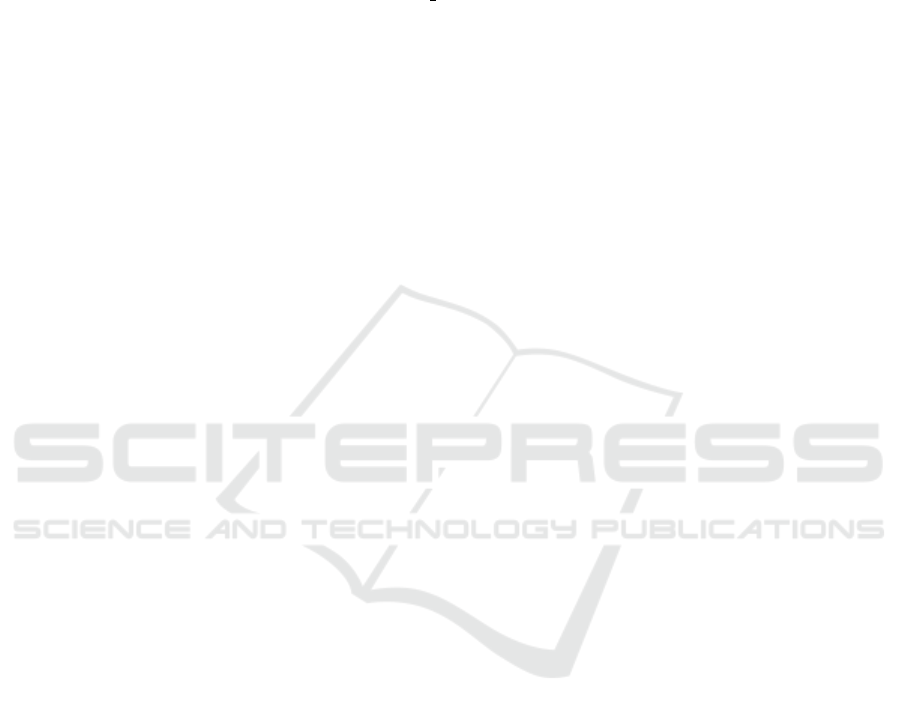
Innovation on Accessible and Low Cost Deflection Measurement Devices
Sukamto
1
, Juriah Mulyanti
1
and Nizar Achmad
2
1
Department of Mechanical Engineering, Janabadra University, Yogyakarta 55231, Indonesia
2
Department of Civil Engineering, Janabadra University, Yogyakarta 55231, Indonesia
{kamto ,jm.yanti, nizar achmad }@janabadra.ac.id
Keywords:
Optic mouse, deflection, innovation, low cost, measurement device modification
Abstract:
Deflection occurs mostly in structures, especially those that accept lateral loads. Excessive deflection can
cause damage, especially in the supporting structure therefore deflection must be measured but the deflection
measurement device is still expensive so the application is limited. Modification of the deflection measurement
device can be done using an optical mouse. The ability of optical mouse is expressed in the ability to scan the
number of points in each area, the bigger the smaller the displacement that can be measured. we use a cheap
mouse and the results show the mouse is able to measure deflection to accuracy of about 0.04 mm. Optical
mouse is cheap so it is expected to use it more widely, except for practitioners and universities, it is hoped that
it can also be used in vocational schools where the needs are large but the budget are limited.
1 INTRODUCTION
Monitoring of building structure deformation and
durability testing of materials and structures is a
very important process in development and produc-
tion with the aim of maintaining safety and strength
of the structure. Deflection occurs a lot in structures
that cause deformation so it needs to be monitored
by measuring it, especially when receiving maximum
loads. Fibre optic sensors used for monitoring bridges
(Yoneyama and Ueda, 2012). However the cost of fi-
bre optic sensors is too high and the installation of
the sensors is not easy for existing bridges. Another
approach to bridge deflection measurement is the use
of noncontact measurement method for example pho-
togrammetry, moir
´
e and laser scanning. A laser sys-
tem has a potential to measure deflection distribution
of bridge by scanning, however, at higher cost. Struc-
tural deflections represent a critical response param-
eter often measured for structural health monitoring
(Attanayake et al., 2011). Laser tracker records po-
sition coordinates at few discrete points while laser
scanner captures points of clouds representing de-
formed and undeformed shapes of a structure. These
technologies present distinctive advantages, capabili-
ties and limitations for field applications. Innovations
in deflection measurement devices that are low cost
(Guo and Wei, 2015) have to be created. This re-
search tries to make a cheap deflection measurement
device from a computer mouse. This aims to expand
the use of these devices in practical and academic en-
vironments. This research is limited to the use of op-
tical mouse to read shift points only in one direction
(Ali and Al-garni, 1996), (Simm et al., 2016). Com-
puter mouse that are modified only for one-way shifts.
It is mainly for measuring very small distances. De-
flection is very small, so it is precisely measured by
this tool. The depth of drilling holes that require high
accuracy can also be measured with this tool (Peng
et al., 2007). There are still many kinds of very small
distance measurements in daily work. This can be
seen from the development of tools that are getting
smaller in size so that the size needs to beaccurate in
the design and manufacture. Vocational school stu-
dents and university students really need to develop
skills in designing and manufacturing tools or ma-
chines. Of course this cannot be separated from the
use of measuring instruments. A cheap measuring in-
strument can be used even though it is not as precise
as a high-tech measuring instrument which of course
is expensive. However, the main objective is for stu-
dents to master the basic principles of measurement
that will not be separated from design. Cheap measur-
ing instruments are expected to be used more widely
so that it will increase the number of students who
have better skills to support their future. The rest of
this paper is structured as follows. After this intro-
duction of study, some previous study related to this
research are presented in theoretical background, ma-
terials and methods. Result and discussion presents
Sukamto, ., Mulyanti, J. and Achmad, N.
Innovation on Accessible and Low Cost Deflection Measurement Devices.
DOI: 10.5220/0009879601390142
In Proceedings of the 2nd International Conference on Applied Science, Engineering and Social Sciences (ICASESS 2019), pages 139-142
ISBN: 978-989-758-452-7
Copyright
c
2020 by SCITEPRESS – Science and Technology Publications, Lda. All rights reserved
139