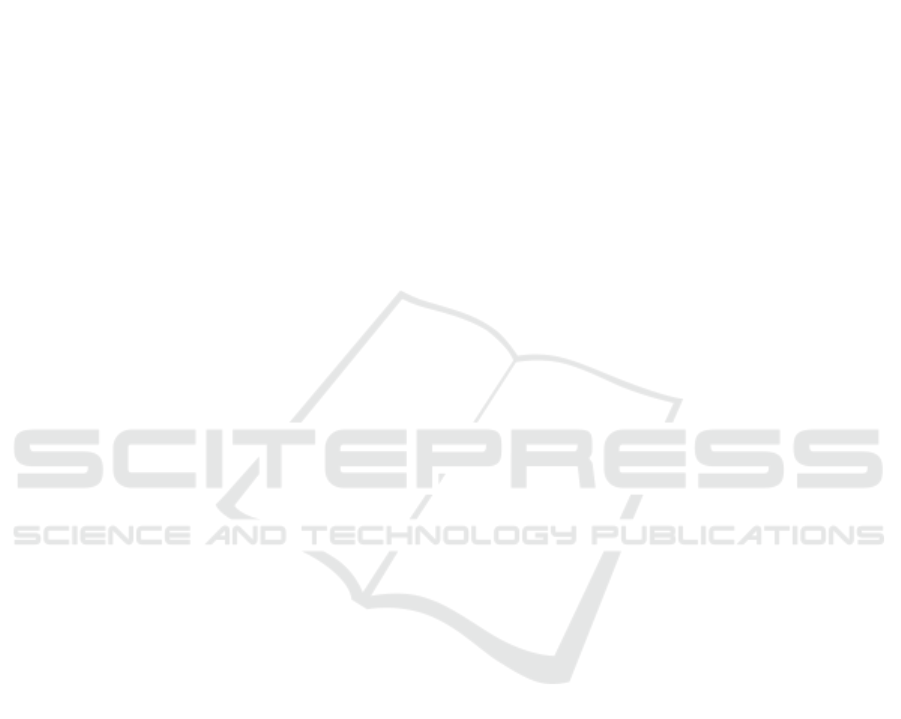
The Motion Response Analysis of Floating Jack-Up Rigs in the
Operating Condition
Universitas Islam Negeri Sunan Ampel, Jl. A. Yani 117 Surabaya, Indonesia
Keywords: floating jack-up, motion, wave, six degree of freedom
Abstract: Natural gas reservoirs near the seabed (shallow gas) make drilling activities prone to blowout. Using a
modified jack-up in a floating state will facilitate evacuation to avoid gas explosion. The floating jack-up is a
misuse of the concept of jack-up structure design which must be operated in a fixed structural condition. This
issue requires further investigation regarding the feasibility of the drilling operation process. Motion response
of the floating structure is revealed in order to explore the feasibility of the operation of the jack-up. In this
study, the motion response of the floating bodies will be compared by varying the jack-up leg length immersed
in the water. The site reviewed in this analysis is in the Madura Strait, Indonesia. The floating jack-up was
modeled and analysed in the MOSES offshore platform design and simulation software. Results show that
the response amplitude operator of pitch motion has the most significant response in each variation. From
motion validation with rules it can be concluded that the heave motion of this structure exceeded criteria limits
for BOP and riser operations but is allowed for drilling activities. The obtained results show that a drilling
process in the Madura Strait site using a floating jack-up could possibly be operated by lowering the legs
until it reaches five meters above the seabed without running BOP and risers.
1 INTRODUCTION
Jack-up rigs are offshore drilling platforms with legs
that can be raised and lowered in the installation
process. The concept of designing a jack-up structure
is that it combines the advantages of fixed structure
buildings such as platform jacket legs and floating
platforms such as floating barges. The jack-up is a
self-elevating unit. The transportation and installation
phases are done during floating conditions, while the
spud cans will be jacked onto the seabed during the
operating or drilling phase (DNV, 1996).
Seabed sub-surface soil conditions containing
shallow gas where the trap of natural gas reservoirs
located near the seabed floor will cause the area to be
prone to blowout. The presence of shallow gas may
possibly cause blowout that will damage the jack-up
structure. The penetration of jack-up legs will make it
difficult to structure evacuation, because the jacking
process of the jack-up legs will take a long time. This
problem raises an idea: what if this offshore building
structure is operated under conditions where the legs
are not fixed on the sea floor or operated in floating
condition. Jack-up legs do not touch the sea floor,
meaning jack-ups will always be floating in the ocean
so evacuation procedures can run smoothly and
prevent damage to the structure. A jack-up structure
with hanging legs may prove to be the solution. In
accordance to the concept of jack-up design, the
floating structure of the jack-up clearly does not fulfil
the design rule. It may be questioned whether the
jack-up can remain stable in a state of operation
(drilling activities), how the structure moves, if it can
still withstand environmental loads such as wind,
currents and waves. With this analysis, we will find
out whether the floating jack-up can be operated in
drilling or operating conditions.
This research focuses on jack-up rigs of the three
independent leg type with K-braced truss legs. It
discusses how the motion response of the floating
jack-up was subjected to the environmental load. The
location of study of this simulation is in the Madura
Strait in Indonesia, which has a water depth of 57m.
This paper describes and compares the structural
motion analysis of six variations of immersed jack-up
legs which were subjected to environmental loads.
The behavior of motion response of each variation
was recorded.
Sawiji, A.
The Motion Response Analysis of Floating Jack-Up Rigs in the Operating Condition.
DOI: 10.5220/0008908100002481
In Proceedings of the Built Environment, Science and Technology International Conference (BEST ICON 2018), pages 191-196
ISBN: 978-989-758-414-5
Copyright
c
2022 by SCITEPRESS – Science and Technology Publications, Lda. All rights reserved
191