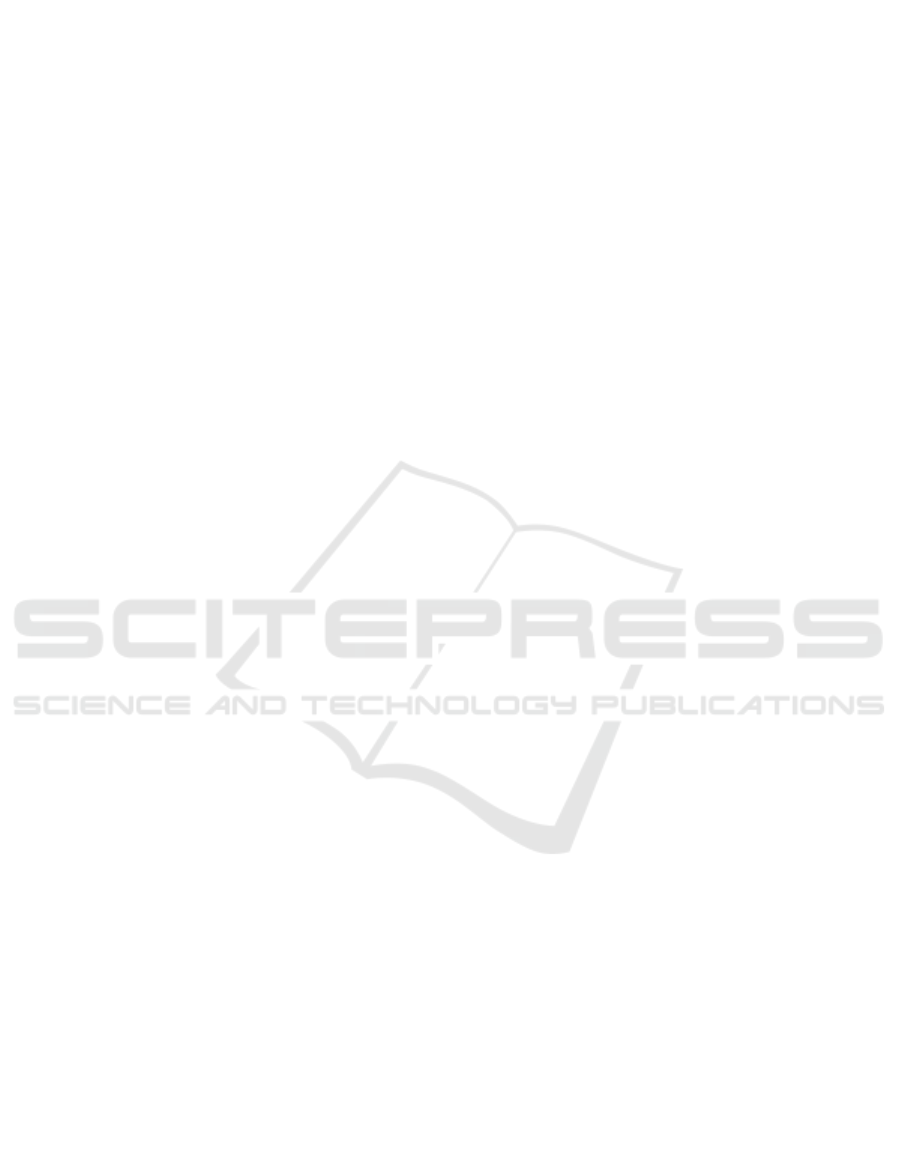
surface? A review on the recent progress in the preparation of superhydrophobic surfaces J.
Chemical Society Reviews 36(8) 1350-1368
[2] Wang S, Liu K, Yao X and Jiang L 2015 Bioinspired surfaces with superwettability: new insight
on theory, design, and applications J. Chemical reviews 115(16) 8230-8293
[3] Bayer I S 2017 On the durability and wear resistance of transparent superhydrophobic coatings J.
Coatings 7(1) 12
[4] Zhang Y L, Xia H, Kim E and Sun H B 2012 Recent developments in superhydrophobic surfaces
with unique structural and functional properties J. Soft Matter 8(44) 11217-11231
[5] Barthlott W and Neinhuis C 1997 Purity of the sacred Lotus, or escape from contamination in
biological surfaces J Planta 202(1) 1-8
[6] Huang W H and Lin C S 2014 Robust superhydrophobic transparent coatings fabricated by a
low-temperature sol–gel process J. Applied Surface Science 305 702-709
[7] Chen Y, Zhang Y B, Shi L, Li J, Xin Y, Yang T T and Guo Z G 2012 Transparent
superhydrophobic/superhydrophilic coatings for self-cleaning and anti-fogging J. Applied
Physics Letters 101(3) 033701
[8] Xu Q F, Wang J N, Smith I H and Sanderson K D 2009 Superhydrophobic and transparent
coatings based on removable polymeric spheres J. Journal of Materials Chemistry 19(5)
655-660
[9] Ganesh V A, Dinachali S S, Raut H K, Walsh T M, Nair A S and Ramakrishna S 2013
Electrospun SiO
2
nanofibers as a template to fabricate a robust and transparent
superamphiphobic coating J. RSC Advances 3(12) 3819-3824
[10] Kim Y D, Shin J H, Cho J Y, Choi H J and Lee H 2014 Nanosized patterned protective glass
exhibiting high transmittance and self-cleaning effects for photovoltaic systems J. physica
status solidi (a) 211(8) 1822-1827
[11] Cho W K and Choi I S 2008 Fabrication of hairy polymeric films inspired by geckos: wetting
and high adhesion properties J. Advanced Functional Materials 18(7) 1089-1096
[12] Liu Y, Song Y, Niu S, Zhang Y, Han Z and Ren L 2016 Integrated super-hydrophobic and
antireflective PDMS bio-tem plated from nano-conical structures of cicada wings J. RSC
Advances 6(110) 108974-108980
[13] Son J, Kundu S, Verma L K, Sakhuja M, Danner A J, Bhatia C S and Yang H 2012 A practical
superhydrophilic self cleaning and antireflective surface for outdoor photovoltaic
applications J. Solar Energy Materials and Solar Cells 98 46-51
[14] Liu K, Du J, Wu J and Jiang L 2012 Superhydrophobic gecko feet with high adhesive forces
towards water and their bio-inspired materials J. Nanoscale 4(3) 768-772
[15] Lee W, Jin M K, Yoo W C and Lee J K 2004 Nanostructuring of a polymeric substrate with
well-defined nanometer-scale topography and tailored surface wettability J. Langmuir
20(18) 7665-7669
[16] Shen K B, Yang H, Liu J, Wang W, Huang Y, Zhou Z H and Shen S 2012 Fabrication and
characterization for innate super-hydrophilic SiO
2
thin films J. Materials Science Forum
743-744 377-381
[17] Liu X and He J 2009 One-step hydrothermal creation of hierarchical microstructures toward
superhydrophilic and superhydrophobic surfaces J. Langmuir 25(19) 11822-11826
[18] Choi H, Lee S, Park S H, Ko J S and Yang H 2017 Water repellency of large-scale
imprinting-assisted polymer films J. Macromolecular Research 25(6) 584-590
[19] Cassie A B D and Baxter S 1944 Wettability of porous surfaces J. Transactions of the Faraday
society 40 546-551
A Novel and Facile Method to Fabricate SiO2 Nano-pillar Arrays on Glass Surface
499