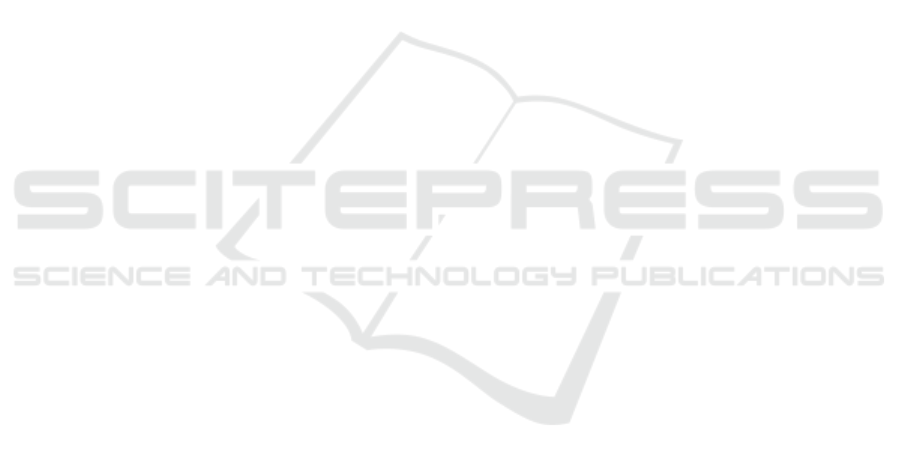
Chen, Z., Liao, H., and Zhang, X. (2014). Telecentric stereo
micro-vision system: Calibration method and experi-
ments. Optics and Lasers in Engineering, 57:82–92.
Halır, R. and Flusser, J. (1998). Numerically stable direct
least squares fitting of ellipses. In Proc. 6th Inter-
national Conference in Central Europe on Computer
Graphics and Visualization. WSCG, volume 98, pages
125–132. Citeseer.
Hartley, R. and Zisserman, A. (2003). Multiple view geom-
etry in computer vision. Cambridge university press.
Lee, T.-C., Kashyap, R. L., and Chu, C.-N. (1994). Build-
ing skeleton models via 3-d medial surface axis thin-
ning algorithms. CVGIP: Graphical Models and Im-
age Processing, 56(6):462–478.
Lei, S. and Zhang, S. (2009). Flexible 3-d shape mea-
surement using projector defocusing. Optics letters,
34(20):3080–3082.
Li, B. and Zhang, S. (2015). Flexible calibration method for
microscopic structured light system using telecentric
lens. Optics express, 23(20):25795–25803.
Li, B. and Zhang, S. (2017). Microscopic structured light
3d profilometry: Binary defocusing technique vs. si-
nusoidal fringe projection. Optics and Lasers in En-
gineering, 96:117–123.
Li, D., Liu, C., and Tian, J. (2014). Telecentric 3d profilom-
etry based on phase-shifting fringe projection. Optics
express, 22(26):31826–31835.
Liu, C., Chen, L., He, X., Thang, V. D., and Kofidis,
T. (2015). Coaxial projection profilometry based on
speckle and fringe projection. Optics Communica-
tions, 341:228–236.
Liu, H., Lin, H., and Yao, L. (2017). Calibration method for
projector-camera-based telecentric fringe projection
profilometry system. Optics express, 25(25):31492–
31508.
Pistellato, M., Bergamasco, F., Albarelli, A., Cosmo, L.,
Gasparetto, A., and Torsello, A. (2019a). Robust
phase unwrapping by probabilistic consensus. Optics
and Lasers in Engineering, 121:428–440. cited By 4.
Pistellato, M., Bergamasco, F., Albarelli, A., Cosmo, L.,
Gasparetto, A., and Torsello, A. (2019b). Stochas-
tic phase estimation and unwrapping. pages 200–209.
cited By 0.
Pistellato, M., Bergamasco, F., Albarelli, A., and Torsello,
A. (2015). Dynamic optimal path selection for 3d tri-
angulation with multiple cameras. Lecture Notes in
Computer Science (including subseries Lecture Notes
in Artificial Intelligence and Lecture Notes in Bioin-
formatics), 9279:468–479.
Pistellato, M., Bergamasco, F., Albarelli, A., and Torsello,
A. (2019c). Robust cylinder estimation in point clouds
from pairwise axes similarities. pages 640–647.
Pistellato, M., Cosmo, L., Bergamasco, F., Gasparetto, A.,
and Albarelli, A. (2018). Adaptive albedo compen-
sation for accurate phase-shift coding. volume 2018-
August, pages 2450–2455. cited By 3.
Rosendahl, S., H
¨
allstig, E., Gren, P., and Sj
¨
odahl, M.
(2010). Shape measurement with one fringe pattern
recording including a digital master. Applied Optics,
49(14):2622–2629.
Saeed, G. and Zhang, Y. (2007). Weld pool surface depth
measurement using a calibrated camera and struc-
tured light. Measurement Science and Technology,
18(8):2570.
Weckenmann, A., Peggs, G., and Hoffmann, J. (2006).
Probing systems for dimensional micro-and nano-
metrology. Measurement Science and Technology,
17(3):504.
Winkelbach, S. and Wahl, F. M. (2002). Shape from single
stripe pattern illumination. In Joint Pattern Recogni-
tion Symposium, pages 240–247. Springer.
Xu, J., Xi, N., Zhang, C., Shi, Q., and Gregory, J. (2011a).
Real-time 3d shape inspection system of automotive
parts based on structured light pattern. Optics & Laser
Technology, 43(1):1–8.
Xu, J., Xi, N., Zhang, C., Zhao, J., Gao, B., and Shi, Q.
(2011b). Rapid 3d surface profile measurement of in-
dustrial parts using two-level structured light patterns.
Optics and Lasers in Engineering, 49(7):907–914.
Yao, M. and Xu, B. (2007). Evaluating wrinkles on lami-
nated plastic sheets using 3d laser scanning. Measure-
ment Science and Technology, 18(12):3724.
Zhou, P., Zhu, J., Su, X., Jing, H., and Zhang, X. (2017).
Three-dimensional shape measurement using color
random binary encoding pattern projection. Optical
Engineering, 56(10):104102.
Zuo, C., Feng, S., Huang, L., Tao, T., Yin, W., and Chen,
Q. (2018). Phase shifting algorithms for fringe pro-
jection profilometry: A review. Optics and Lasers in
Engineering, 109:23–59.
ICPRAM 2022 - 11th International Conference on Pattern Recognition Applications and Methods
448