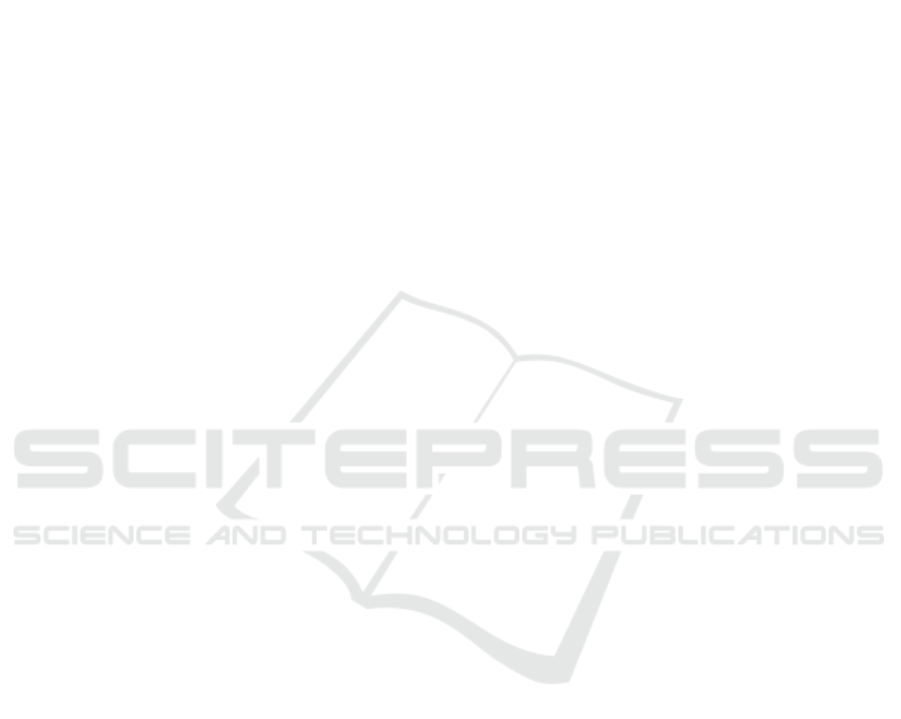
Effect of Applied Voltage on Properties of Micro-arc Oxidation
Coating on TC4 Alloy
Wei Zhou, Yunlong Zhang
*
, Chaojun Cui, Zhigang Wang, Haifeng Zhang and Qingxiang Yang
Anyang institute of technology, Huang he street, Anyang city, P. R. China
Keywords: Micro-arc oxidation, Yttrium nitrate, Micro-hardness
Abstract: In order to resolve biological toxicity of TC4 titanium alloy, the micro-arc oxidation (MAO) technology was
introduced to fabricate ceramic coating on the surface of TC4 titanium alloy. Yttrium nitrate was introduced
into the silicate electrolyte system as additive. The micro-structure, phase composition, surface morphology
and micro-hardness of MAO coatings were characterized. When applied voltage increased, the content of
rutile-TiO
2
in the coating increased. The maximum value of surface roughness was about 11μm as applied
voltage was 300V. The maximum micro-hardness was about 5210MPa.
1 INTRODUCTION
Ti-based alloys are widely used in aerospace, weapon
and other fields owing to their low density, high
specific strength and excellent corrosion resistance
(Boyer, 1996; Wang, 2015; Wang, 2017). TC4 alloy
has biological toxicity, so it is seriously limited in the
clinical medicine applications. Therefore, various
modifying techniques such as salt cyaniding (Lai and
Wu, 1993), plasma immersion ion implantation
treatment (Yilbas and Shuja, 2000), laser treatment
(Yerokhin, 2000), micro-arc oxidation (Mandl, 2007)
and PVD process, were introduced to
improve performances for practical applications. The
main purpose of surface treatment is to keep
vanadium elements in titanium alloy matrix and
avoid its releasing.
Micro-arc oxidation technology (MAO) has
distinguished advantage to prepare ceramic coating
on the Mg, Ti and Al alloys. The ceramic coating can
improve both wear and corrosion resistance of alloys.
Rare earth materials have important scientific
research value, so they are widely used in the field of
metal matrix modification. In this work, yttrium
nitrate was introduced into the silicate electrolyte
system as additive. The TC4 alloy was oxidized
under different applied voltages by MAO method.
The micro-structure, phase composition, surface
morphology and micro-hardness of MAO coatings
were characterized.
2 EXPERIMENTAL
Before micro-arc oxidation treatment, TC4 alloy
were cut into the size of 20mm×20mm×2mm. The
specimens were polished by SiC sandpapers with grit
sizes of 600#, 1000# and 2000#, respectively. And
they were rinsed by distilled water, acetone several
times and dried. The electrolyte is composed of 30g/L
Na
2
SiO
3
·5H
2
O, 10g/L EDTA-2Na, 2g/L KF and
1.5g/L Y(NO
3
)
3
in aqueous solution. In MAO
process, applied voltage was designed as 240V, 270V,
300V, 330V and 360V, respectively. And the
samples were correspondingly nominated as S1, S2,
S3, S4 and S5. The MAO equipment with power of
100kW was composed of an AC power supply and
ultrasonic systems. The stainless steel container and
TC4 alloy were used as cathode and anode separately.
For comparison, MAO was carried out at 330V
without Y(NO
3
)
3
in the electrolyte, and the sample
was nominated as S6. After MAO treatment, the
samples were rinsed with distilled water and dried.
X-ray diffraction device (Bruker D8 Advance) was
used to analyse the phase structures with a scan rate
of 4°/min. Surface morphology and roughness was
analysed by Olympus self-focusing microscope and
field emission scanning electron microscope. At least
five areas within 480μm×640μm were measured to
calculate surface roughness. The hardness was tested
by digital micro-hardness tester (HVS-1000A,
Huayin L.L.C., China). The average hardness was
surveyed at least five spots. The Olympus
164
Zhou, W., Zhang, Y., Cui, C., Wang, Z., Zhang, H. and Yang, Q.
Effect of Applied Voltage on Properties of Micro-arc Oxidation Coating on TC4 Alloy.
DOI: 10.5220/0008187101640167
In The Second International Conference on Materials Chemistry and Environmental Protection (MEEP 2018), pages 164-167
ISBN: 978-989-758-360-5
Copyright
c
2019 by SCITEPRESS – Science and Technology Publications, Lda. All rights reserved