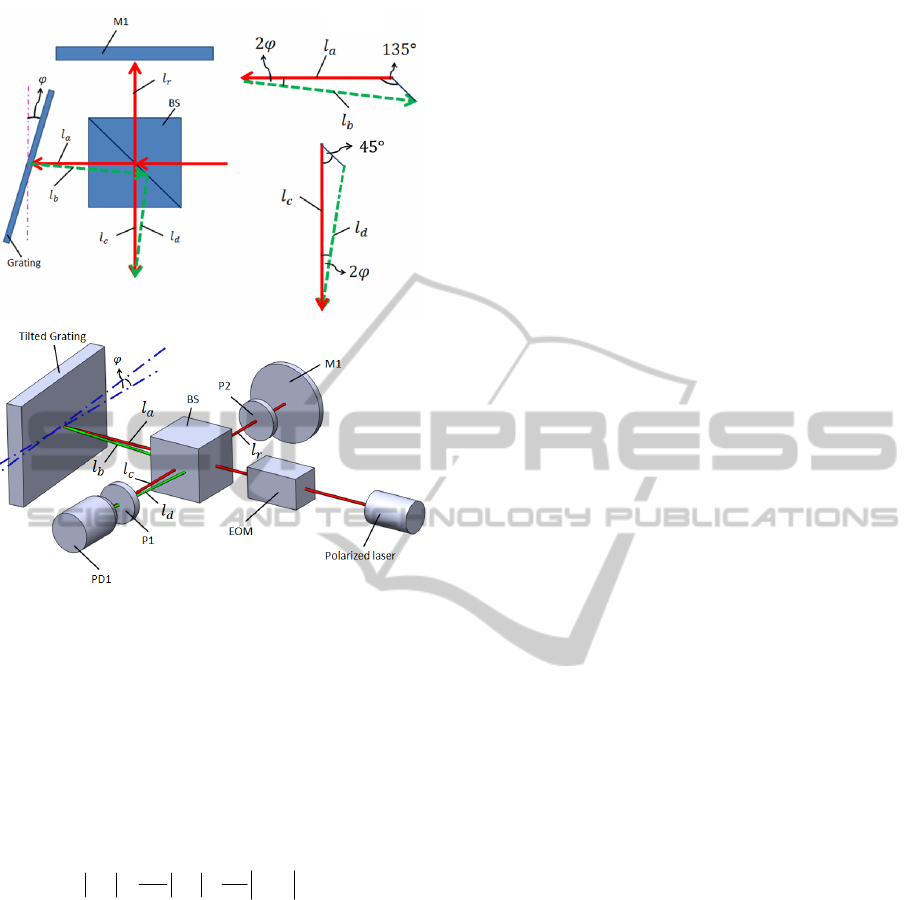
Figure 7: The Error Effect of Michelson Interferometry: (a)
the top view of the error configuration, (b) the overall
error configuration
frequency and polarization Moreover, non-
uniformity is caused by utilizing a grating with
irregular grating pitch or the thermal variation in
grating interferometry. The performance of our
proposed system is influenced by these factors. The
theoretical displacement error |Δe
t
| in the proposed
interferometer is given by the following expression:
44
g
tg
e
(22)
where |ΔΛ| is the uncertainty of grating pitch and
|ΔΦ
g
| is the phase uncertainty mainly caused by
frequency mixing and polarization mixing errors.
According to the characteristic of the experimental
setup, the total error |Δe
t
| caused by non-linearity
and non-uniformity is about 1.628 nm.
5 CONCLUSIONS
In this research, we proposed a heterodyne
interferometer for measuring 2D (in-plane and out-
of-plane) displacement. Once a heterodyne light
beam normally passes through a semi-transmission
diffraction grating, the system is divided into two
detection parts, reflection part (Michelson
interferometry) and diffraction part (Grating
interferometry). The experimental results show that
the system has ability to provide precise in-plane
and out-of-plane displacement information without
changing its optical arrangement. Straightness tests
in 2D are also conducted to prove the system
feasibility. Moreover, the error analysis reveals that
the dominant errors are mainly caused by the
misalignment of the yaw angle, the errors arising
from non-linearity of heterodyne modulating
technique and the non-uniformity of grating pitch.
Therefore, the measurement resolution and range
can achieve to nanometric and millimetric levels.
ACKNOWLEDGEMENTS
The authors cordially thank the NTUST Opto-
Mechatronics Technology Center for their useful
help. This study was supported by the National
Science Council, Taiwan, under contract NSC-101-
2218-E-011-033.
REFERENCES
Zajtchuk R., 1999. “New technologies in medicine:
biotechnology and nanotechnology” Disease a-Month,
Volume 45, Issue 11, PP453-495.
B, Yu, M. Meyyappan, 2006 “Nanotechnology: Role in
emerging nanoelectronics” Solid-State Electronics,
Volume 50, Issue 4, PP536-544.
G. Lérondel, A. Sinno, L. Chassagne, S. Blaize, P. Ruaux,
A. Bruyant, S. Topçu, P. Royer, Y. Alayli, 2009
“Enlarged near-field optical imaging” Applied
Physics, Volume 106, Issue 4, PP 044913 - 044913-4.
J. Zhao, M. Kunieda, G. Yang, X. Yuan, 2010 “The
Application of Nanotechnology for Mechanical
Manufacturing,” Key Engineering Materials, Volumes
447 – 448, PP86-90.
L. Thillya, S. Petegemb, P. Renaulta, F. Lecouturierc, V.
Vidald, B. Schmittb, H. Swygenhovenb, 2009 “A new
criterion for elasto-plastictransition in nanomaterials:
Application to size and composite effects on Cu–
Nbnanocompositewires,” Acta Materialia, Volume 57,
Issue 11, PP3157–3169.
J. Li, Y. Lu, M. M, 2006 “Nano Chemical Sensors with
Polymer-Coated Carbon Nanotubes,” IEEE Sensors
Journal, Volume 6, Issue 5, PP 1047-1051.
H. L. Hsieh, 2011 “Novel interferometric stage based on
quasi-common-optical-path configuration for large
scale displacement,” doctoral thesis.
G. R. Witt, 1974 “Thin solid film,” Thin Solid Films
Volume 22, Issue 2, pp133–156.
H. Miyajima, E. Yamamoto, K. Yanagisawa,
(b)
(a)
HeterodyneInterferometerforIn-planeandOut-of-planeDisplacementMeasurements
61