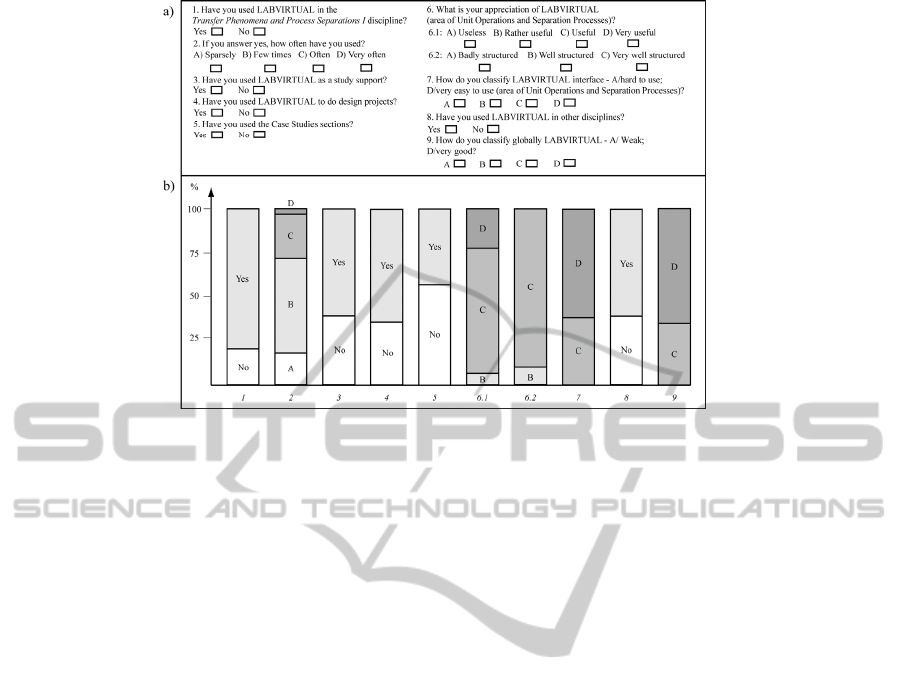
Figure 6: LABVIRTUAL assessment: a) enquiry; b) enquiry’s results (A- bad, D- very good).
ACKNOWLEDGEMENTS
The authors wish to acknowledge the receipt of
financial support from POSC, Portugal, contract
743/4.2/C/REG, which enabled the development of
the platform partially described here.
REFERENCES
Bell, J. T. and Fogler, H. S., 1998. The application of
virtual reality to chemical engineering and education.
In Proc. AIChE Annual Meeting, Miami, USA, session
170.
Edgar, T.F., 2006. Enhancing the undergraduate
computing experience. Chemical Engineering
Education, 40 (3) 231─238.
Felder, R.M., 2006. Teaching engineering in the 21st
century with a 12th-century teaching model: how
bright is that?. Chemical Engineering Education, 40
(2) 110─113.
Garcia-Herreros, P. and Gómez, J. M., 2010. Modeling
and optimization of a crude distillation unit: a case
study for undergraduate students. Comp. Appl. Eng.
Ed., DOI: 10.1002/cae.20469.
Granjo, J. F., Rasteiro, M. G., Gando-Ferreira, L. M.,
Bernardo, F. P., Carvalho, M. G., Ferreira, A. G.,
2009. A virtual platform to teach separation Processes.
Computer Appl. in Eng. Ed., DOI 10.1002/cae.20383.
Hasna, A.M., 2010. E-competence in chemical
engineering learning and teaching. In Proc. ICETC
2010 - 2nd. Int. Conf. Ed. Tech. and Computers,
China, art. no. 5529669, V4330-V4336.
Henry, J., 2005. Real laboratories at a distance. In Proc.
AIChE annual meeting, Cincinnati, USA, 3640.
Henry, J., Miletic, M., DiBiasio, D., Clark, W., 2008.
Varieties of ways for learning about distillation. In
Proc. ASEE annual meeting, Pittsburg, USA.
Poling, B. E., Prausnitz, J. M., O'Connell, J. P., 2001.
Properties of Gases and Liquids. McGraw-Hill, N. Y.,
5
th
edition.
Rasteiro, M. G., Ferreira, L. M., Teixeira, J. C., Bernardo,
F. P., Carvalho, M. G., Ferreira, A. G., Ferreira, R. Q.,
Garcia, F. P., Baptista, C. G., Oliveira, N. M., Quina,
M. M., Santos, L. O., Saraiva, P. A., Mendes, A. M.,
Magalhães, F. M., Almeida, A. S., Granjo, J. F.
Ascenso, M., Bastos, R. M., Borges, R., 2009.
LABVIRTUAL – a virtual platform to teach chemical
processes. Education for Chemical Engineers, 4 (1)
e9─19.
Seader, J. D. and Henley, E. J., 2006. Separation Process
Principles. John Wiley & Sons, Hoboken, NJ, 2
nd
edition.
Shacham, M., Cutlip, M. Brauner, N., 2009. From
numerical problem solving to model-based
experimentation – incorporating computer based tools
of various scales into the ChE curriculum, Chem. Eng.
Ed., 43 (4).
Streicher, S. J., West, K., Fraser, D. M., Case, J. M.,
Linder, C., 2005. Learning through simulation ─
student engagement, Chem. Eng. Ed., 39 (4),
288─301.
Wankat, P. C., 2007. Separation Process Engineering.
Prentice-Hall, Upper Saddle River, NJ, 2
nd
edition.
CSEDU2012-4thInternationalConferenceonComputerSupportedEducation
240