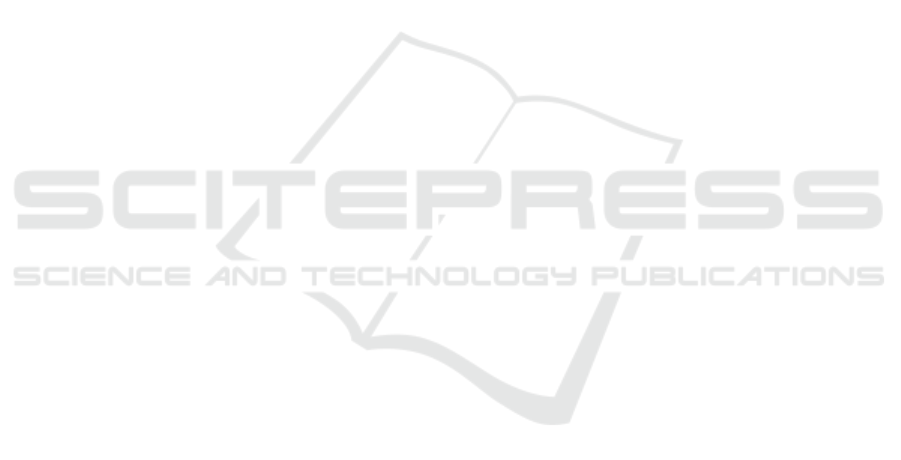
Crystal Plastic Finite Element Simulation and Texture
Analysis of Aluminum
J S Qi, Z M Yue
*
, K Cao, Y S Li and J Gao
School of Mechanical, Electrical and Information Engineering, Shandong University
at Weihai, China
Corresponding author and e-mail: Z M Yue, yuezhenming@sdu.edu.cn
Abstract. The application of crystal plasticity in finite element codes is widely regarded as a
valid way to represent the elasto-plastic behaviour of metal. Based on the rate-dependent
crystal plastic constitutive model, the forming behaviour of the pure aluminium is studied in
this paper. The stress distribution during the stretching, compres sing, and shearing
deformation is simulated, and it is concluded that the heterogeneity of the material
deformation can be well reflected through the simulation with the crystal plasticity theory. At
the same time, the pole figure and orientation distribution function (ODF) are obtained based
on the numerical data, and the evolution of polycrystalline texture are analysed and predicted
based on the simulation results obtained with the proposed crystal plasticity model.
1. Introduction
Accurate description of the anisotropic behavior of metal materials in the plastic forming process is
always an attractive research issue in the calculation of plastic mechanics research and engineering
applications. Therefore, a variety of plastic theories about metal materials have emerged. The crystal
plasticity (CP) theory starts from the crystal structure of the material and explores the macroscopic
deformation mechanism, so as to better understand the macroscopic plastic deformation of the
material, reveal the law of material deformation, and optimize the forming behavior of the material
[1].
In this paper, together with the crystal plastic finite element method (CPFEM), the
single-crystalline and polycrystalline simulations of pure aluminum have been conducted with user
material subroutine UMAT/ABAQUS. And through analyzing the pole figures and ODFs, the
micro-texture of the material in the compressing, shearing deformation is compared. Therefore, it is
of great significance to material forming, material strengthening, and plastic processing of materials.
2. Crystal plasticity theory
The CP theory has been widely used in the literature [2]. In this study, the single crystal constitutive
equation is chosen.
364
Qi, J., Yue, Z., Cao, K., Li, Y. and Gao, J.
Crystal Plastic Finite Element Simulation and Texture Analysis of Aluminum.
In Proceedings of the International Workshop on Materials, Chemistry and Engineering (IWMCE 2018), pages 364-370
ISBN: 978-989-758-346-9
Copyright © 2018 by SCITEPRESS – Science and Technology Publications, Lda. All rights reserved