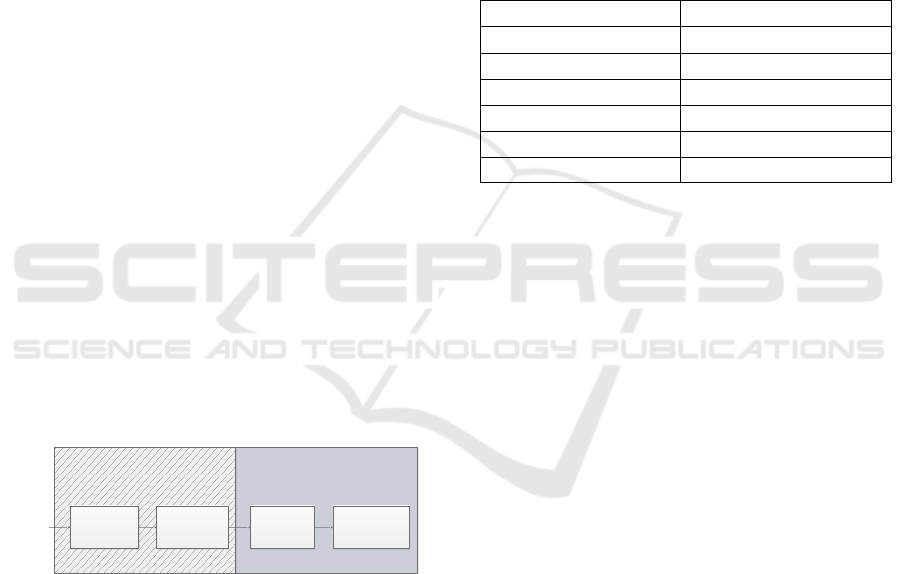
2 METHODOLOGY
2.1 Project Introduction
At present, “ZhuYuan sludge incineration project” is
the largest sewage sludge drying and incineration
project that has been operated in China. The scale of
this project is 150 t/DS, and the Sludge calorific
value is 13700 kJ/kg. The project mainly includes
sludge receiving and storage system, sludge drying
system, sludge incineration system, waste heat
utilization system, flue gas treatment system and
auxiliary system. The sludge is dried by indirect
drying method, and the heat source is steam. The
sludge is incinerated by fluidized bed incinerator.
2.2 Boundary of Research System
In the study of sludge life cycle assessment, it is
generally regarded as the starting point of life cycle
evaluation, and the scope of the study includes the
whole process from production, transportation,
recycling, and treatment to final disposal. This paper
focuses on the research on the disposal and disposal
parts. Along with the sludge itself entering the
system, it also includes auxiliary energy and other
raw materials; the output of the system is useful
products and recycled energy.
Sludge treatment processes and the disposal
route are presented in Figure 1. “Thickening” and
“Dewatering” process are finished in Waste water
treatment plant. “Drying” and “Incineration” process
are finished in Sludge treatment plants. Research
boundary is limited to sludge treatment plant.
Figure 1: Sludge treatment processes and disposal routes.
2.3 Carbon Footprint Method
The Carbon footprint is defined as the total amount
of greenhouse gases (GHG) produced to directly and
indirectly support human activities, usually
expressed in equivalent tons of carbon dioxide
(CO
2
). It is a common method to calculate the
impacts of human activities on Global Warming
(IPCC, 2006).
Although the study found many gases affecting the
climate system, only 6 major types of greenhouse
gases were included in the “Kyoto Protocol”,
including CO
2
, CH
4
, N
2
O, HFCs, PCFs and SF in
the carbon footprint assessment. As the
quantification of these gases cannot be directly
measured, they are estimated by calculating GHG
emissions of each processes involved in the studied
activities. The amount of each gas is then converted
with an emission factor in CO
2
equivalent (CO
2eq
)
according to their Global Warming Potential (GWP),
which showed in Table 1 (IPCC, 2006).
Table 1: Considered gases in carbon footprint and their
Global Warming Potential at 100 years (GWP
100
).
GHG emission of sludge treatment can be divided
into direct part and indirect part:
Direct part: GHG emissions directly occurring
in sludge treatment and disposal.
Indirect part: GHG emissions caused by
electricity and fuel consumption during sludge
drying and incineration process.
2.4 Calculation Method
At present, the domestic calculation methods of
GHG emissions in sludge treatment and disposal
process are mainly divided into actual measurement
method and model estimation method.
The actual measurement method needs to
measure the relevant parameters of the emission
source or the operating equipment through the actual
testing method, and calculate the carbon emissions
by the measured data approved by the environmental
protection department. Most of calculations used
model estimation method. These studies are of great
guiding significance, but the results are largely
dependent on the hypothesis and scenario analysis.
In order to make the research more practical, the
carbon footprint of “ZhuYuan sludge incineration
project” is calculated by actual measurement method
and model estimation method.
Waste water treatment plants
MEEP 2018 - The Second International Conference on Materials Chemistry and Environmental Protection
274