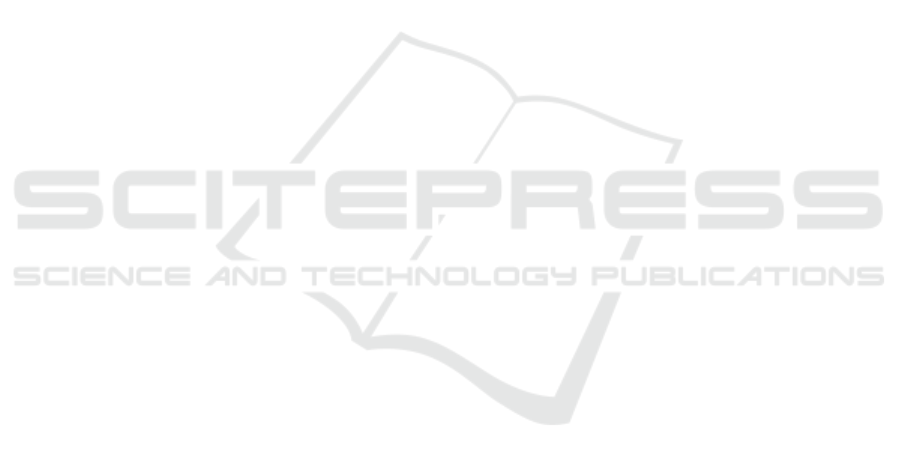
SELECTIVELY BONDED POLYMERIC CHECK VALVE FOR
THE RELIABLE REGULATION OF INTRAOCULAR PRESSURE
Seongmin Im, Byungphil Mun, Jaeyong An, Jongchan Choi
School of Mechatronics, Gwangju Institute of Science and Technology, Gwangju, Korea
Sung Yang
1,2,3
, Jonghyun Lee
1,2,3
1
School of Mechatronics,
2
Graduate Program of Medical System Engineering
3
Department of Nanobio Materials and Electronics, Gwangju Institute of Science and Technology, Gwangju, Korea
Keywords: Glaucoma drainage device, Polymer, Check Valve, Selectively bonding, Intraocular Pressure, FEA, MEMS.
Abstract: A glaucoma drainage device for the regulation of intraocular pressure is presented. The device consists of
three biocompatible polymer layers: the cover (top layer), the diaphragm (intermediate layer), and the
baseplate with a cannular (bottom layer). Finite element analyses (FEA) were performed to find optimal
design parameters for the targeted cracking pressure: the diameter of orifice, the thickness of intermediate
layer, the width of the channel, and the overlapped length of the orifice over valve seat. Top and bottom
layers were made by polydimethylsiloxane (PDMS) replica molding process, and an intermediate thin layer
with through-holes was fabricated by PDMS fill-in molding method and hydrophobic treatment. The
overlapped area of the bottom layer was coated with Cr and Au by using PDMS as a shadow mask. Metal
layers are not to be bonded between the bottom and the intermediate layers so that the device showed the
enhanced reliability in operation and the higher yield in production. Oxygen plasma treatment was
performed for irreversible bonds between separate three PDMS layers. The experimental cracking pressure
of the fabricated valve was 2.50 kPa, which is very close to the target value (2.67 kPa). The experiments
showed that the proposed polymer check valve can regulate the pressure of the aqueous humour, fluid in an
anterior chamber, within the normal intraocular pressure range (15~20mmHg) with a high repeatability.
1 INTRODUCTION
In microfluidic systems, valves are one of the most
important components to control the flow of the
systems. One of the most important characteristics
of microvalves is reliability, and high reliability
makes microfluidic systems successful. Check
valves are passive microvalves which allow
unidirectional flow. In micro check valve, reliability
can be defined as the consistency of cracking
pressure, flow rate, and diode-like characteristic.
Check valves can be used for flow regulation, on/off
switch, and sealing of liquid/gas/vacuum (Kwang W
Oh et al., 2006). Glaucoma drainage devices and
drug delivery are representative applications of
micro check valve for bionics. Currently, the reliable
fabrication and operation are the key issues in the
micro check valve (Ronalee Lo et al., 2009).
Though prior micro check valves have several
advantages: simple fabrication, polymer and cheap,
there is a stiction problem in the bonding process of
polymer layers (Nooli Jeon et al.,2002). To detach
the overlapped area between valve seat and valve
orifice, air or water should be introduced quickly
during bonding process before polymer layers are
irreversibly bonded. If the overlapped area is not
completely detached, cracking pressure and flow
rate of the fabricated device will vary seriously
during operation as shown in Fig. 1.
Glaucoma is the second leading cause of
blindness in the world, and it is estimated that 66.8
million people are suffering from glaucoma
(Quigley HA., 1996). Glaucoma is theoretically
defined as a progressive optic neuropathy as a result
of elevation of intraocular pressure (IOP) above the
physiological level of individuals (Shiose Y.,1990).
Glaucoma drainage devices (GDDs) have the
potential to regulate flow reliably and to maintain
IOP below 20mmHg.
234
Im S., An J., Choi J., Mun B., Yang S. and Lee J..
SELECTIVELY BONDED POLYMERIC CHECK VALVE FOR THE RELIABLE REGULATION OF INTRAOCULAR PRESSURE.
DOI: 10.5220/0003167302340237
In Proceedings of the International Conference on Biomedical Electronics and Devices (BIODEVICES-2011), pages 234-237
ISBN: 978-989-8425-37-9
Copyright
c
2011 SCITEPRESS (Science and Technology Publications, Lda.)