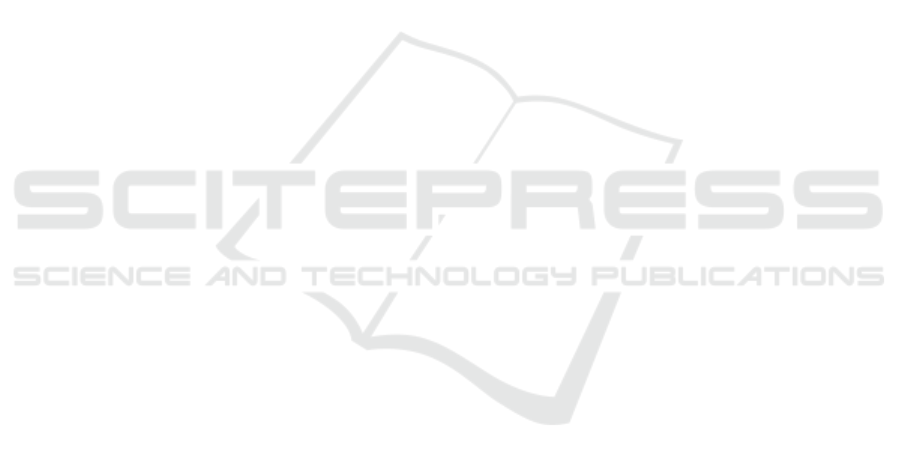
front-end deformation and the rotation of the vehicle;
first around the point of impact and then around the
failure of the material due to welding or heat treat-
ment. The LPM employs Lagrangian formulation to
define the equations of motion and is presented in po-
lar coordinates to simplify the system. The model cor-
relates well with the FE data for a 2010 Toyota Yaris;
the deformation, velocity and pitching angle are pre-
dicted well for a full frontal impact at 56 kmph. The
failure of the structural members is simulated in the
model with a torsional spring. The angle of rotation
of the vehicle θ
2
due to material behavioural changes
is close to the maximum values in the validation data.
The novel methodology presented in this study
can be further enhanced with real-time weld fracture
data from physical tests. The model predictability can
be further improved by replacing the piece-wise linear
approximation for the vehicle parameter values with
non-linear functions for stiffness and damping coeffi-
cients.
ACKNOWLEDGEMENTS
The authors would like to thank Top Research Center
Mechatronics (TRCM) at University of Agder for the
support to conduct the research. We would also like
to acknowledge the support of NHTSA and NCAC for
the FE models used in this study.
REFERENCES
Amirthalingam, M., Hermans, M., and Richardson, I.
(2009). Microstructural development during weld-
ing of siliconand aluminum-based transformation-
induced plasticity steels-inclusion and elemental par-
titioning analysis. Metallurgical and Materials Trans-
actions A: Physical Metallurgy and Materials Sci-
ence, 40(4):901–909.
Benson, D., Hallquist, J., Igarashi, M., Shimomaki, K., and
Mizuno, M. (1986). Application of DYNA3D in large
scale crashworthiness calculations.
B
¨
ottcher, C. S., Frik, S., and Gosolits, B. (2005). 20 years of
crash simulation at Opel-experiences for future chal-
lenges. 4th LS-DYNA Anwenderforum, pages 79–86.
Chang, J. M., Ali, M., Craig, R., Tyan, T., El-Bkaily, M.,
and Cheng, J. (2006a). Important modeling practices
in CAE simulation for vehicle pitch and drop. In SAE
Technical Papers. SAE International.
Chang, J. M., Huang, M., Tyan, T., Li, G., and Gu, L.
(2006b). Structural optimization for vehicle pitch and
drop. In SAE Technical Papers. SAE International.
Cyr
´
en, O. and Johansson, S. (2018). Modeling of Occupant
Kinematic Response in Pre-crash Maneuvers A sim-
plified human 3D-model for simulation of occupant
kinematics in maneuvers.
Elkady, M. and Elmarakbi, A. (2012). Modelling and anal-
ysis of vehicle crash system integrated with different
VDCS under high speed impacts. Central European
Journal of Engineering, 2(4):585–602.
Elkady, M., Elmarakbi, A., and Macintyre, J. (2012). En-
hancement of vehicle safety and improving vehicle
yaw behaviour due to offset collision using vehicle
dynamics. International Journal of Vehicle Safety,
6(2):110–133.
Goldstein, H., Poole, C., Safko, J., and Addison, S. R.
(2002). Classical Mechanics, 3rd ed. American Jour-
nal of Physics, 70(7):782–783.
Ionut, R. A., Corneliu, C., and Bogdan, T. (2017). Math-
ematical model validated by a crash test for study-
ing the occupant’s kinematics and dynamics in a cars’
frontal collision. International Journal of Automotive
Technology 2017 18:6, 18(6):1017–1025.
Kamal, M. M. (1970). Analysis and simulation of vehicle
to barrier impact. SAE Technical Papers, pages 1498–
1503.
Marzougui, D., Brown, D., Park, H. K., Kan, C. D., and
Opiela, K. S. (2011). 3 th International LS-DYNA
Users Conference Session: Automotive Development
& Validation of a Finite Element Model for a Mid-
Sized Passenger Sedan.
Mentzer, S. G., Radwan, R. A., and Hollowell, W. T. (1992).
The SISAME methodology for extraction of optimal
lumped parameter structural crash models. SAE Tech-
nical Papers.
NHTSA (2017). Crash simulation vehicle models.
Noorsumar, G., Robbersmyr, K., Rogovchenko, S., and
Vysochinskiy, D. (2020). Crash Response of a Re-
paired Vehicle - Influence of Welding UHSS Mem-
bers. In WCX SAE World Congress Experience. SAE
International.
Noorsumar, G., Rogovchenko, S., Robbersmyr, K., and
Vysochinskiy, D. (2021a). Mathematical models for
assessment of vehicle crashworthiness: a review. In-
ternational Journal of Crashworthiness.
Noorsumar, G., Rogovchenko, S., Robbersmyr, K.,
Vysochinskiy, D., and Klausen, A. (2021b). A novel
technique for modeling vehicle crash using lumped
parameter models. In Proceedings of the 11th In-
ternational Conference on Simulation and Modeling
Methodologies, Technologies and Applications, SI-
MULTECH 2021.
Noorsumar, G., Vysochinskiy, D., Englund, E., Rob-
bersmyr, K. G., and Rogovchenko, S. (2021c). Ef-
fect of welding and heat treatment on the properties
of UHSS used in automotive industry. EPJ Web of
Conferences, 250:05015.
Pavlov, N. (2019). Study the vehicle pitch motion by spring
inverted pendulum model. (February).
Pifko, A. and Winter, R. (1981). Theory and Application of
Finite Element Analysis To Structural Crash Simula-
tion, volume 13. Pergamon Press Ltd.
Savaresi, S., Poussot-Vassal, C., Spelta, C., Sename, O., and
SIMULTECH 2022 - 12th International Conference on Simulation and Modeling Methodologies, Technologies and Applications
110