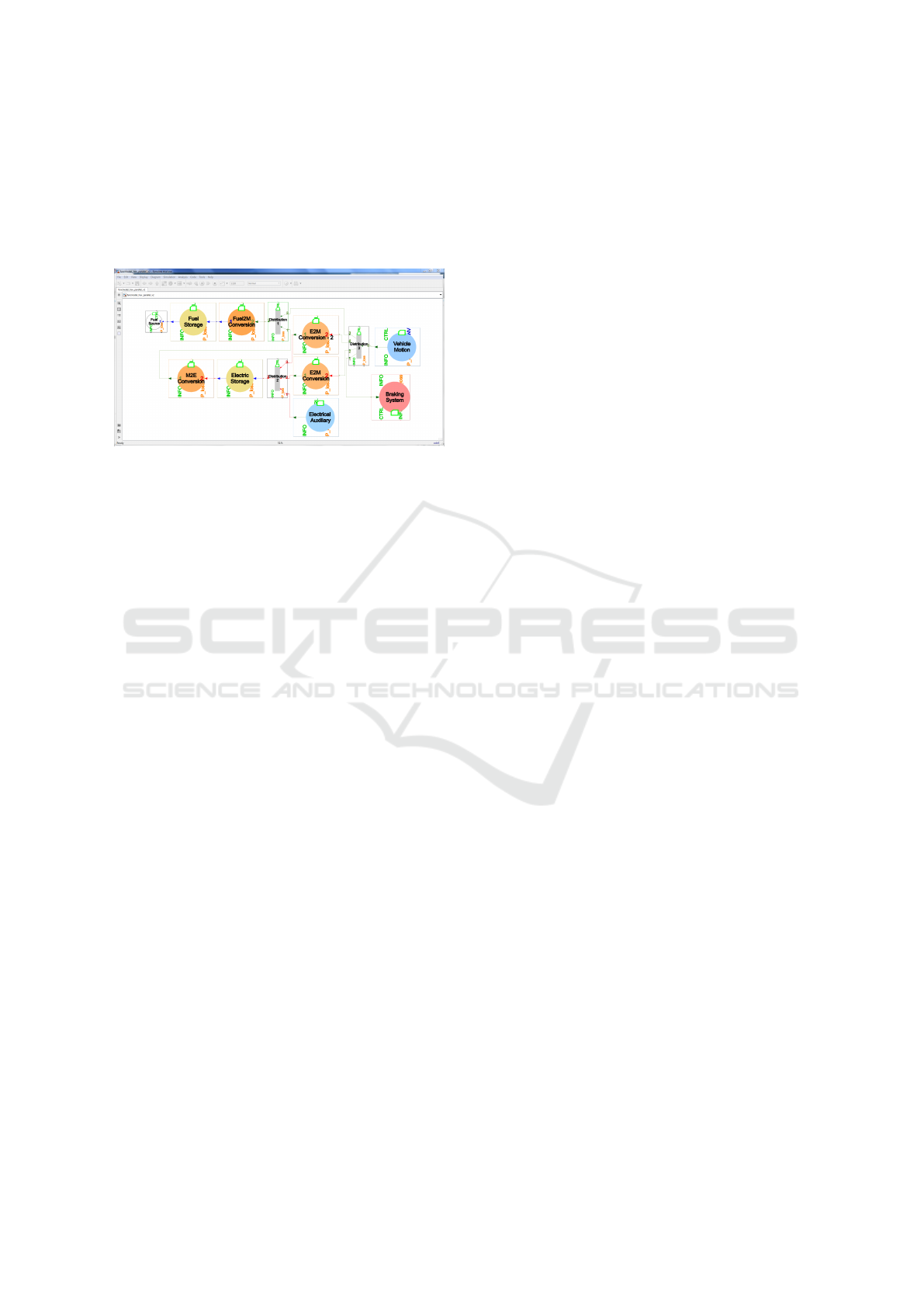
the new configuration can be validated in a fast and
efficient way. An example of this interesting feature
is demonstrated in Fig. 16, highlighting the modular-
ity of functional modelling. Compared to Fig. 9, an
additional component is added to the system: a sec-
ond electric machine used for traction.
Figure 16: Reconfigurated HEV model.
Therefore, with faster simulations compared to
multi-physical modeling and ease of reconfigura-
tion, the functional modeling becomes a very useful
methodology for system modeling and simulation.
5 CONCLUSION AND FUTURE
WORK
In the presented work, a methodology of modeling a
control architecture was proposed using a functional
energy-based approach. The methodology was ap-
plied to a PHEV with WLTC use case, using Mat-
lab/Simulink simulation environment. The intercon-
nection between functional model and multi-physical
model serves to add a high level control to the multi-
physical system representation. At functional level of
abstraction, where the energy system exchanges need
and supply, the energy management algorithms are
easier and faster to adapt at this level of representa-
tion. Based on the functional model, the proposed
concept simplifies the control design and computes
appropriate multi-physical reference signals for the
multi-physical model.A first perspective of the pro-
posed modeling methodology is to establish a gener-
alized method to interconnect the two levels of mod-
eling.
Also, the simulated multi-physical model does not
contain gear box for the ICE. The components (ICE or
EM) models can be acknowledged as simple, which
means that the dynamic behaviour of the system and
its components cannot be thoroughly researched.
Future works intend to enhance the accuracy of
multi-physical model (by improving the components
models or by adding additional ones) in order to have
a more reliable validation. On the other hand, robust-
ness of the control architecture will be further investi-
gated.
Another perspective is to improve the energy man-
agement strategy used at functional level: more effi-
cient algorithms for need/supply distributions should
be developed and integrated into the simulation mod-
els for further validation. In this work, distributors
use priorities for power need/supply distribution. For
an optimal power split, an otimization-based energy
management algorithm should be used.
Finally, the proposed method for control architec-
ture design will be tested on different types of appli-
cations that need an optimal energy management like
water treatment systems or building energy manage-
ment systems.
REFERENCES
Brunet, J., Flambard, L., and Yazman, A. (2005). A hard-
ware in the loop (HIL) model development and im-
plementation methodology and support tools for test-
ing and validation car engine electronic control unit.
Lecce, Italy. International Conference on Simulation
Based Engineering and Studies, TCN CAE.
Fauvel, C. (2015). Approche modulaire de l’optimisation
des flux de puissance multi-sources et multi-clients,
´
a
vis
´
e temps reel. PhD thesis, Nantes, France.
Fauvel, C., Claveau, F., and Chevrel, P. (2014). Energy
management in multi-consumers multi-sources sys-
tem: a practical framework. pages pp.2260–2266,
Cape Town, South Africa. IFAC World Congress.
Fiani, P., Taleb, L. A., Chavanne, S., and Mokukcu,
M. (2016). Mod
´
elisation pour la conception et
l’
´
evaluation de syst
`
emes complexes. Revue Ing
´
enieurs
de l’automobile, vol.841.
Le Moigne, J. (1977). La th
´
eorie du syst
`
eme g
´
en
´
eral,
th
´
eorie de la mod
´
elisation. PUF, Paris, France.
Mokukcu, M., Fiani, P., Chavanne, S., Taleb, L. A., Vlad,
C., Godoy, E., and Fauvel, C. (2016). A new con-
cept of functional energetic modelling and simulation.
pages pp.536–541, Oulu, Finland. The 9th Eurosim
Congress on Modelling and Simulation.
Penalva, J. (1994). Sagace: la mod
´
elisation des system
`
es
dont la ma
ˆ
ıtrise est complexe. volume vol.94, pages
pp.536–541, Montpellier. 2nd International Confer-
ence on Integrated Logistics and Concurrent Engi-
neering (ILCE).
Sciarretta, A. and Guzzella, L. (2007). Control of
hybrid electric vehicles. IEEE Control Systems,
vol.27:pp.60–70.
Suh, N. (1998). Axiomatic design theory for sys-
tems. Journal of Research in Engineering Design,
vol.10:pp.189–209.
Control Architecture Modeling using Functional Energetic Method - Demonstration on a Hybrid Electric Vehicle
53