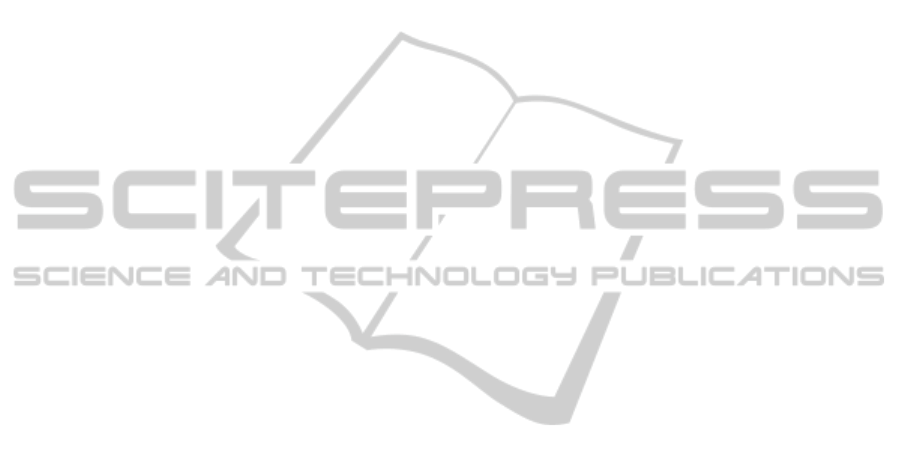
control, which is mainly caused by the nonlinear
optimization and on-line model identifications, the
disturbance model predictive control (Muske and
Badgwell, 2002) is introduced for SOFC (Pan and
Shen, 2012). It has less computing load and can deal
with some nonlinearity and uncertainty
characteristics. But it is non-adaptive and cannot
guarantee the closed-loop stability while achieving a
fast disturbance-rejection.
In this paper, we try to introduce another
advanced control approach, L
1
adaptive control, for
designing the SOFC control system. L
1
adaptive
control offers its own set of attractive features,
including fast and robust adaptation. In addition to
the conventional asymptotic performance
characterization, L
1
adaptive control permits
transient analysis for both control signal and system
response. Furthermore, this methodology has been
extended to systems with unknown time-varying
parameters (Cao and Hovakimyan, 2007), to systems
with nonlinear uncertainties (Cao and Hovakimyan,
2008), to systems with un-modeled internal and
actuator dynamics (Cao and Hovakimyan, 2008), to
systems in the presence of non-zero trajectory
initialization error (Cao and Hovakimyan, 2008),
and to a certain output feedback framework (Cao
and Hovakimyan, 2009). L
1
adaptive control has
been very successfully applied in unmanned flight
controls which have nonlinearities, time-varying
disturbances, unknown parameters and un-modeled
dynamics.
An extension approach of the L
1
adaptive output
feedback control (Cao and Hovakimyan, 2009) to
systems of unknown relative degree may deal well
with the control problems of SOFC, e.g., time-
varying uncertainties with unknown rate of
variations caused by load disturbances. Compared to
other L
1
adaptive control methods, this approach
adopts a new piece-wise continuous adaptive law
along with the low-pass filtered control signal. It
allows for achieving arbitrarily close tracking of the
reference signals, and the transfer function of its
reference system is not required to be strictly
positive real (SPR). Stability of this system is
guaranteed by its design via small-gain type
argument. These features show that this L
1
adaptive
control approach may have great potential to be
applied in wide industrial processes.
In this paper, we reproduce a SOFC simulation
model as the plant; then take advantage of its
nominal working conditions to design a L
1
adaptive
output feedback controller. Through the analysis on
the controller framework, the operating constraints
are set to the proper position in the loop. It holds the
closed-loop stability in the presence of the hard
constraints. Simulations comparing to a linear
disturbance model predictive controller (DMPC) on
the SOFC model show that L
1
adaptive control has
better disturbance-rejection performance and much
faster temporary regulating-process on the SOFC
constant voltage.
The paper is organized as follows. Section 2
describes the dynamic SOFC model. In Section 3, L
1
adaptive output feedback controller with operating
constraints is designed. For making an evaluation on
the new controller, a linear DMPC controller is
designed in Section 4. The simulation results along
with some discussions on these two SOFC control
methods are presented in Section 5. Section 6
concludes the paper.
2 DYNAMIC MODEL OF SOFC
Many nonlinear dynamic models of SOFC with
detailed descriptions on cell internal processes are
too complicated to support a controller designing
process. The model reported in the paper (Padullés
and Ault, 2000) describes the key characteristics of
the SOFC dynamic process in the Laplace transform
domain. It shows challenging control problems
owing to SOFC’s nonlinear dynamics, tight
operating constraints and unexpected disturbances. It
has been taken as a benchmark commonly studied in
the SOFC control literature (Huo et al., 2008; Wu et
al., 2008; Yang et al., 2009). Therefore, this model
will be adopted as the SOFC plant for the L
1
adaptive
controller design. Some preconditions (Padullés and
Ault, 2000) are stated in the following: The gases
are ideal; The stack is fed with hydrogen and air;
The flow ratio of hydrogen to oxygen is kept at
1.145; Lump gas pressures are considered in the
channels along the electrodes; The temperature is
stable; The exhaust of each channel is via a single
orifice, and the ratio of pressures between the
interior and exterior of the channel is large enough
to consider that the orifice is choked; The Nernst
equation can be applied. This dynamic SOFC model
consists of the fuel processor and the fuel cell stack,
as shown in Fig. 1, where E denotes the stack output
voltage (V), q
f
the natural gas flow rate (mol/ s), and
I the external current load (A); p
H2
, p
O2
, and p
H2O
denote the partial pressures (Pa) of hydrogen,
oxygen, and water, respectively; q
H2,in
and q
O2,in
are
the input flow rates of hydrogen and oxygen (mol/s),
respectively. The model is described in the
following and all the parameters are annotated in
Table 1.
ICINCO2014-11thInternationalConferenceonInformaticsinControl,AutomationandRobotics
500