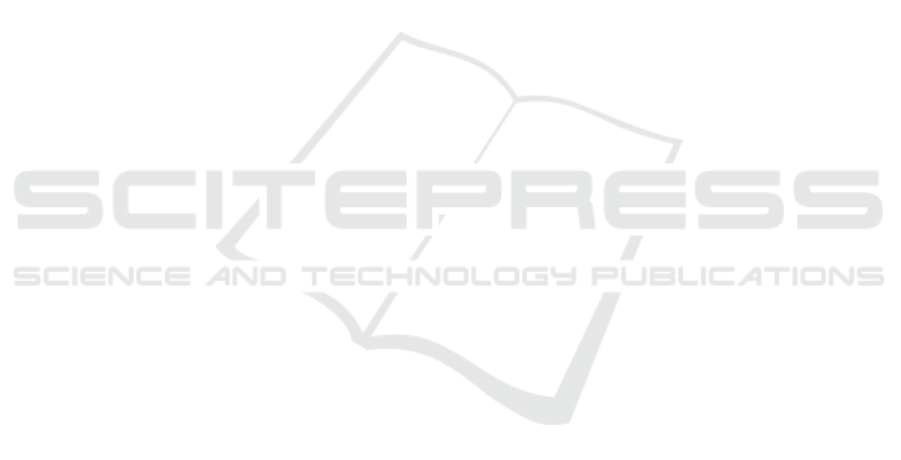
SONDE of the Federal Ministry of Education and Re-
search, Germany (Grant-No.: 13FH144PA8).
REFERENCES
Agora Energiewende and Guidehouse (2021). Making re-
newable hydrogen cost-competitive: Policy instru-
ments for supporting green H
2
.
Bahr, M., Gusak, A., Stypka, S., and Oberschachtsiek, B.
(2020). Artificial neural networks for aging simula-
tion of electrolysis stacks. Chemie Ingenieur Technik,
92(10):1610–1617.
Bro, R. and Kiers, H. A. (2003). A new efficient method
for determining the number of components in parafac
models. Journal of Chemometrics: A Journal of the
Chemometrics Society, 17(5):274–286.
Buttler, A. and Spliethoff, H. (2018). Current status of water
electrolysis for energy storage, grid balancing and sec-
tor coupling via power-to-gas and power-to-liquids: A
review. Renewable and Sustainable Energy Reviews,
82:2440–2454.
Christoph Edler (2018). Untersuchung der Einsatz-
moeglichkeiten von Hochleistungselektrolyseuren
fuer Netzdienstleistungen. diploma thesis, TU Wien,
https://repositum.tuwien.at/handle/20.500.12708/
7708.
Cihlar, J., Villar Lejarreta, A., Wang, A., Melgar, F., Jens,
J., and Rio, P. (2020). Hydrogen generation in eu-
rope: Overview of costs and key benefits. Luxem-
bourg. Publications Office of the European Union.
Enapter (2022). The AEM Multicore: Lowest-Cost Flexible
Hydrogen at Megawatt-Scale. https://www.enapter.
com/aem-multicore, Accessed: 28.02.2022.
Espinosa-L
´
opez, M., Darras, C., Poggi, P., Glises, R., Bau-
cour, P., Rakotondrainibe, A., Besse, S., and Serre-
Combe, P. (2018). Modelling and experimental val-
idation of a 46 kW PEM high pressure water elec-
trolyzer. Renewable Energy, 119:160–173.
Frensch, S. H., Fouda-Onana, F., Serre, G., Thoby, D.,
Araya, S. S., and Kær, S. K. (2019). Influence of
the operation mode on PEM water electrolysis degra-
dation. International Journal of Hydrogen Energy,
44(57):29889–29898.
Geitmann, S. (2022). HZwei - Das Magazin f
¨
ur Wasser-
stoff und Brennstoffzellen. Hydrogeit Verlag. Issue 1,
January 2022.
Green Hydrogen Systems (2022). HyProvide™: A-Series.
https://greenhydrogensystems.com/wp-content/
uploads/2021/02/A-Series-brochure-120421.pdf,
Accessed: 28.02.2022.
H-TEC SYSTEMS GmbH (2022). H-
TEC PEM-Elektrolyseur ME450/1400.
https://www.h-tec.com/produkte/detail/
h-tec-pem-elektrolyseur-me450-1400/me450-1400/,
Accessed: 17.03.2022.
Hornik, K., Stinchcombe, M., and White, H. (1989). Multi-
layer feedforward networks are universal approxima-
tors. Neural Networks, 2(5):359–366.
IRENA (2020). Green Hydrogen Cost Reduction: Scaling
up Electrolysers to Meet the 1.5
◦
C Climate Goal. In-
ternational Renewable Energy Agency. Abu Dhabi.
Kolda, T. G. (2006). Multilinear operators for higher-order
decompositions. Technical report, Citeseer.
Kopp, M., Coleman, D., Stiller, C., Scheffer, K., Aichinger,
J., and Scheppat, B. (2017). Energiepark Mainz:
Technical and economic analysis of the world-
wide largest Power-to-Gas plant with PEM electrol-
ysis. International Journal of Hydrogen Energy,
42(19):13311–13320.
Kosonen, A., Koponen, J., Huoman, K., Ahola, J., Ruuska-
nen, V., Ahonen, T., and Graf, T. (2016). Optimiza-
tion strategies of PEM electrolyser as part of solar
PV system. In 2016 18th European Conference on
Power Electronics and Applications (EPE’16 ECCE
Europe), pages 1–10. IEEE.
Kruppa, K. (2018). Multilinear Design of Decentralized
Controller Networks for Building Automation Sys-
tems. PhD thesis, HafenCity Universit
¨
at Hamburg.
Kruppa, K., Pangalos, G., and Lichtenberg, G. (2014). Mul-
tilinear approximation of nonlinear state space mod-
els. IFAC Proceedings Volumes, 47(3):9474–9479.
Lichtenberg, G., Pangalos, G., Cateriano Y
´
a
˜
nez, C., Luxa,
A., J
¨
ores, N., Schnelle, L., and Kaufmann, C. (2022).
Implicit multilinear modeling. at - Automatisierung-
stechnik, 70(1):13–30.
P. Ayivor, J. Torres, M.A.M.M. van der Meijden, R. van der
Pluijm, and B. Stouwie (2018). Modelling of large
size electrolyzer for electrical grid stability studies in
real time digital simulation. IEEE.
Pangalos, G., Eichler, A., and Lichtenberg, G. (2013). Ten-
sor systems - multilinear modeling and applications.
3rd International Conference on Simulation and Mod-
eling Methodologies, Technologies and Applications
(SIMULTECH-2013), pages 275–285.
Rakousky, C., Reimer, U., Wippermann, K., Kuhri, S.,
Carmo, M., Lueke, W., and Stolten, D. (2017). Poly-
mer electrolyte membrane water electrolysis: Re-
straining degradation in the presence of fluctuating
power. Journal of Power Sources, 342:38–47.
Schnelle, L., Lichtenberg, G., and Warnecke, C. (2022).
Using low-rank multilinear parameter identification
for anomaly detection of building systems. 11th
IFAC Symposium on Fault Detection, Supervision and
Safety for Technical Processes. Status: accepted.
The MathWorks, Inc. (2022). append - Group models
by appending their inputs and outputs. https://de.
mathworks.com/help/control/ref/lti.append.html, Ac-
cessed: 16.03.2022.
Zagorowska, M., Wu, O., Ottewill, J. R., Reble, M., and
Thornhill, N. F. (2020). A survey of models of degra-
dation for control applications. Annual Reviews in
Control, 50:150–173.
SIMULTECH 2022 - 12th International Conference on Simulation and Modeling Methodologies, Technologies and Applications
62