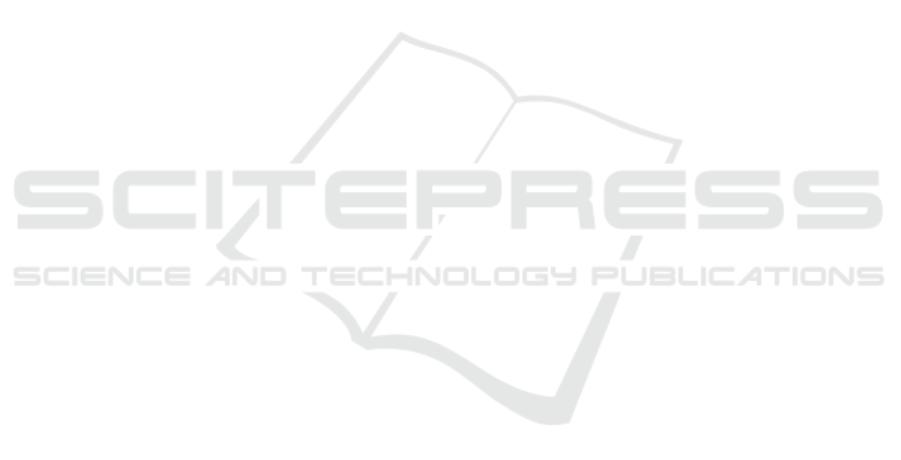
• The vehicle acceleration is assumed to be zero at
the time pitching starts in the crash event.
• Energy losses like friction and heat losses in the
vehicle during the crash event are neglected to
simplify the problem.
• Only vehicle rotations about the y-axis (pitching)
are considered for modeling in the full frontal im-
pact scenario; rotations about other axes are con-
sidered negligible and not impacting the occupant
injuries.
The next steps in this study include creating a
mathematical expression for the force components in
the mathematical model for the second phase which
includes pitching of the vehicle. The mathematical
expression for the force would help vehicle design
teams to reduce pitching on the vehicle by changing
the force components acting on the vehicle during a
collision. The prediction for maximum deformation
can be improved by using a non-linear force defor-
mation curve for the spring stiffness curve with larger
breakpoints along with including energy losses in the
model. The model currently uses standard spring and
damper coefficients for the suspension model which
can be tuned to match a particular vehicle being stud-
ied; also including the mass and the distance of the
CG from the vehicle suspension connections.
ACKNOWLEDGMENTS
The authors would like to thank University of Agder
for the support to conduct this research.
REFERENCES
Administration, N. H. T. S. et al. (2016). Crash sim-
ulation vehicle models. URL: https://www. nhtsa.
gov/research-data/databasesand-software.
B Munyazikwiye, B., Vysochinskiy, D., Khadyko, M., and
G Robbersmyr, K. (2018). Prediction of vehicle crash-
worthiness parameters using piecewise lumped pa-
rameters and finite element models. Designs, 2(4):43.
Benson, D., Hallquist, J., Igarashi, M., Shimomaki, K., and
Mizuno, M. (1986). Application of dyna3d in large
scale crashworthiness calculations. Technical report,
Lawrence Livermore National Lab.
Chang, J. M., Ali, M., Craig, R., Tyan, T., El-Bkaily, M.,
and Cheng, J. (2006). Important modeling practices in
cae simulation for vehicle pitch and drop. SAE Trans-
actions, pages 62–72.
Chang, J. M., Rahman, M., Ali, M., Tyan, T., El-Bkaily, M.,
and Cheng, J. (2005). Modeling and design for vehi-
cle pitch and drop of body-on-frame vehicles. SAE
transactions, pages 329–338.
Du Bois, P., Chou, C. C., Fileta, B. B., Khalil, T. B., King,
A. I., Mahmood, H. F., Mertz, H. J., Wismans, J.,
Prasad, P., and Belwafa, J. E. (2004). Vehicle crash-
worthiness and occupant protection.
Elkady, M. and Elmarakbi, A. (2012). Modelling and anal-
ysis of vehicle crash system integrated with different
vdcs under high speed impacts. Open Engineering,
2(4):585–602.
Elkady, M., Elmarakbi, A., and MacIntyre, J. (2012). En-
hancement of vehicle safety and improving vehicle
yaw behaviour due to offset collisions using vehicle
dynamics. International journal of vehicle safety,
6(2):110–133.
Goldstein, H., Poole, C., and Safko, J. (2002). Classical
mechanics.
Huang, M. (2002). Vehicle crash mechanics. CRC press.
Kamal, M. M. (1970). Analysis and simulation of vehicle to
barrier impact. SAE Transactions, pages 1498–1503.
Klausen, A., Tørdal, S. S., Karimi, H. R., Robbersmyr,
K. G., Je
ˇ
cmenica, M., and Melteig, O. (2014). Mathe-
matical modeling and optimization of a vehicle crash
test based on a single-mass. In Proceeding of the 11th
World Congress on Intelligent Control and Automa-
tion, pages 3588–3593. IEEE.
Marzbanrad, J. and Pahlavani, M. (2011). A system identifi-
cation algorithm for vehicle lumped parameter model
in crash analysis. International Journal of Modeling
and Optimization, 1(2):163.
Mentzer, S. G., Radwan, R. A., and Hollowell, W. T. (1992).
The sisame methodology for extraction of optimal
lumped parameter structural crash models. Technical
report, SAE Technical Paper.
Munyazikwiye, B. B., Karimi, H. R., and Robbersmyr,
K. G. (2013). Mathematical modeling of vehicle
frontal crash by a double spring-mass-damper model.
In 2013 XXIV International Conference on Informa-
tion, Communication and Automation Technologies
(ICAT), pages 1–6. IEEE.
Munyazikwiye, B. B., Karimi, H. R., and Robbersmyr,
K. G. (2017). Application of genetic algorithm on pa-
rameter optimization of three vehicle crash scenarios.
IFAC-PapersOnLine, 50(1):3697–3701.
Noorsumar, G., Robbersmyr, K., Rogovchenko, S., and
Vysochinskiy, D. (2020). Crash response of a repaired
vehicle-influence of welding uhss members. Techni-
cal report, SAE Technical Paper.
Pawlus, W., Karimi, H. R., and Robbersmyr, K. G.
(2011). Development of lumped-parameter mathe-
matical models for a vehicle localized impact. Journal
of mechanical science and technology, 25(7):1737–
1747.
Riegl, P. and Gaull, A. (2018). Modeling and validation of
a complex vehicle dynamics model for real-time ap-
plications. In Proceedings of 8th International Con-
ference on Simulation and Modeling Methodologies,
Technologies and Applications - SIMULTECH,, pages
403–413. INSTICC, SciTePress.
Savaresi, S. M., Poussot-Vassal, C., Spelta, C., Sename, O.,
and Dugard, L. (2010). Semi-active suspension con-
trol design for vehicles. Elsevier.
A Novel Technique for Modeling Vehicle Crash using Lumped Parameter Models
69