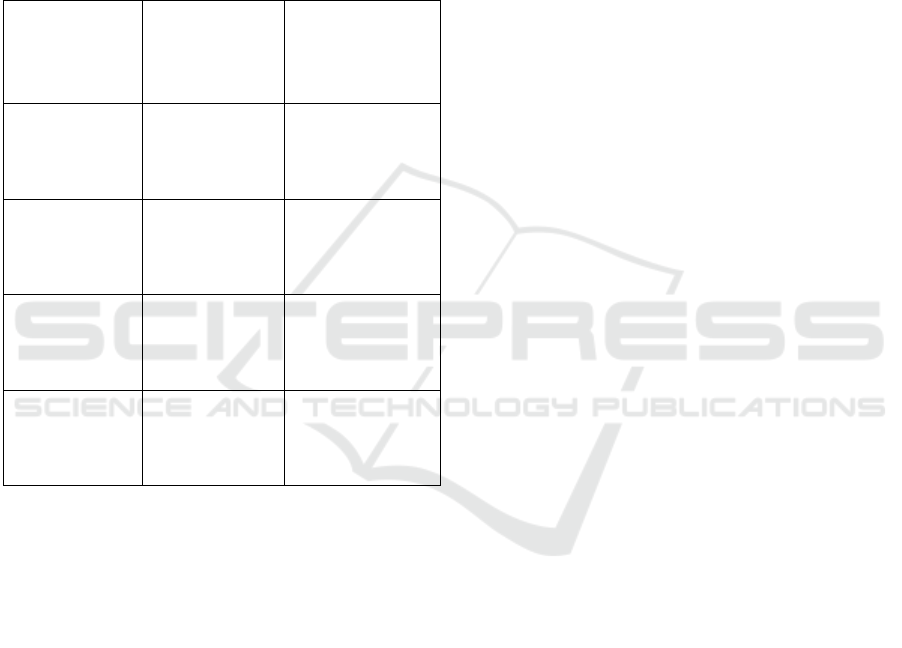
The increase of temperature from 1000°C to
1050°C reduced the density for about 2%. It aligns
with the previous study by Huda and Astuti (2012),
showing that adding 20°C heating temperature
reduced the brick density. The effect of adding
duration of calcination temperature reduced the
density.
3.1.3 Water Absorption
The density in every composition and calcination is
shown in Table 7.
Table 7: Water Absorption of fine ALWA
Water absorption
(ASTM) (%)
The water absorption value is shown in Table 7
shows that almost all of the values meet the
requirement (ASTM C 330-04) less than 20%. The
water absorption value is in the range of 11-20.5%.
The smallest water absorption occurs at calcination
temperature of 1050 °C for 6 hours by 11-12.5%.
The addition of fly ash to water absorption of fine
ALWA reduces the water absorption of fine ALWA.
The addition of calcination temperature from 1000°C
to 1050°C reduces water absorption of fine ALWA.
The addition of duration of calcination temperature
reduces water absorption of fine ALWA
3.2 X-Ray Diffraction Analysis
Xray diffraction analysis for fine ALWA FA-0-1000-
6, fine ALWA FA-0-1050-6, fine ALWA FA-30-
1050-6, fine ALWA FA-50-1050-6, fine ALWA FA-
0-1050-4, analysis fine ALWA FA-30-1050-4, fine
ALWA FA-50-1050-4 discribe below.
The diffraction pattern is shown in figure 6 forms
scattered and peaked. It shows that in temperature
1000°C duration 6 hours, the minerals that appeared
are quartz (SiO2), anorthite (Al2CaO8Si2), hematite.,
calcite (CaCO3), indialite (Al4Mg2O18Si5) and
silimanite (Al2SiO5).
Xray diffraction of fine ALWA 100% Sidoarjo
mud, with calcination temperature 1050°C for 6 hours
is shown in figure 7.
The diffraction pattern presented in figure 7
shows that mineral occure are anorthite
(Al2CaO8Si2), quartz (SiO2), hematite (Fe2O3),
Indialite (Al2Mg2O18Si5), Calcite (CaCO3).
Silimanite has not been detected in this sample.
Xray diffraction of fine ALWA 70% Sidoarjo
mud-30% Fly Ash, with calcination temperature
1050°C for 6 hours is shown in figure 8.
The diffraction pattern presented in figure 8
shows that minerals occuref in higher peak are quartz
(SiO2), anorthite (Al2CaO8Si2) and hematite
(Fe2O3). In the short peak, calcite, silimanie, and a
little indialite can be found.
Xray diffraction of fine ALWA 50% Sidoarjo
mud-50% Fly Ash, with calcination temperature
1050°C for 6 hours shown in figure 9.
Xray diffraction of fine ALWA 100% Sidoarjo
mud, with calcination temperature 1050°C for 4 hours
shown in figure 10.
The diffraction pattern shown in figure 10 show
that mineral occure in higher peak are anorthite
(Al2CaO8Si2) quartz (SiO2), and hematite (Fe2O3).
The short peak occur calcite and indialite.
Xray diffraction of fine ALWA 70% Sidoarjo
mud-30% Fly ash, with calcination temperature
1050°C for 4 hours shown in figure 12.
The diffraction pattern shown in figure 12 show
that mineral occure in higher peak are anorthite
(Al2CaO8Si2) quartz (SiO2), and hematite (Fe2O3).
The short peak occur calcite, silimanite and indialite.
Xray diffraction of fine ALWA 50% Sidoarjo
mud-50% Fly ash, with calcination temperature
1050°C for 4 hours shown in figure 13.
The diffraction pattern shown in figure 13 show
that mineral occure in FA-50-1050-4 same with FA-
30-1050-4.
Study of Fine Artificial Lightweight Aggregate (ALWA) from Sidoarjo-Mud and Fly Ash with Different Calcination and Composition
181