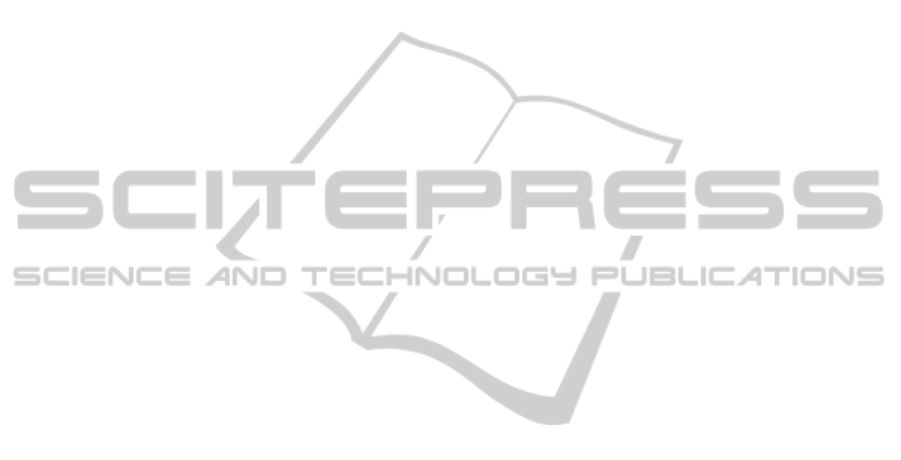
comprise a massive amount of car functionalities. An
example is the engine control unit which includes up
to 300 software components. It deals with lots of sen-
sor signals and is highly interconnected with other
controllers. However, on such a centralized software
system, some integrated functionalities are highly in-
volved with each other and are not suitable for fur-
ther relocation. Inter core communication will cause a
lot of overhead between cores or even between ECUs
if higher synchronization mechanisms have to han-
dle data exchange between every component. Be-
cause applications shall be shared individually be-
tween ECUs and cores this scenario could be an ori-
gin to fulfill the postulated requirements of a future
domain controller.
3.3 A standardized middleware for
domain controllers
Based on a technical side of view, every migrated sin-
gle core software project and their software compo-
nents run encapsulated on each core. Thus, the ap-
propriate Run Time Environment Layer (abbr. RTE)
must be located independently on every core, as well.
In practice, the upcoming bottlenecks are hardware
resources (e.g. memory and communication con-
trollers in all kinds), which have to be allocated si-
multaneously. These resources shall be under control
of centralized basic software modules, like the operat-
ing system, which handles each access. According to
the ISO Standard 26262 (International Organization
for Standardization, 2011), for safety-relevant vehicle
applications, which are specified with an ASIL, there
must be arrangements made to avoid any interference
caused by other components during runtime. The ap-
proach to run single core applications shared individ-
ually on multi-core core systems is covered from the
AUTOSAR 4.0 standard and is already included in its
basic software.
The AUTOSAR Operating System (abbr. OS) is
enriched by the new IOC (Inter-OS-Application Com-
munication), which allows information exchange be-
tween OS-Applications (AUTOSAR, 2011). There-
fore all information is passed through by the IOC (see
fig. 4). For software components, running on applica-
tion layer level, this module is not directly accessible
and is decoupled by the RTE (AUTOSAR Adminis-
tration, 2011). If information transfer between soft-
ware components shared on several cores is needed,
this feature is a possible approach for it. As proposed
in (Scheidemann et al., 2010a), (Scheidemann et al.,
2010b), the IOC enables the communication chan-
nel between separated memory partitions, surround-
ing software component groups which assure freedom
from interference related on memory faults. Thus, if
the MPU or MMU is configured correctly, software
components cannot modify memory of another par-
tition. Considering a multi-core scenario, the IOC
facilitates communication over core borders. How-
ever these mechanisms have an influence on the whole
system performance and availability. Especially for
safety-relevant functions, mixed integrated on a mul-
ticore controller with hard timing constraints, provi-
sions like appropriate scheduling algorithms have to
be arranged at software integration phase (Schmidt
et al., 2012), in order to guarantee the predicted ex-
ecution time of each software component.
4 CONCLUSION AND FUTURE
WORK
In the future, Tier-2 and also Tier-1 suppliers will
mainly supply and develop multi-core platforms for
OEMs. Car manufactures are confronted with the ac-
tual hardware controller designs and have to deal with
the problem to parallelize their software and to re-
duce complexity. More and more software compo-
nents must be integrated on less automotive ECUs.
If that assumption applies, large scale software inte-
gration techniques could be the enabler for upcom-
ing automotive E/E software architectures. As men-
tioned before, these approaches will come along with
multi-core hardware platforms, derived from con-
sumer electronics.
This paper proposes a domain controlled archi-
tecture in order to exhibit a possible approach for
future vehicle electrical systems. Furthermore, it is
demonstrated that there is a need for further research,
to transfer multi-core technologies to the automotive
industry, by using the examples of consumer elec-
tronics. Nevertheless, considering the different sys-
tem and safety requirements inflicted on mobility do-
mains, typical software parallelization scenarios, as
used for personal computer software, are not entirely
suitable. In this context, the national research project
ARAMiS aims at enabling multi-core systems for au-
tomotive, railway and avionic domain, to smooth the
way for Cyber Phyical Systems (Geisberger and Broy,
2012) in the future.
ACKNOWLEDGEMENTS
This work was funded within the project ARAMiS by
the German Federal Ministry for Education and Re-
search with the funding ID 01IS11035.