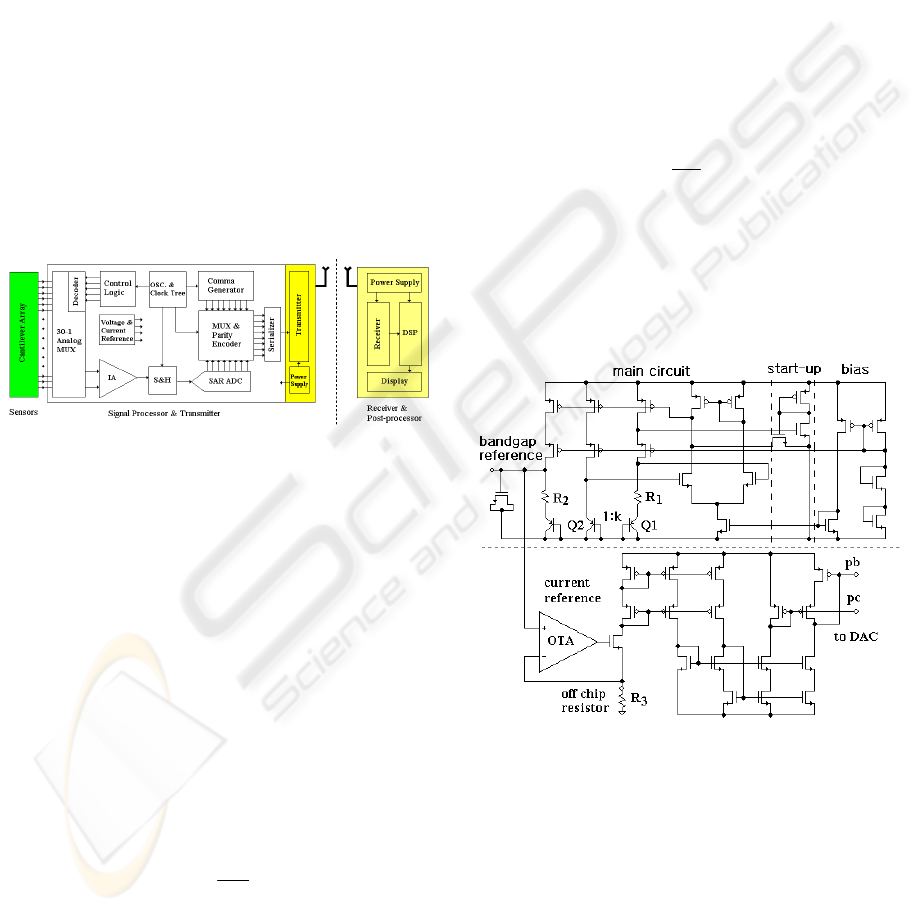
their functions. The first part is the sensor array.
There are 30 strain-sensing micro-cantilevers
distributed evenly on the two sides of the biomedical
instrument top plate. The Wheatstone bridge
configured sensors convert the physical strain to a
resistance change and then to voltage signal under
DC excitation. The middle part shown in figure 2
includes two chips, one chip for signal processing
and another one for signal transmitting. The signal-
processing chip amplifies the signal coming from the
sensors and digitizes the analog signal to digital
domain. The transmitter chip sends out the signal
using ASK modulation with 335MHz carrier
frequency. The receiver part receives and recovers
the data remotely. Furthermore, the data will be
post-processed by software and shown graphically
on the display.
In this paper, the scope mainly focuses on the
design and implementation of the signal processing
integrated circuit.
Figure 2: Sensor array signal processing system block
diagram.
3 CIRCUIT IMPLEMENTATION
Instrumentation Amplifier. The Instrumentation
Amplifier (IA) amplifies the difference signal
between the two input terminals and rejects the
common mode signals on both inputs (Kitchin and
Counts, 2000). Unlike normal opamp, the feedback
of IA uses an internal resistance network but the
gain is set by an external resistor.
The external gain setting resistor provides
maximum design flexibility for the system designer
to accommodate the input signal level. The gain can
be set using the following equation
g
V
R
R
A
2
1+=
(1)
where, R is internal resistor and R
g
is off chip gain
setting resistor.
A classical 3 opamps configuration is chosen and
an additional opamp provides variable output DC
level to accommodate the following stage circuit.
Voltage and Current Reference. Both the ADC
and the DAC in the system need either the voltage or
the current reference. Bandgap voltage reference is
selected for its extraordinary performance of
process, power supply and temperature variation
independence (Meyer and Gray, 1993, Brokaw,
1974). The reference is generated by adding a
negative temperature coefficient (TC) voltage and a
weighted positive TC voltage. Hence, a zero TC can
be achieved by adjusting the value of R2 and R1
based on the following equation
kV
R
R
VV
TbeBG
ln
1
2
+=
(2)
where, V
be
is the base-emitter junction voltage, V
T
is
thermal voltage and k is the geometry ratio of Q1
and Q2. The bandgap reference circuit shown in
figure 3 has two operation points. To guarantee the
circuit always works at the right point, a startup
circuit is also included.
Figure 3: Voltage and Current Reference Schematic.
The current reference for the current-steering
DAC cannot be fully generated on-chip due to the
lack of a high precision absolute value resistor. With
the aid of a low TC and high precision external
resistor, and the bandgap voltage reference, an
accurate current reference can be obtained. The
current reference circuit is shown in the lower part
of figure 3.
DESIGN OF ANALOG SIGNAL PROCESSING INTEGRATED CIRCUIT FOR MULTI-CHANNEL BIOMEDICAL
STRAIN MEASUREMENT INSTRUMENT
257