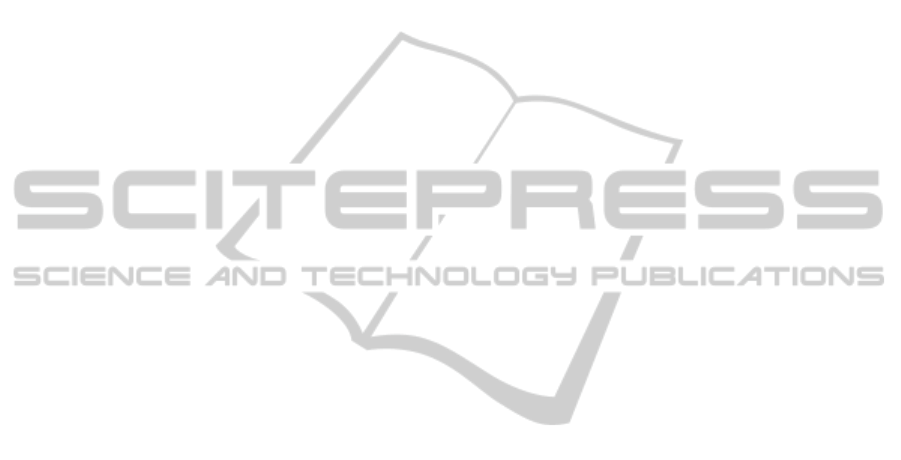
interviews. The model should be considered as a
start point when defining a design process for an
enterprise. The process is intended to be fitted and
specified for the needs of a particular organization.
This research has revealed that applying
optimizing design for pulp and paper facilities not
only requires development of optimization methods
and tools but also changes in the business processes
of design organizations and also customers. An
enterprise offering collaborative optimizing design
can’t compete with traditional design enterprises, if
the customer is not aware of the different approach
with different time and budget requirements.
Therefore, the design organization has to be able to
convince the customer that optimizing design will
benefit the project.
One great challenge is the trustworthiness of the
models. In order to convince the customer to invest
in a separate optimization project or to allow longer
and more expensive conceptual phase, the models
have to match with experiential data. The optimizing
design has the greatest potential, when the solution
is outside the conventional solution area. Therefore
the models should be proved to be valid also when
extrapolated outside the area where the data for the
model has been gathered.
ACKNOWLEDGEMENTS
This research was supported by Forestcluster Ltd
and its Effnet program. Other research partners in
the research project were from Tampere University
of Technology, University of Eastern Finland,
University of Jyväskylä and VTT Technical
Research Center of Finland.
REFERENCES
Bañares-Alcántara, R., King, J.M.P., 1996. Design support
systems for process engineering—III. Design rationale
as a requirement for effective support. Computers &
Chemical Engineering 21, 263–276.
Blanco, A., Dahlquist, E., Kappen, J., Manninen, J.,
Negro, C., Ritala, R., 2009. Use of modelling and
simulation in the pulp and paper industry.
Mathematical and Computer Modelling of Dynamical
Systems 15, 409–423.
Bogusch, R., Marquardt, W., 1997. A formal
representation of process model equations. Computers
& Chemical Engineering 21, 1105–1115.
Catledge, L. D., Potts, C., 1996. Collaboration during
conceptual design. IEEE Comput. Soc. Press, pp. 182–
189.
Dahlquist, E., 2008. Use of modeling and simulation in
pulp and paper industry. EU COST and Malardalen
University Press, Sverige.
Davenport, Thomas; Short James, 1990. The new
industrial engineering : information technology and
business process redesign. Massachusetts Institute of
Technology.
Eichfelder, G., 2010. Multiobjective bilevel optimization.
Mathematical Programming 123, 419–449.
Hämäläinen, J., Miettinen, K., Madetoja, E., Mäkelä, M. M.,
Tarvainen, P., 2004. Multiobjective decision making for
papermaking. CD-Rom Proceedings of MCDM.
Kahrs, O., Marquardt, W., 2007. The validity domain of
hybrid models and its application in process
optimization. Chemical Engineering and Processing:
Process Intensification 46, 1054–1066.
Kettinger, W. J., Grover, V., 1995. Special section: toward
a theory of business process change management.
J. Manage. Inf. Syst. 12, 9–30.
Kettinger, W.J., Teng, J.T.C., Guha, S., 1997. Business
Process Change: A Study of Methodologies,
Techniques, and Tools. MIS Quarterly 21, 55–80.
Linnala, 2010. Dynamic simulation and optimization of an
SC papermaking line - illustrated with case studies.
Nordic Pulp and Paper Research Journal 25, 213–220.
Marquardt, W., Nagl, M., 2004. Workflow and
information centered support of design processes—the
IMPROVE perspective. Computers & Chemical
Engineering 29, 65–82.
Pajula, E., 2006. Studies on Computer Aided Process and
Equipment Design in Process Industry. Helsinki
University of Technology.
Ropponen, A., Ritala, R., 2012. Operational Optimization
of Flow Management in Papermaking. Presented at
the Papercon 2012, New Orleans, USA.
Ropponen, A., Ritala, R., Pistikopoulos, E.N., 2011.
Optimization issues of the broke management system
in papermaking. Computers and Chemical
Engineering 35, 2510–2520.
Schein, E., 1998. Process Consultation Revisited: Building
the Helping Relationship. Prentice Hall.
Seuranen, T., Pajula, E., Hurme, M., 2001. Applying CBR
and Object Database Techniques in Chemical Process
Design, in: Aha, D., Watson, I. (Eds.), Case-Based
Reasoning Research and Development, Lecture Notes
in Computer Science. Springer Berlin / Heidelberg, pp.
731–743.
Strömman, M., Seilonen, I., Peltola, J., Koskinen, K.,
2011. Design process model for optimizing design of
continuous production processes, in: SIMULTECH
2011 - Proceedings of 1st International Conference on
Simulation and Modeling Methodologies,
Technologies and Applications. pp. 492–501.
Theissen, M., Hai, R., Marquardt, W., 2008. Design
Process Modeling in Chemical Engineering. Journal of
Computing and Information Science in Engineering 8,
011007.
Theißen, M., Hai, R., Marquardt, W., 2011. A framework
for work process modeling in the chemical industries.
Computers & Chemical Engineering 35, 679–691.
SIMULTECH2012-2ndInternationalConferenceonSimulationandModelingMethodologies,Technologiesand
Applications
478