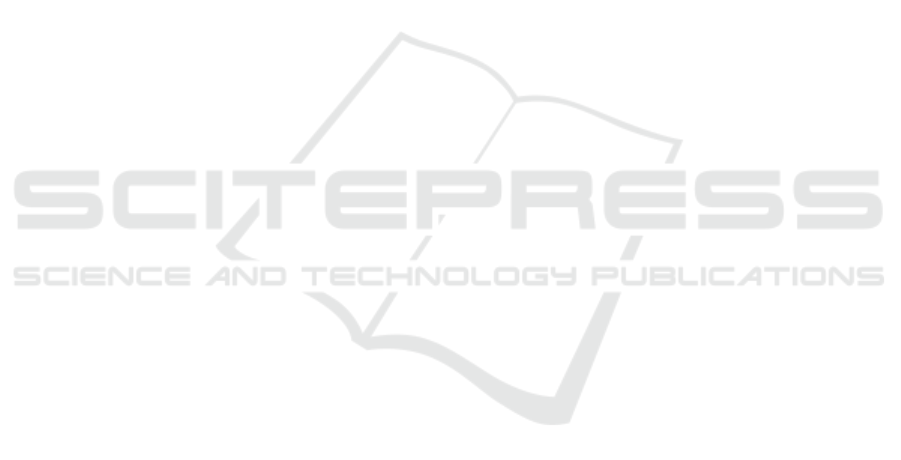
cause WISES is categorized as a ship. The low as-
pect ratio and thick wing of WISES are easy to con-
struct. Furthermore, a pressurized cabin is unnec-
essary, thus reducing fatigue strength requirements.
For WISES navigates only in very low altitude, its
governing regulations are those of ships. Therefore,
requirements of safety, structural strength and pilot
trailing of WISES are lighter than in aviation laws.
It differentiates WISES from seaplanes those tend to
be high-cost airplanes.
Although a WISE appears similar to an airplane,
it has different properties from the standpoint of com-
mercialization. The ship experiences hydrodynamic
loads while taking off from and alighting on water.
Although there is no explicit limitation to the length
of water runways, the speed at take-off and alight has
a great influence on the ship’s economy. As accel-
eration before take-off occurs on water, the required
power of the vehicle is nearly proportional to the cube
of take-off speed. In addition, the maximum hydrody-
namic load of the ship is proportional to the square of
the speed. Therefore, a decrease in take-off speed al-
lows for a smaller engine and lighter structural weight
of the vehicle. Slow take-off and alighting (STOA)
capability is important for reducing both the construc-
tion and operational cost of the ship (KAWAKAMI
and AKIMOTO, 2006).
2.3 Experimental and Numerical Study
on WISE
The aerodynamic characteristics of 2D airfoils and 3D
WISE have been investigated both experimentally and
numerically by other researchers (Fuwa and Hirata,
1993). The general conclusion is that there is a re-
duction in induced drag and an increase in lift as the
ground is approached. As a result, both aerodynamic
efficiency and aerodynamic loading are increased due
to ground proximity effects. Pioneer researchers such
as Kumar (1972), Irodov (1974), and Staufenbiel and
Schlichting (1988) have analyzed various aspects of
WISE craft longitudinal stability.
Ho et al. (2008) also investigated the effects of
end plate (numerically) on a highly cambered aero-
foil. Aerofoil shape optimization underground effect
had been carried out by Moore et al. (2002). Studies
have shown that the ground has a significant influence
on the pressure distributions along the wing surface.
As a WIG vehicle moves forward, the speed of the on-
coming air gradually decreases under the lower wing
surface, and dynamic pressure changes to static pres-
sure. This increased pressure is called an air cushion
or a ram effect, and it necessitates a longer runway for
landing.
Technical feasibility of WISE vehicles (possibil-
ity to develop lifting systems taking advantage of SE
and able to perform stable flight in proximity to an un-
derlying surface) has been proven both through model
experiments and full-size trials of prototypes.
Different aerodynamic configurations have been
developed and examined, each of them showing ad-
vantages and disadvantages from the viewpoint of
specific applications. A tendency is observed for con-
figurations to evolve into all-wing (flying wing) or
composite wing schemes, the latter being particularly
advantageous from the viewpoint of efficient take-
off, aerodynamic (economic) viability in cruise and
a wider range of pitch stability.
Extensive wind tunnel tests were carried out in
the closed-type wind tunnel at Pusan National Uni-
versity. Lift and drag forces and the pitch moment
of NACA6409 was measured as several aerodynamic
parameters such as the aspect ratio (AR), the angle of
attack (α), ground clearance (h/c) and endplate shape
were varied. In addition, the smoke trace technique
was employed to visualize the flow pattern around
the wing during the ground effect. This experimen-
tal study presents how the aerodynamic performance
of NACA6409 during the ground effect is influenced
by various design parameters (Jung et al., 2008).
In 2006, Al-Atabi (2006) fitted three small lifting
surfaces to the tip of a NACA0012 wing similar to that
of the wing tip feathers, the tests show that tip-sails
could decrease the induced drag, increase the longi-
tudinal static stability and break the tip vortices. In
1977, Withers and Timko (1977) recorded motion pic-
ture of black skimmers flapping and skimming over a
water surface by the camera. The flight velocities and
the wing-beat frequency were achieved by analyzing
the films. The conclusion is that ground clearance
has a great effect upon the foraging energetics and
daily energy balance of skimmers. The experimen-
tal results of Ground Effect of a wing mounted with
tip sails are introduced by Sun and Dai (2015). The
study has evaluated the flow control efficiency of pri-
mary feathers to the wing of a pelican skimming over
the water surface. Compared with a NACA4412 pro-
totype wing, the experimental results show that, for
the same ground clearance, the lift coefficient of the
tip-sails wing increases significantly and the stalling
angle of attack decreases, the drag coefficient keeps
nearly unchanged at a small angle of attack (AOA)
and decreases obviously at higher AOA.
Numerical Study on the Section Design of a Wing in Surface Effect
155